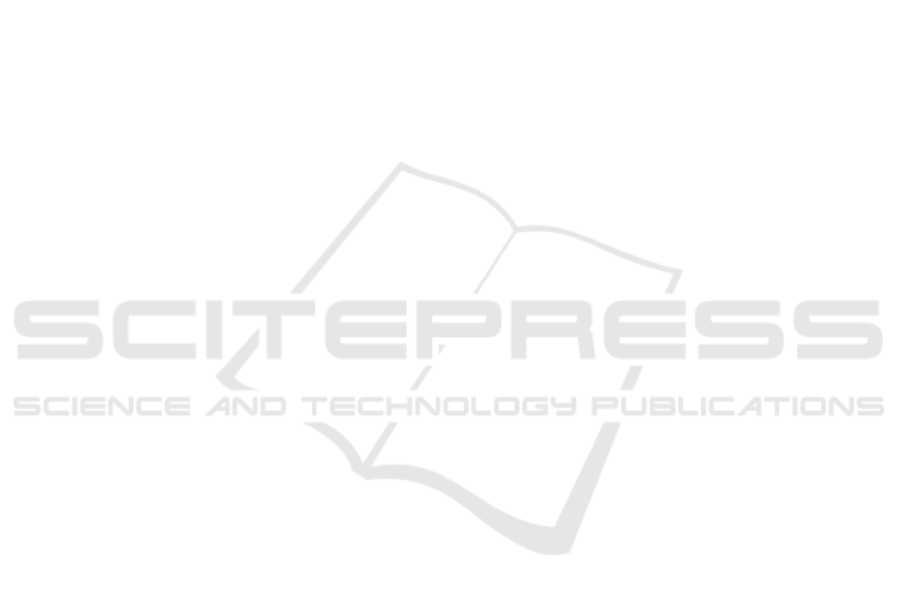
A New Device for Hydrogen Production on Demand with Application
to Electric Assist Bike: Description, Production Characteristics and
Basic Control
Jocelyn Sabatier
1
, Fabrice Mauvy
2
, Jean-Louis Bobet
2
, Damien Mohedano
3
,
Matthieu Faessel
3
and Frédéric Bos
3
1
Bordeaux University, IMS Lab., UMR 5218 CNRS, 351 Cours de la Libération, 33405 Talence, France
2
CNRS, ICMCB Lab, UPR 5026, 87 Avenue du Dr Albert Schweitzer, 33600 Pessac, France
3
Bordeaux University, TechnoShop Coh@bit platform, Bordeaux Institute of Technology,
15 Rue Naudet, 33750 Gradignan, France
Keywords: Hydrogen, PEM Fuel Cell, Production on Demand, Water Hydrolysis, Magnesium.
Abstract: Using a magnesium-based hydrolysis reaction that spontaneously produces hydrogen with a high kinetic and
a high efficiency, this paper proposes a solution to supply a PEM fuel cell that permits production on
demand. This solution is an instrumented reactor that uses capsules with magnesium powder and that
controls the hydrolysis reaction in order to maintain a constant pressure. The hydrogen produced by the
reactor is used to feed a PEM fuel cell in which variable electric loads are applied. By solving both the
hydrogen supply and storage problems, such a system is particularly suitable for light mobility applications.
1 INTRODUCTION
Urban travel covers a significant economic reality.
The last mile represents almost 20% of the total cost
of the freight value chain. In France, it accounts for
about 20% of the traffic, occupies 30% of the road
network and is responsible for 25% of greenhouse
gas emissions (Roullé and Lorrillard, 2012). The last
mile problem of goods and persons thus raises many
essential issues - economic, environmental, societal
and urbanistic - that the authorities are trying to
solve with electric vehicle such as bicycle or
tricycle. As the recharging of these means of
transport is a lengthy process, dihydrogen (H
2
)
coupled with a fuel cell as a source of fuel is thus
often considered.
Hydrogen mobility is seen by many as a solution
for the future. Indeed, the modularity of hydrogen
(used directly or indirectly via a fuel cell), its high
combustion energy (3 times that of hydrocarbons)
and its non-polluting nature make it a very
promising fuel. However, three major problems
hinder the large-scale development of this
technology.
Environment: 95% of the hydrogen currently
produced comes from steam reforming of natural gas
which does not solve environmental problems. The
production of hydrogen without an environmental
impact therefore remains an important issue
Refueling: In a country such as France, there are
only very few points where hydrogen refueling is
possible.
Storage: Hydrogen can be stored under pressure
or in liquid form, which in both cases causes storage
safety and/or cost problems, or in solid form in
hydrides, which solves the safety question but
induces a large tank mass constraint. In any case, the
volume of the tank will be larger than a tank of
hydrocarbons.
The work described in this paper provides an
answer in the area of electric assistance for bikes or
tricycles or more generally for light mobility. In
such applications, the hydrogen must be produced
on demand, as the PEM fuel cell needs to consume it
to produce electrical energy, to avoid any storage
constraints. To reach this goal, the hydrogen is
produced by the help of water hydrolysis. In order to
control the reaction, a dedicated reactor was
designed. This reactor has been implemented in a
Sabatier, J., Mauvy, F., Bobet, J-L., Mohedano, D., Faessel, M. and Bos, F.
A New Device for Hydrogen Production on Demand with Application to Electric Assist Bike: Description, Production Characteristics and Basic Control.
DOI: 10.5220/0006846304110419
In Proceedings of the 15th International Conference on Informatics in Control, Automation and Robotics (ICINCO 2018) - Volume 1, pages 411-419
ISBN: 978-989-758-321-6
Copyright © 2018 by SCITEPRESS – Science and Technology Publications, Lda. All rights reserved
411