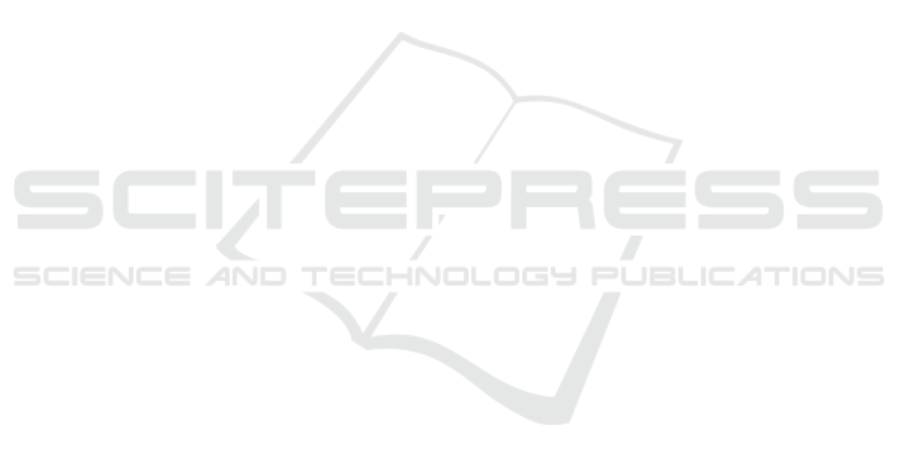
A Proposal based on Frequency Response for Multi-Model
Controllers
Anderson Luiz de Oliveira Cavalcanti
Federal University of Rio Grande do Norte, Natal, RN, Brazil
Keywords: MPC, Multi Model Control.
Abstract: This paper presents an alternative approach to control nonlinear plants. The nonlinear system to be
controlled is decomposed into a number of operating points and a GPC controller is properly designed,
based on local linear model for each point. A metric based on frequency response of each local linear model
is proposed in order to consider the contribution of each local controller in the signal sent to the plant. Two
applications are presented. The first application in a simulated plant consists of a continuous stirred tank
reactor (CSTR) and the second consists of a coupled tanks system level control.
1 INTRODUCTION
In the industry are found processes that work in
large operating ranges. Batch processes (Foss et al.,
1995), as chemical reactors, are classic examples of
this type of process. The main solution in these cases
would be to obtain a non-linear complex model,
requiring, in the case of using predictive controllers,
the use of nonlinear prediction and optimization,
which is not a trivial task (Camacho and Bordons,
1999).
In order to provide a simpler solution for the
problems mentioned above, a known approach, in
academia, as multi-models approach has been
investigated (Boling et al., 2007), (Dougherty and
Cooper, 2003a), (Dougherty and Cooper, 2003b),
(Arslan et al., 2004) and (Normey- Bravo and Rich,
2009). This approach seeks to decompose the
process range of operating at various operating
points usual in the same place and obtain a valid
model for each of these points. A validation
function, called a metric is defined to indicate what
is the most appropriate model at a given moment of
sampling. Such a metric is used to calculate
weighting factors, the application of which will be
described below. There are basically two types of
multi-model approaches, which will be detailed
below also.
The first approach uses the weighting factors to
compute a global model formed by the convex
combination of local models obtained and a single
controller is designed from said master (Foss et al.,
1995) (Azimadeh et al., 1998) (Dumitrache and
Constantine, 2000) (Pickhardt, 2000) and
(Cavalcanti et al., 2007a).
The second type of approach designs a suitable
controller for each model of each operating point. In
this case, the control signal to the process is a
convex combination of the computed control signals
(Cavalcanti et al., 2007b), (Cavalcanti et al., 2008),
(Arslan et al., 2004), (Wen et al., 2006), (Dougherty
and Cooper, 2003) and (Dougherty and Cooper,
2003b).
This article is based on the second type of
approach mentioned. Most existing literature are
based on the metrics or statistics of the process (Foss
et al., 1995) or standards (Dougherty and Cooper,
2003) (Dougherty and Cooper, 2003b), (Arslan et
al., 2004) (Cavalcanti et al., 2007b) and (Cavalcanti
et al., 2008). This work, in particular, consider the
frequency response of each local model compared to
the frequency response of each current approximate
model obtained by interpolation at each sampling
instant.
The choice of use of a predictive controller based
on the highlight that this is gaining in terms of
industrial applications (García, Prett and Morari,
1989). This highlight is observed as the same, and
can be applied in a wide range of processes,
including processes with long delays and non-
minimum phase, you can easily incorporate the
constraint treatment in the problem formulation
(Camacho and Bordons 1999).
223
Luiz de Oliveira Cavalcanti A..
A Proposal based on Frequency Response for Multi-Model Controllers.
DOI: 10.5220/0005546202230229
In Proceedings of the 12th International Conference on Informatics in Control, Automation and Robotics (ICINCO-2015), pages 223-229
ISBN: 978-989-758-122-9
Copyright
c
2015 SCITEPRESS (Science and Technology Publications, Lda.)