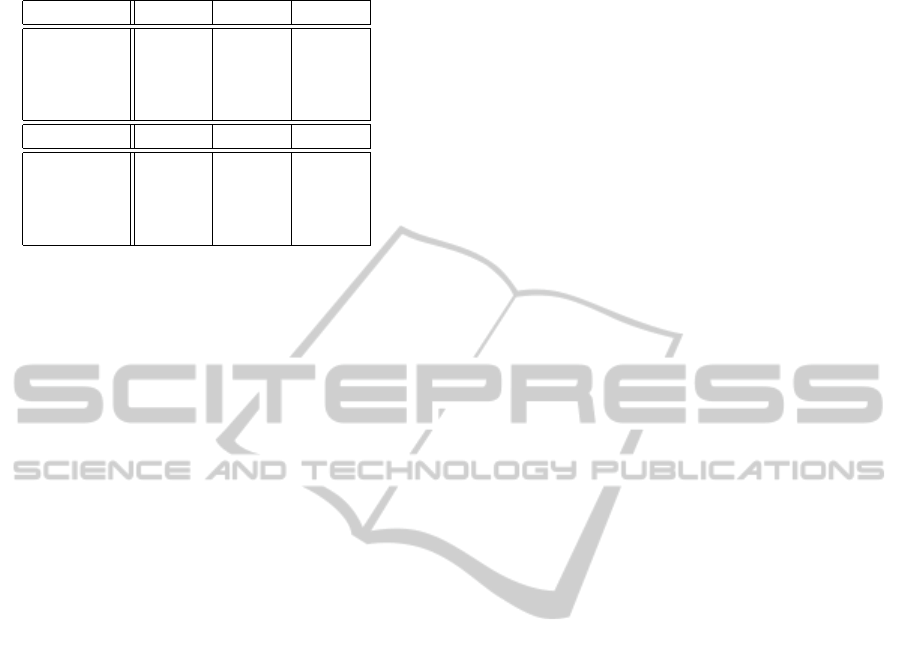
Table 2: Model criteria error for the different tests.
Canal axis VAF
1
VAF
2
VAF
3
x = L 80.36 91.14 91.97
x = 3/4L 91.71 99.61 99.29
x = 1/2L 87.43 99.58 98.50
x = 1/4L 93.40 99.09 98.37
Canal axis MAE
1
MAE
2
MAE
3
x = L 0.0041 0.0092 0.0121
x = 3/4L 0.0066 0.0061 0.0097
x = 1/2L 0.0049 0.0019 0.0064
x = 1/4L 0.0053 0.0040 0.0074
6 CONCLUSIONS
A finite dimension linear model for canal pools has
been presented and validated with experimental data.
The linearized partial differential equations describ-
ing the system are solved through matrices multipli-
cations which requires low computational effort. This
enables the model to be used for constructing open
water network systems. The possibility to use the dis-
charge, water depth or linearized hydraulic structures
as boundary conditions, augments the model applica-
bility.
The proposed model also allows for full canal
monitoring. This is an important feature that opens
the scope of application to fault detection, isolation,
and fault tolerant control algorithms.
ACKNOWLEDGEMENTS
This work was co-sponsored by project AQUANET -
Decentralized and Reconfigurable Control for Water
delivery Multipurpose Canal Systems (PTDC/EEA-
CRO/102102/2008), FCT, Portugal, through IDMEC
by the Associated Laboratory in Energy, Transports,
Aeronautics and Space.
REFERENCES
Akan, A. O. (2006). Open Channel Hydraulics. Elsevier.
Almeida, M., ao Figueiredo, J., and Rijo, M. (2002). Scada
configuration and control modes implementation on
an experimental water supply canal. In 10th Mediter-
ranean Conference on Control Automation, Lisbon,
Portugal.
Bedjaoui, N., Weyer, E., and Bastin, G. (2009). Methods
for the localization of a leak in open water channels.
Networks and Heterogeneous Media, 4(2):180–210.
Blanke, M., Kinnaert, M., Lunze, J., and Staroswiecki,
M. (2006). Diagnosis and Fault-Tolerant Control.
Springer-Verlag.
Duarte, J., Rato, L., Shirley, P., and Rijo, M. (2011). Multi-
platform controller interface for scada application. In
IFAC World Congress (Accepted in), Milan, Italy.
Isermann, R. (2006). Fault-Diagnosis Systems. Springer-
Verlag.
Litrico, X. and Fromion, V. (2002). Infinite dimensional
modelling of open-channel hydraulic systems for con-
trol purposes. In 41th IEEE Conference on Decision
and Control, pages 1681–1686, Las Vegas, Nevada.
Litrico, X. and Fromion, V. (2004). Simplified modeling
of irrigation canals for controller design. Journal of
Irrigation and Drainage Engineering, 130:373–383.
Litrico, X. and Fromion, V. (2009). Modeling and Control
of Hysrosystmes. Springer-Verlag.
Martinez, C. A. O. (2007). Model Predictive Control of
Complex Systems including Fault Toelrance Capabil-
ities: Application to Sewer Networks. PhD thesis,
Technical University of Catalonia.
Nabais, J. and Botto, M. A. (2010). Qualitative compar-
ison between two open water canal models. In 9th
Portuguese Conference on Automatic Control, pages
501–506, Coimbra, Portugal.
Negenborn, R., van Overloop, P.-J., Keviczky, T., and
de Schutter, B. (2009). Distributed model predictive
control of irrigation canals. Networks and Heteroge-
neous Media, 4(2):359–380.
Schuurmans, J., Bosgra, O., and Brouwer, R. (1995). Open-
channel flow model approximation for controller de-
sign. Applied Mathematical Modelling.
Schuurmans, J., Clemmens, J., S.Dijkstra, Hof, A., and
Brouwer, R. (1999a). Modeling of irrigation and
drainage canals for controller design. Journal of Ir-
rigation and Drainage Engineering, 125(6):338–344.
Schuurmans, J., Hof, A., S.Dijkstra, Bosgra, O., and
Brouwer, R. (1999b). Simple water level controller
for irrigation and drainage canals. Journal of Irriga-
tion and Drainage Engineering, 125(4):189–195.
Silva, P., Botto, M. A., and ao Figueiredo, J. (2007). Model
predictive control of an experimental canal. In Eu-
ropean Control Conference, pages 2977–2984, Kos,
Greece.
Szymkiewicz, R. (2010). Numerical Modeling in Open
Channel. Springer-Verlag.
van Overloop, P. (2006). Model Predictive Control on Open
Water Systems. IOS Press.
LINEAR MODEL FOR CANAL POOLS
313