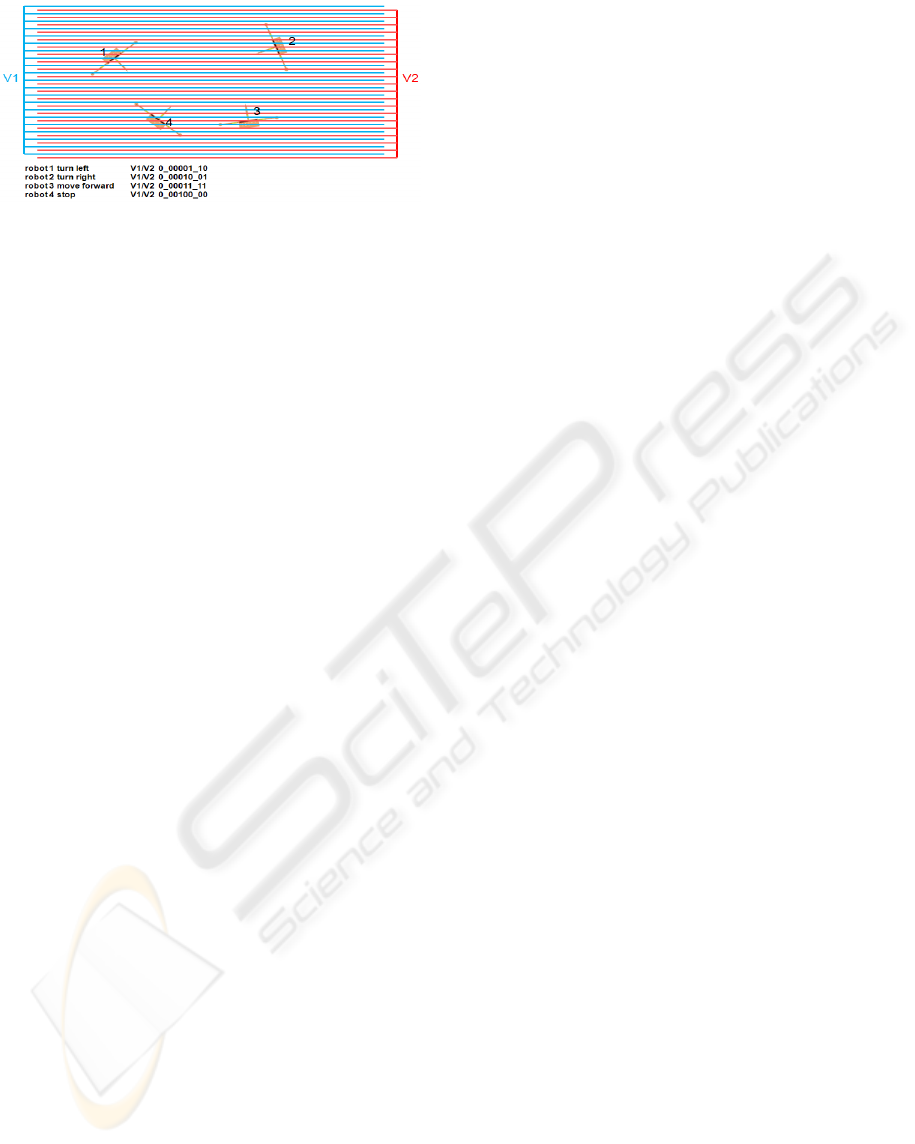
Figure 10: V1 / V2 are used as channels to apply binary
encoded controls to each micro-robot.
Each micro-robot is assigned a unique 5-bit number
and as part of the on-board logic there is an 8-bit
UART which recovers the serial communication and
programs each micro-robot for the operation it needs
to perform. When a particular micro-robot receives a
5-bit number that does not match its assigned robot
number, the robot in question ignores the three
command bits. If, on the other hand, the 5-bit
numbers match, the robot in question will latch the
three command bits into MTJ flip-flops so that at the
next major cycle the robot in question will perform
the command specified. The UART is clocked every
minor cycle, which operates at a much higher
frequency than the major cycle. Since transmitting
each 8-bit code requires a start and stop bit, the
bandwidth required on the global communications
channel for a swarm of 32 robots is at least
10*32=320 times the major cycle, and the UART
operates at some multiple of this. For example, if the
major cycle is 1 KHz and the UART requires 8
minor cycles per bit received, the minor cycle needs
to be about 2.5 MHz because the channel needs to
transmit at least 320,000 bits/second.
6 CONCLUSIONS
We have proposed a novel approach of applying
MEMS SDA micro-robots to assist in
dermatological procedures on the assumption power
may be applied via a bandage-like substrate. We
discussed features needed on a MEMS micro-robot
to achieve this. It needs improvement from Donald
et al. (Donald et al., 2006) to provide uniform
control for turning MEMS SDAs using a much
lower voltage signal that used by Donald et al. By
adding an additional stylus arm the robot can now
turn both left and right as well as use both arms to
stop. A third stylus arm provides a micro-scalpel.
Fabricating a transistor connection between each
stylus and the parallel-plate body allows the micro-
robot to control the pull-in voltage. Using this
control capability, we also presented a new approach
to using the power grid to communicate to each
micro-robot using a binary-encoded signal which
operates at much lower voltages than previous multi-
robot SDA systems.
REFERENCES
Bruce R. Donald, Christopher G. Levey, and Igor
Paprotny, 2008.
Planar Microassembly by Parallel Actuation of MEMS
Microrobots. In IEEE – Journal of Microelectro-
mechanical Systems, vol. 17, no. 4.
Bruce R. Donald, Christopher G. Levey, Craig D.
McGray, Igor
Paprotny, and Daniela Rus, 2006. An Untethered,
Electrostatic, Globally Controllable MEMS Micro-
Robot. In IEEE – Journal of Microelectro-mechanical
Systems, vol. 15, no. 1.
Bruce R. Donald, Christopher G. Levey, Craig D.
McGray, and
Daniela Rus, 2003. Power Delivery and Locomotion of
Untethered Micro-actuators. In IEEE – Journal of
Microelectromechanical Systems, vol. 12, no. 6.
W. Zhao, E. Belhaire, C. Chappert, 2007. Spin-MTJ based
Non-Volatile Flip-Flop. In International Conference on
Nanotechnology.
Loreto Mateu and Francesc Moll, 2007. System-level
Simulation
of a Self-powered Sensor with Piezoelectric Energy
Harvesting. In International Conference on Sensor
Technologies and Applications.
Shimul Chandra Saha, Ulrik Hanke, Geir Uri Jensen, and
Trond Saether, 2006. Modeling of Spring Constant and
Pull-down Voltage of Non uniform RF MEMS
Cantilever. In Behavioral Modeling and Simulation
Workshop, Proceedings of the 2006 IEEE
International, pp. 56-60.
Leow Cheah Wei, Abu Baker Mohammad and
Norazan Mohd. Kassim, 2002. Analytical Modeling For
Determination Of Pull-In Voltage For An Electrostatic
Actuated MEMS Cantilever Beam. In Proceedings of
ICSE2002.
Smith, Susan Rae, Foster, Kenneth R., Wolf, Gerald L.,
1986.
Dielectric Properties of VX-2 Carcinoma Versus Normal
Liver Tissue. In IEEE Transactions on Biomedical
Engineering, BME-33, 5, 522-524.
C. Hensen, 1998. Data transmission applications via low
voltage
power lines using OFDM technique. In 1998 IEEE 5th
International Symposium on Spread Spectrum
Techniques and Applications, 1, 210 – 214.
Jung H. Cho and Mark G. Arnold, 2009. Powering
Embedded
CMOS Logic on MEMS-based Micro-Robots. In IEEE
International Behavioral Modeling and Simulation
Conference, 73-77.
LOW-VOLTAGE SCRATCH-DRIVE MICRO-SCALPELS CONTROLLED BY A BINARY-ENCODED SIGNAL
223