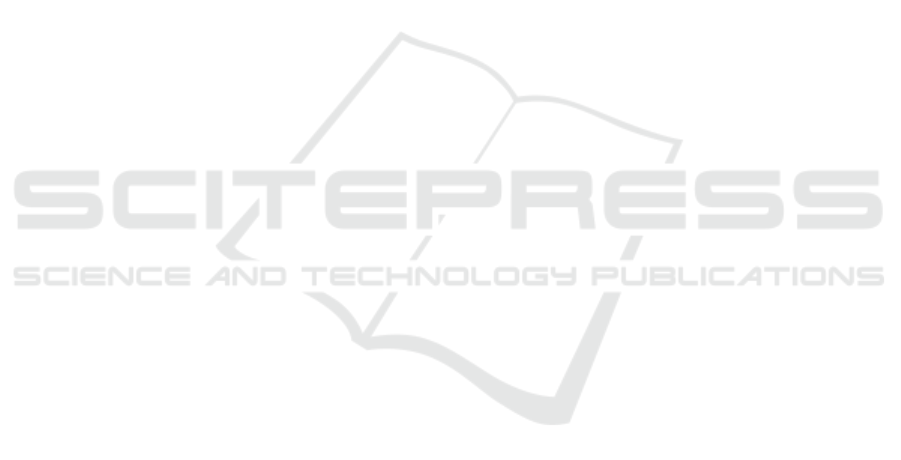
step is the design of a high-performance algorithm for
the parameters estimation, more robust with respect
of the presence of noise and of model parameters un-
certainties.
REFERENCES
Bagolini, A., Bellutti, P., Di Giamberardino, P., Rudas,
I.J.and DAndrea, V., Verotti, M., Dochshanov, A., and
Belfiore, N. (2018). Stiffness characterization of bi-
ological tissues by means of mems-technology based
micro grippers under position control. In Mechanisms
and Machine Science, volume 49, pages 939 – 947.
Bagolini, A., Ronchin, S., Bellutti, P., Chiste, M., Ver-
otti, M., and Belfiore, N. (2017). Fabrication of no-
vel mems microgrippers by deep reactive ion etching
with metal hard mask. IEEE J. Microelectromechani-
cal Syst., 26:926 – 934.
Boonvisut, P. and C¸ avus¸o
ˇ
glu, M. C. (2013). Estimation of
soft tissue mechanical parameters from robotic mani-
pulation data. IEEE/ASME Transactions on Mecha-
tronics, 18(5):1602–1611.
Cao, S., Luo, Z., and Quan, C. (2015). Estimation of an
objects physical parameter by force sensors of a dual-
arm robot. In Proceedings of the 2015 IEEE Confe-
rence on Robotics and Biomimetics.
Cecchi, R., Verotti, M., Capata, R., Dochshanov, A., Brog-
giato, G. B., Crescenzi, R., Balucani, M., Natali, S.,
Razzano, G., Lucchese, F., et al. (2015). Develop-
ment of micro-grippers for tissue and cell manipula-
tion with direct morphological comparison. Microma-
chines, 6(11):1710–1728.
Choi, D.-K. (2016). Mechanical characterization of biolo-
gical tissues: Experimental methods based on mathe-
matical modeling. Biomedical Engineering Letters,
6(3):181–195.
Di Giamberardino, P., Bagolini, A., Bellutti, P., Rudas, I. J.,
Verotti, M., Botta, F., and Belfiore, N. P. (2018). New
mems tweezers for the viscoelastic characterization of
soft materials at the microscale. Micromachines, 9(1).
Edsberg, L. E., Cutway, R., Anain, S., and Natiella, J. R.
(2000). Microstructural and mechanical characteriza-
tion of human tissue at and adjacent to pressure ulcers.
Journal of Rehabilitation Research and Development,
37(4):463–471.
Flacco, F., De Luca, A., Sardellitti, I., and Tsagarakis, N. G.
(2011). Robust estimation of variable stiffness in flex-
ible joints. In in Proc. of 2011 IEEE/RSJ International
Conference on Intelligent Robots and Systems.
Fontanelli, G. A., Ficuciello, F., Villani, L., and Siciliano,
B. (2017). Modelling and identification of the da vinci
research kit robotic arms. In 2017 IEEE/RSJ Interna-
tional Conference on Intelligent Robots and Systems
(IROS), pages 1464–1469.
Gonz
´
alez-Cruz, R. D., Fonseca, V. C., and Darling, E. M.
(2012). Cellular mechanical properties reflect the dif-
ferentiation potential of adipose-derived mesenchy-
mal stem cells. Proceedings of the National Aca-
demy of Sciences of the United States of America,
109(24):E1523–E1529.
Guido, I., Jaeger, M., and Duschl, C. (2011). Dielectrop-
horetic stretching of cells allows for characterization
of their mechanical properties. European Biophysics
Journal, 40(3):281–288.
Kiss, M. Z., Varghese, T., and Hall, T. J. (2004). Viscoelas-
tic characterization of in vitro canine tissue. Physics
in Medicine and Biology, 49(18):4207–4218.
Lee, S. D. and Jung, S. (2016). A recursive least square ap-
proach to a disturbance observer design for balancing
control of a single-wheel robot system. 2016 IEEE In-
ternational Conference on Information and Automa-
tion (ICIA), pages 1878–1881.
Ljung, L. (1999). System Identification: Theory for the
User. Prentice Hall, 2nd edition.
Lundquist, C. and Sch
¨
on, T. B. (2009). Recursive identifi-
cation of cornering stiffness parameters for an enhan-
ced single track model. IFAC Proceedings Volumes,
42(10):1726 – 1731. 15th IFAC Symposium on Sy-
stem Identification.
Morrison III, B., Meaney, D. F., and McIntosh, T. K. (1998).
Mechanical characterization of an in vitro device de-
signed to quantitatively injure living brain tissue. An-
nals of Biomedical Engineering, 26(3):381–390.
Nava, A., Mazza, E., Furrer, M., Villiger, P., and Reinhart,
W. H. (2008). In vivo mechanical characterization of
human liver. Medical Image Analysis, 12(2):203–216.
Nava, A., Mazza, E., Kleinermann, F., Avis, N. J., and
McClure, J.and Bajka, M. (2004). Evaluation of
the mechanical properties of human liver and kidney
through aspiration experiments. Technology and He-
alth Care, 12(3):269–280.
Tavakoli, M., Aziminejad, A., Patel, R., and Moallem, M.
(2006). Multi-sensory force/deformation cues for stif-
fness characterization in soft-tissue palpation. Annual
Int. Conference of the IEEE Engineering in Medicine
and Biology Society. IEEE Engineering in Medicine
and Biology Society, pages 837–840.
Vahidi, A., Stefanopoulou, A., and Peng, H. (2005). Recur-
sive least squares with forgetting for online estimation
of vehicle mass and road grade: Theory and experi-
ments. Vehicle System Dynamics, 43(1):31–55.
Verotti, M., Crescenzi, R., Balucani, M., and Belfiore, N. P.
(2015). Mems-based conjugate surfaces flexure hinge.
Journal of Mechanical Design, 137(1):012301.
Verotti, M., Dochshanov, A., and Belfiore, N. P. (2017).
Compliance synthesis of csfh mems-based microgrip-
pers. Journal of Mechanical Design, 139(2):022301.
Wakatsuki, T., Kolodney, M. S., Zahalak, G. I., and Elson,
E. L. (2000). Cell mechanics studied by a reconsti-
tuted model tissue. Biophysical Journal, 79(5):2353–
2368.
Wilkening, A. and O., I. (2014). Estimation of mass para-
meters for cooperative human and soft-robots as basis
for assistive control of rehabilitation devices. In Pro-
ceedings of the RAAD 2014, 23rd International Con-
ference on Robotics in Alpe-Adria-Danube Region.
ICINCO 2018 - 15th International Conference on Informatics in Control, Automation and Robotics
510