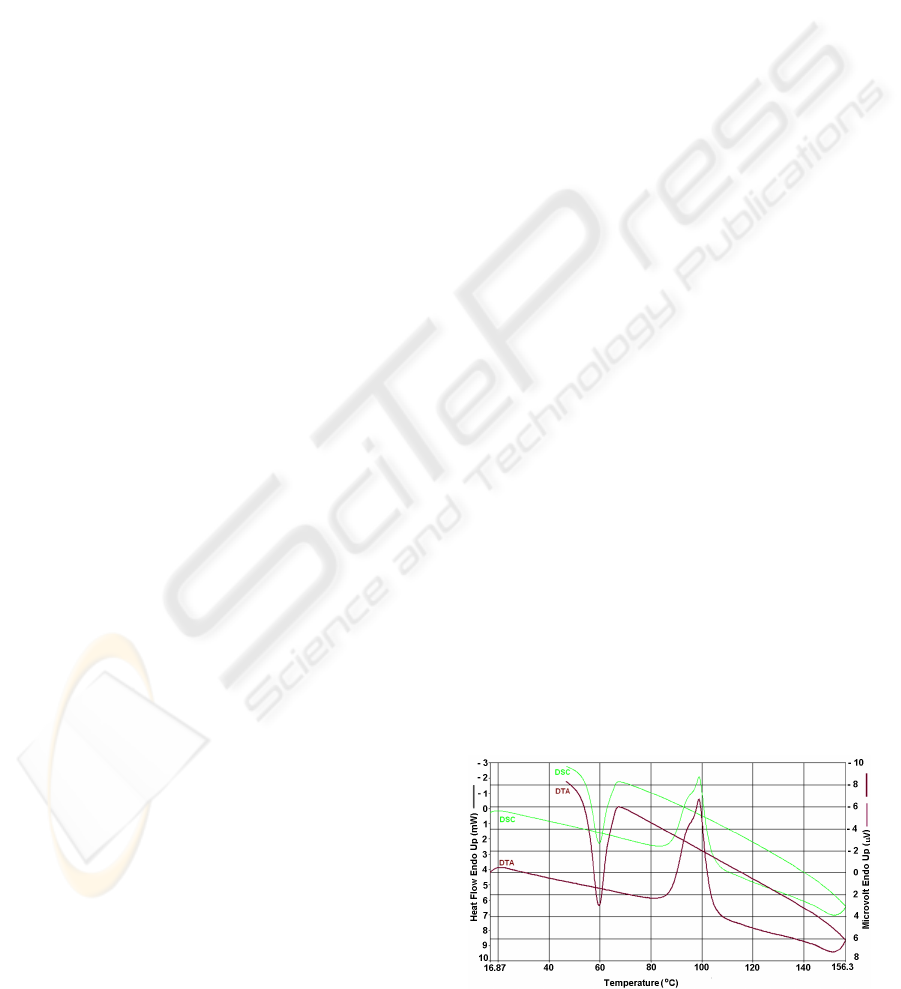
2006), (Waram, 1993), (Van Humbeeck, 2001). The
two applications presented in this paper are mainly
using the two-way shape memory effect representing
the ability of SMA's to recover a preset shape upon
heating above the transformation temperatures and to
return to a certain alternate shape upon cooling.
3 DESIGN STRATEGIES FOR
SMA ELEMENTS
The first step an engineer should take when
undertaking a design involving shape memory
material is to clearly define the design requirements.
This article includes the design strategies for the
SMA cantilever strip and for a SMA spring working
against a conventional steel spring (referred to in
this case as the “biasing” spring). In both design
models the friction effect is neglected and a linear
stress-strain behavior is assumed (Nasser, 2005).
3.1 Operating Modes of SMA’s
The most used operating modes of SMA's are: free
recovery, constrained recovery and work production.
The two Visual Basic applications presented in
this paper use a work production operating mode. In
this kind of operating mode a shape memory
element (SME), such as a strip or a helical springs,
works against a constant or varying force to perform
work. The element therefore generates force and
motion upon heating.
3.2 Transformation Temperatures
SMA’s exhibit a large temperature dependence on the
material shear modulus, which increases from low to
high temperature. Therefore, as the temperature is
increased the force exerted by a SME increases
dramatically (Dolce, 2001), (Nasser, 2005).
This section presents the transformation
temperatures obtained for the studied SMA elements
(strip and helical spring) using Thermal Analysis
Methods. Ni-Ti-Cu (Raychem proprietary alloy) is
the material used for the two SMA elements.
Thermogravimetric Analysis (TGA), Differential
Thermal Analysis (DTA) and Differential Scanning
Calorimetry (DSC) methods were used to determine
the required parameters. The measurements were
carried out on a Perkin Elmer Thermobalance in
dynamic air atmosphere, showing that the sample’s
mass does not undergo any changes at heating and
cooling. In consequence, the TGA curves are ignored.
SMA strip transformation temperature
The temperature control program used for SMA
strip measurements contains the following sequences:
heating from 30°C to 160°C at 5°C/min;
holding for 10min at 160°C;
cooling from 160°C to 20°C at 5 °C/min.
The DTA and DSC curves are presented in Figure
1. By analyzing this figure we can observe two phase
transitions. The first occurs during the heating while
the second one appears during the cooling process.
The details of these thermal effects are presented in
figures 2 and 3 (reported from the DSC curve).
Figure 2 shows that the determined transformation
temperatures at heating are A
s
=80°C and A
f
=111°C.
The enthalpy of the endothermal transition process is
ΔH
h
=36.8858J/g. The temperature corresponding to
maximum transformation speed is 98.79°C.
The transformation temperatures at cooling result
from Figure 3: M
s
=69°C and M
f
=48.25°C. The
enthalpy of the exothermal transition process is
ΔH
c
=-28.7792J/g and the temperature corresponding
to maximum transformation speed is 59.75°C.
SMA helical spring transformation temperature
The transformation temperatures of SMA helical
spring are obtained by similar measurements as in
the case of SMA strip, using the following
temperature-control sequences:
heating from 30°C to 100°C at 5°C/min;
holding for 10 min at 100°C;
cooling from 100°C to 20°C at 5 °C/min.
The form of DTA and DSC curves is similar to
the ones represented in Figure 1, for 6.849mg SMA
spring sample. The experimental transformation
temperatures at heating are A
s
=58.89°C and
A
f
=67.93°C. The enthalpy of the endothermal
transition process is ΔH
h
=9.2J/g and the temperature
corresponding to maximum transformation speed is
60.42°C. The transformation temperatures at cooling
are M
s
=45°C and M
f
=33°C, the enthalpy of the
exothermal transition process is ΔH
c
= -5.03J/g and
the temperature corresponding to maximum
transformation speed is 39.07°C.
Figure 1: DTA and DSC curves for 18.275mg SMA strip.
ICINCO 2008 - International Conference on Informatics in Control, Automation and Robotics
208