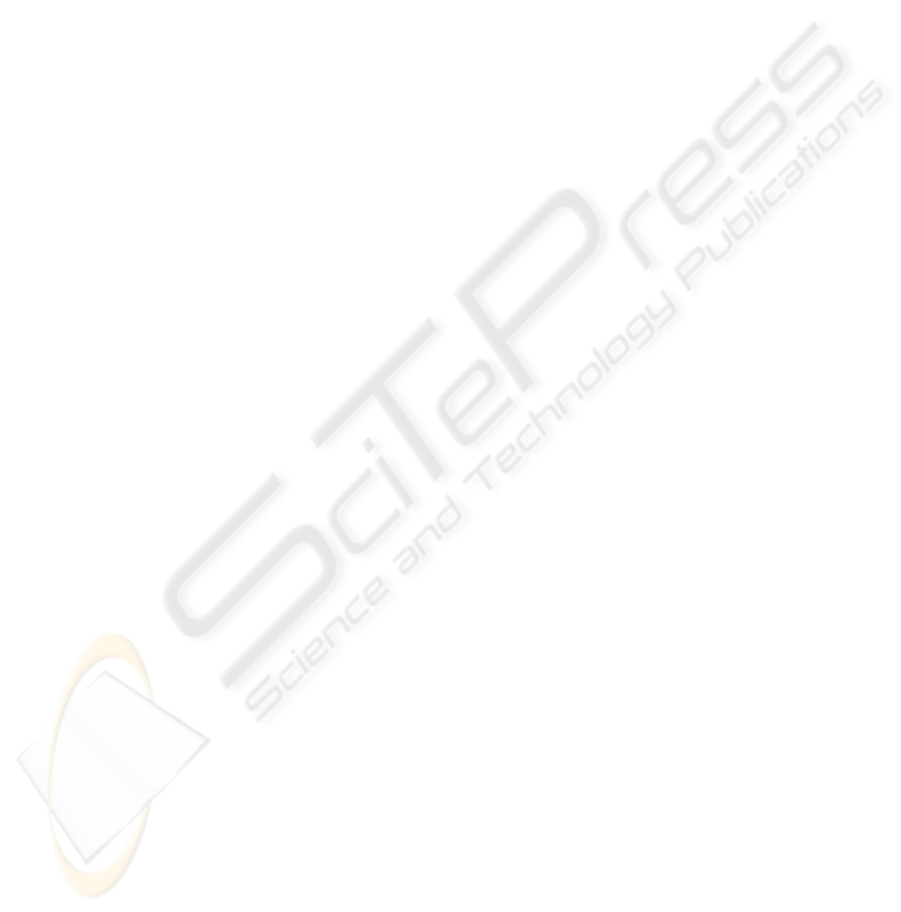
5 CONCLUSION
In this paper, two identification methods have been
tested and compared: the first based on the ordinary
LS technique associated with an appropriate data
treatment and the second based on the SRIV method.
Both methods give interesting and reliable results.
Hence, we can choose these techniques for a
parametric identification.
In addition, the authors have introduced a simple
calculation which enables us to know the parameters
which are sensitive to noises and undesirable effects.
Future works concern the use of both techniques to
identify a 6 degrees of freedom robot.
REFERENCES
Garnier H., Gilson M. and Huselstein E., 2003.
“Developments for the MATLAB CONTSID
toolbox”, In: 13th IFAC Symposium on System
Identification, SYSID 2003, Rotterdam Netherlands,
August 2003, pp. 1007-1012
Garnier H., Gilson M. and Cervellin O., 2006. “Latest
developments for the MATLAB CONTSID toolbox”,
In: 14th IFAC Symposium on System Identification,
SYSID 2006, Newcastle Australia, March 2006, pp.
714-719
Gautier M. and Khalil W., 1990. "Direct calculation of
minimum set of inertial parameters of serial robots",
IEEE Transactions on Robotics and Automation, Vol.
6(3), June 1990
Gautier M. and Khalil W., 1991. “Exciting trajectories for
the identification of base inertial parameters of
robots”, In: Proc. Of the 30
th
Conf. on Decision and
Control, Brigthon, England, December 1991, pp. 494-
499
Gautier M., 1997. “Dynamic identification of robots with
power model”, Proc. IEEE Int. Conf. on Robotics and
Automation, Albuquerque, 1997, p. 1922-1927
Gautier M., Khalil W. and Restrepo P. P., 1995.
“Identification of the dynamic parameters of a closed
loop robot”, Proc. IEEE on Int. Conf. on Robotics and
Automation, Nagoya, may 1995, p. 3045-3050
Gilson M., Garnier H., Young P.C. and Van den Hof P.,
2006. “A refined IV method for closed loop system
identification”, In: 14th IFAC Symposium on System
Identification, SYSID 2006, Newcastle Australia,
March 2006, pp. 903-908
Hampel F.R., 1971. “A general qualitative definition of
robustness”, Annals of Mathematical Statistics, 42,
1887-1896, 1971
Huber P.J., 1981. “Robust statistics”, Wiley, New-York,
1981
Janot A., Bidard C., Gautier M., Keller D. and Perrot Y.,
2006. “Modélisation, Identification d’une Interface
Médicale”, Journées Identification et Modélisation
Expérimentale 2006, Poitiers, November 2006
Khatounian F., Moreau S., Monmasson E., Janot A. and
Louveau F., 2006. “Simultaneous Identification of the
Inertial Rotor Position and Electrical Parameters of a
PMSM for a Haptic Interface”, In: 12
th
EPE-PEMC
Conference, Portoroz, Slovenia, August September
2006, CD-ROM, ISBN 1-4244-0121-6
Lemaire Ch.E., Vandanjon P.O., Gautier M. and Lemaire
Ch., 2006. “Dynamic Identification of a Vibratory
Asphalt Compactor for Contact Efforts Estimation”,
In: 14th IFAC Symposium on System Identification,
SYSID 2006, Newcastle Australia, March 2006,pp.
973-978
Mili L., Phaniraj V. and Rousseeuw P.J., 1990. “Robust
estimation theory for bad data diagnostics in electrical
power systems”, In: C. T. Leondes editor, Control and
Dynamic Systems:Advances in Theory and
Applications, pp. 271-325, San Diego 1990, Academic
Press
Mili L., Cheniae M.G., Vichare N.S. and Rousseeuw P.J.,
1996. “Robust state estimation based on projection
statistics”, IEEE Trans. On Power Systems, 11(2),
1118-1127, 1996
Specht R., and Isermann R., 1988. “On-line identification
of inertia, friction and gravitational forces applied to
an industrial robot”, Proc. IFAC Symp. on Robot
Control, SYROCO’88, 1988, p. 88.1-88.6
Young P.C. and Jakeman A.J., 1979. Refined instrumental
variable methods of time-series analysis: Part 1, SISO
systems, International Journal of Control, 29:1-30,
1979
Young P.C., 2006. “An instrumental variable approach to
ARMA model identification and estimation”, In: 14th
IFAC Symposium on System Identification, SYSID
2006, Newcastle Australia, March 2006, pp. 410-415
COMPARISON OF TWO IDENTIFICATION TECHNIQUES: THEORY AND APPLICATION
347