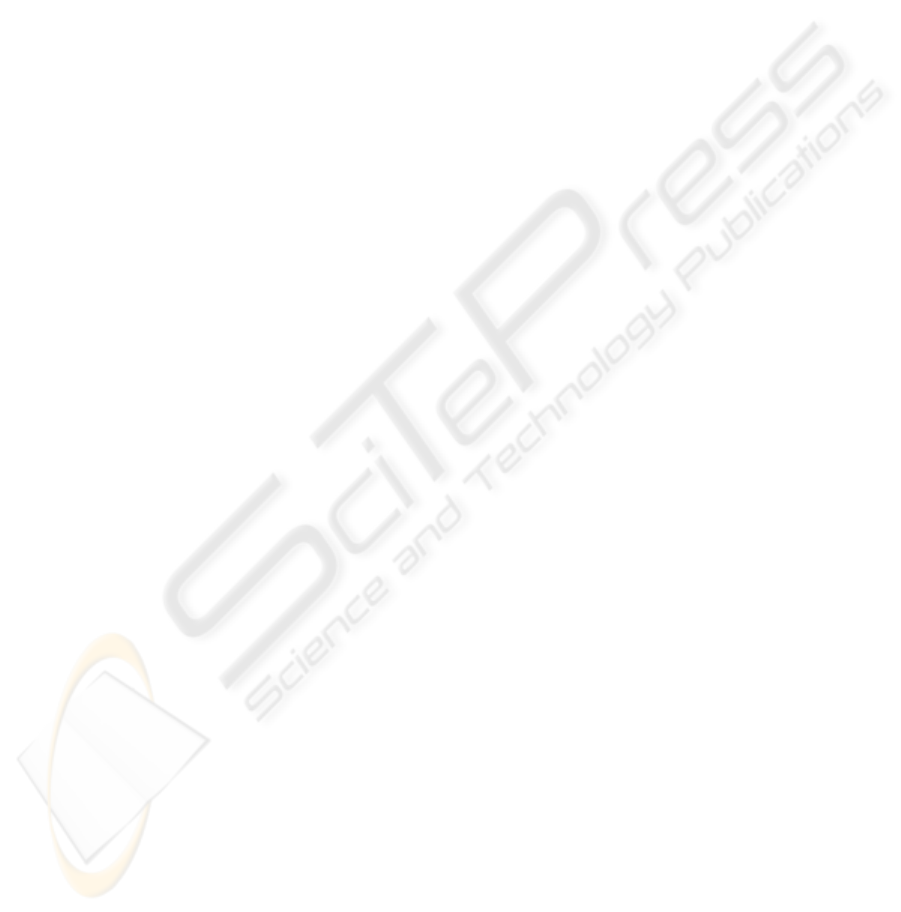
5. Sandia National Laboratories: Java Expert System Shell. http://herzberg.ca.sandia.gov/jess.
6. Waikato Environment for Knowledge Analysis Project, www.cs.waikato.ac.nz/~ml.
7. Hitachi develops RFID powder, www.pinktentacle.com/2007/02/hitachi-develops-rfid-
powder.
8. Bodhuin, T., Canfora, G., Preziosi, R., and Tortorella, M. An Extensible Ubiquitous Archi-
tecture for Networked Devices in Smart Living Environments. In Proceedings of Embed-
ded and Ubiquitous Computing, International Conference (Nagasaki, Japan, December 6-9,
2005). EUC ‘05, LNCS 3823, Springer-Verlag (2005) 21-30.
9. Bodhuin, T., Canfora, G., Preziosi, R., and Tortorella, M. Hiding complexity and heteroge-
neity of the physical world in smart living environments. In Proceedings of the 2006 ACM
Symposium on Applied Computing (Dijon, France, April 23 - 27, 2006). SAC '06. ACM
Press, New York, NY (2006) 1921-1927.
10. Curtin, J., Kauffman, R. J., Riggins, F. J. Making the most out of RFID technology: A
research agenda for the study of the adoption, usage and impact of RFID. Minneapolis, 11.
Carlson School of Management, University of Minnesota (October 30 2005).
www.misrc.umn.edu/workingpapers/fullpapers/2005/0522_103005.pdf.
11. Hamblen, M., RFID successes highlighted at Mobile&Wireless World. Computerworld
(May 2006), www.computerworld.com/action/article.do?command=viewArticleBasic& arti-
cleId =9000767.
12. Juels, A., Rivest, R. L., and Szydlo, M. The blocker tag: selective blocking of RFID tags
for consumer privacy. In Proceedings of the 10th ACM Conference on Computer and
Communications Security (Washington D.C., USA, October 27 - 30, 2003). CCS '03. ACM
Press, New York, NY (2003) 103-111.
13. Kallender, P., Japanese bank taps RFID for document security. InfoWorld (August 18,
2004). http://www.infoworld.com/article/04/08/18/HNjapanrfid_1.html [April 15 2007].
14. Kirk, J., RFID tags vulnerable to viruses, study says Attacks could soon come in the form
of a SQL injection or a buffer overflow attack. Computerworld (March 2006).
www.computerworld.com/mobiletopics/mobile/story/0,10801,109560,00.html.
15. Quaadgras, A. 2005. Who Joins the Platform? The Case of the RFID Business Ecosystem.
In Proceedings of the Proceedings of the 38th Annual Hawaii international Conference on
System Sciences (Hicss'05) - Track 8 - Volume 08 (January 03 - 06, 2005). HICSS. IEEE
Computer Society, Washington, DC (2005) 269.2.
16. Rieback, M. R., Crispo, B., and Tanenbaum, A. S. 2006. Is Your Cat Infected with a Com-
puter Virus?. In Proceedings of the Fourth Annual IEEE international Conference on Per-
vasive Computing and Communications (Pisa, Italy March 13 - 17, 2006). Percom'06.
IEEE Computer Society (2006).
17. Songini, M., Wal-Mart details its RFID journey. Computerworld (March 2006).
www.computerworld.com/industrytopics/retail/story/0,10801,109132,00.html?from=story_kc
18. Wang, S., Chen, W., Ong, C., Liu, L., and Chuang, Y. RFID Application in Hospitals: A
Case Study on a Demonstration RFID Project in a Taiwan Hospital. In Proceedings of the
39th Annual Hawaii international Conference on System Sciences - Volume 08 (January 04
- 07, 2006). HICSS. IEEE Computer Society, Washington, DC (2006).
24