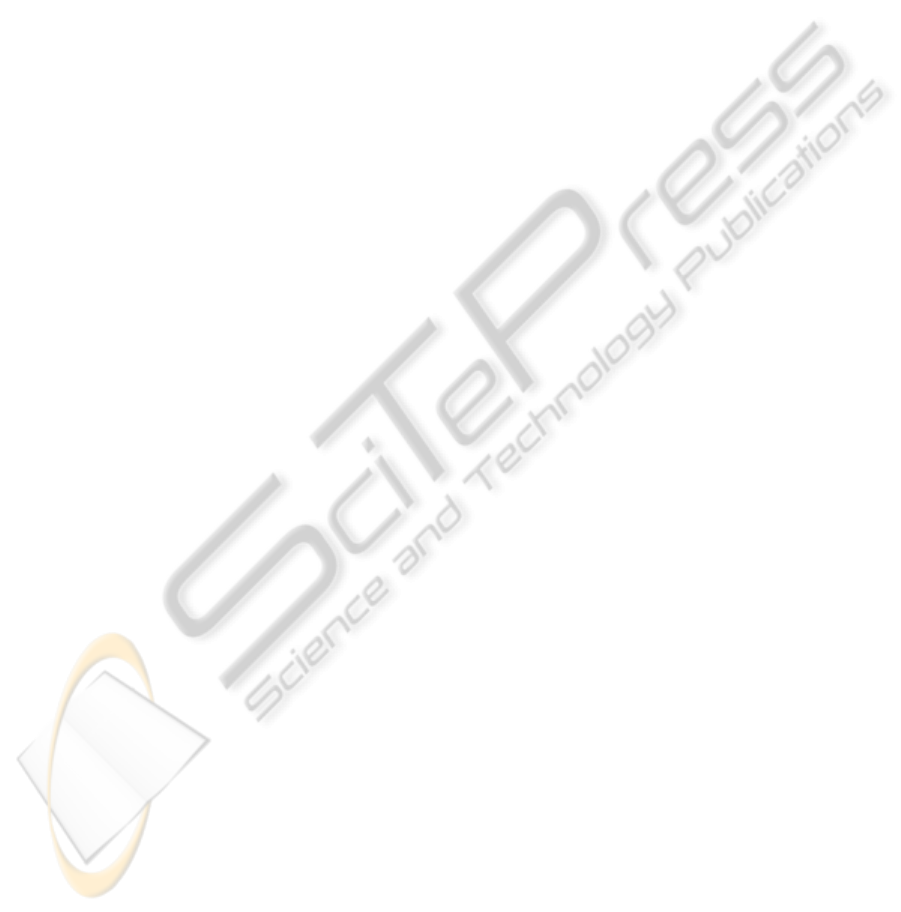
decreased; i.e. for F
aero
= 1800 N the need in
temperature for the maximum vertical displacement
obtaining is approximately 90˚C.
The final configuration of the integrated
controller was a combination of a bi-positional
controller (particularly an on-off one) and a PI
(proportional-integral) controller, due to the two
phases (heating and cooling) of the SMA wires
interconnection. The resulted controller must behave
like a switch between cooling phase and heating
phase, situations where the output current is 0 A, or
is controlled by a law of PI type.
Using an integral criterion, the error minimum
surface criterion (Ziegler-Nichols), the PI controller
for the heating phase was optimal tuned, the resulted
values are K
P
=1792.8 and K
I
=787.0061. Evaluating
the systems’ performances one observed that the
poles of closed loop transfer function of the
controlled heating phase resulted with the values
(14) are all placed in the left-hand side of the s-
plane, so the obtained system is stable. On the other
way, the system was found to be completely
controllable and observable based on the values
established in equations (17)÷(19). So, the final form
of the integrated controller law was (20).
Loading the numerically simulated general
model (the non-linear one with F
pretension
=1500N) in
Fig. 8 with aerodynamic force F
aero
= 1500N, the
obtained characteristics in Fig. 10 confirm that the
controller works good, the transition to the desired
steady-state being significantly improved through
the integration of the two control law in the equation
(20): 1) the amplitudes of oscillations were reduced
and the observed oscillations in the SMA
temperatures around the steady-state are due only to
the thermal inertia of the smart material; 2) the
values of the transition time from 0mm to the
steady-state values decrease from 20÷25 to
approximate 5 s.
As second and third validation methods a bench
test and a wind tunnel test were performed and will
be presented in the second part of the paper, related
to the experimental validation.
ACKNOWLEDGEMENTS
We would like to thank the Consortium of Research
in the Aerospatial Industry in Quebec (CRIAQ),
Thales Avionics, Bombardier Aerospace, and the
National Sciences and Engineering Research
Council (NSERC) for the support that made this
research possible. We would also like to thank
George Henri Simon for initiating the CRIAQ 7.1
project and Philippe Molaret from Thales Avionics
and Eric Laurendeau from Bombardier Aeronautics
for their collaboration on this work.
REFERENCES
Chang, P., Shah, A., Singhee, M., 2009, Parameterization
of the Geometry of a Blended Wing Body Morphing
Wing, Project report, Georgia Institute of Technology,
April 2009, Atlanta, Georgia, USA
Georges, T., Brailovski, V., Morellon, E., Coutu, D.,
Terriault, P., 2009, Design of Shape Memory Alloy
Actuators for Morphing Laminar Wing With Flexible
Extrados, Journal of Mechanical Design, Vol. 31, Nº 9
Gonzalez, L., 2005, Morphing Wing Using Shape Memory
Alloy: a concept proposal, Final research paper, Texas
A&M University, College Station, Texas, USA
Grigorie, T. L., Botez, R. M., 2009, Adaptive neuro-fuzzy
inference system-based controllers for smart material
actuator modeling, Journal of Aerospace Engineering,
Vol. 223, No. 6, pp. 655-668
Hinshaw, T. L., 2009, Analysis and Design of a Morphing
Wing Tip using Multicellular Flexible Matrix
Composite Adaptive Skins, Master of Science Thesis,
Virginia Polytechnic Institute and State University,
Virginia, USA
Khalid, M., Jones, D. J., 1993, Navier Stokes Investigation
of Blunt Trailing Edge Airfoils using O-Grids, AIAA
Journal of Aircraft, vol.30, no.5, pp. 797-800
Khalid, M., Jones, D. J., 1993, A CFD Investigation of the
Blunt Trailing Edge Airfoils in Transonic Flow,
Inaugural Conference of the CFD Society of Canada.
Majji, M., Rediniotis, O. K., Junkins, J.L., 2007, Design of
a Morphing Wing: Modeling and Experiments, AIAA
Atmospheric Flight Mechanics Conference and
Exhibit, Hilton Head, South Carolina, USA
Mihoc, D., 1980, Teoria si elementele sitemelor de reglare
automata. Editura Didactica si Pedagogica, Bucuresti
Namgoong, H., Crossley, W. A., Lyrintzis, A. S., 2006,
Aerodynamic Optimization of a Morphing Airfoil
Using Energy as an Objective, 44th AIAA Aerospace
Sciences Meeting and Exhibit, Reno, Nevada, USA
Popov, A. V., Labib, M., Fays, J., Botez, R. M., 2008,
Closed-Loop Control Simulations on a Morphing
Wing, Journal of Aircraft, Vol. 45, pp. 1794-1803
Ruotsalainen, P., et. al., 2009, Shape Control of a FRP
Airfoil Structure Using SMA-Actuators and Optical
Fiber Sensors. Journal of Solid State Phenomena,
Volume 144, pp. 196-201
Smith, K., Butt, J., Spakovsky, M. R., Moorhouse, D.,
2007, A Study of the Benefits of Using Morphing Wing
Technology in Fighter Aircraft Systems, 39th AIAA
Thermophysics Conference, Miami, Forida, USA
Terriault, P., Viens, F., Brailovski, V., 2006, Non-
isothermal Finite Element Modeling of a Shape
Memory Alloy Actuator Using ANSYS, Computational
Materials Science, Vol. 36, No. 4, pp. 397-410
ICINCO 2010 - 7th International Conference on Informatics in Control, Automation and Robotics
12