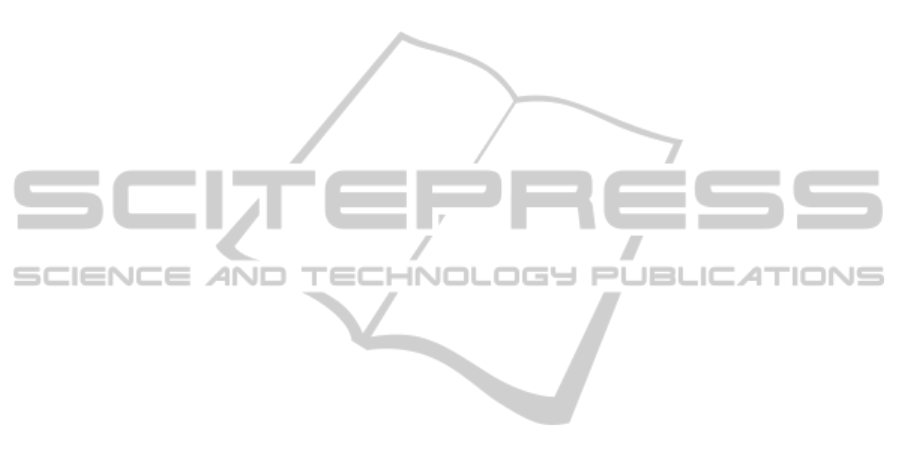
analysis of five characteristics was used: Sector,
Technology, Practical Application, Production Phase
and Benefit.
By way of conclusion, we can state that IoT is a
new research field in production systems. It is
possible to find general proposals for a wide range
of industrial sectors, but also a specific proposal for
given industrial sectors. However, very few of these
proposals have had a real application in industry.
The predominant technologies in the application
of IoT for production systems are RFID and sensors.
Regarding the planning, operation and control
phases in production systems, the application of IoT
focuses mainly on the control phase.
Most of the found proposals are applications to
production control, followed by quality control and
stock control. All the authors indicate that IoT
applications contribute with benefits in production
systems. These benefits are not only for better
management information in production (e.g., real-
time information or improving information quality),
but also benefits for other aspects of the production
system (e.g., reducing production costs and
improving efficiency).
In this review, some gaps in the literature on IoT
application in production system have been
identified. Based on these gaps and seeing how IoT
applications can help managers of the production
system, some near future lines of research arise: 1)
most proposals are general for the production of any
company, but there are very few applied proposals;
2) the predominant technology used to implement
IoT is RFID. Although it offers many advantages,
IoT with other technologies would be interesting for
it to be applied or combined with it; 3) some
industrial sectors, where experiments with IoT are
being done, have been identified, but new research
works could be conducted in other industrial sectors;
4) IoT Applications in the production area
concentrate mainly on the control phase. Hence
further research should also be conducted in
planning and operation phases and subphases.
ACKNOWLEDGEMENT
This research has been carried out in the framework
of the project PAID-06-21 Universitat Politècnica de
València and GV/2014/010 Generalitat Valenciana
(Emergent Research Groups)
REFERENCES
Atzori, L., Iera, A., & Morabito, G. (2010). The Internet of
Things: A survey. Computer Networks, 54.
Cao, Y. L., Li, W. F., & Song, W. (2011). Research on
Materials Tracking in Toy Production Based on the
Internet of Things. Advanced Materials Research,
314-316.
Carnevalli, J. A., & Miguel, P. C. (2008). Review, analysis
and classification of the literature on QFD—Types of
research, difficulties and benefits. Int. Journal of
Production Economics, 114.
Castro, M., Guillen, A., Fuster, J. L., Jara, A. J., Zamora,
M. A., & Skarmeta, A. F. G. (2011). Oxygen
Cylinders Management Architecture Based on Internet
of Things. In 2011 Int. Conf. on Computational
Science and Its Applications (ICCSA).
Cuatrecasas, L. (1994). Organización y gestión de la
producción en la empresa actual. Barcelona: CPET.
Cuiyun, M., & Yuanhang, H. (2010). Discussion on the
Application of Internet of Things in Logistics
Production Management. In 2010 Int. Conf. on E-
Business and E-Government (ICEE).
Gubbi, J., Buyya, R., Marusic, S., & Palaniswami, M.
(2013). Internet of Things (IoT): A vision,
architectural elements, and future directions. Future
Generation Computer Systems, 29.
Houyou, A. M., Huth, H.-P., Trsek, H., Kloukinas, C., &
Rotondi, D. (2012). Agile manufacturing: General
challenges and an IoT@Work perspective. In 2012
IEEE 17th Conf. on Emerging Technologies Factory
Automation (ETFA).
Hu, T., Zheng, M., & Zhu, L. (2011). Research
Application of the Internet of Things Monitor Platform
in Meat Processing Industry. In J. J. Park, H. Jin, X.
Liao, & R. Zheng (Eds.), Proceedings of the Int. Conf.
on Human-centric Computing 2011 and Embedded
and Multimedia Computing 2011. Springer
Netherlands.
Isenberg, M.-A., Werthmann, D., Morales-Kluge, E., &
Scholz-Reiter, B. (2011). The Role of the Internet of
Things for Increased Autonomy and Agility in
Collaborative Production Environments. In D.
Uckelmann, M. Harrison, & F. Michahelles (Eds.),
Architecting the Internet of Things. Springer Berlin
Heidelberg.
Lee, C. K. H., Choy, K. L., Law, K. M. Y., & Ho, G. T. S.
(2012). An intelligent system for production resources
planning in Hong Kong garment industry. In IEEE Int.
Conf. on Industrial Engineering and Engineering
Management.
Liu, J., & Xu, W. (2013). Technical State Monitoring and
Evaluation of Aerospace Product Manufacturing
Workshop Based on Internet of Things. In Green
Computing and Communications (GreenCom), 2013
IEEE and Internet of Things (iThings/CPSCom), IEEE
Int. Conf. on and IEEE Cyber, Physical and Social
Computing.
Lvqing, Y. (2011). The analysis and design of machinery
production monitoring system based on Internet of
ICEIS2015-17thInternationalConferenceonEnterpriseInformationSystems
336