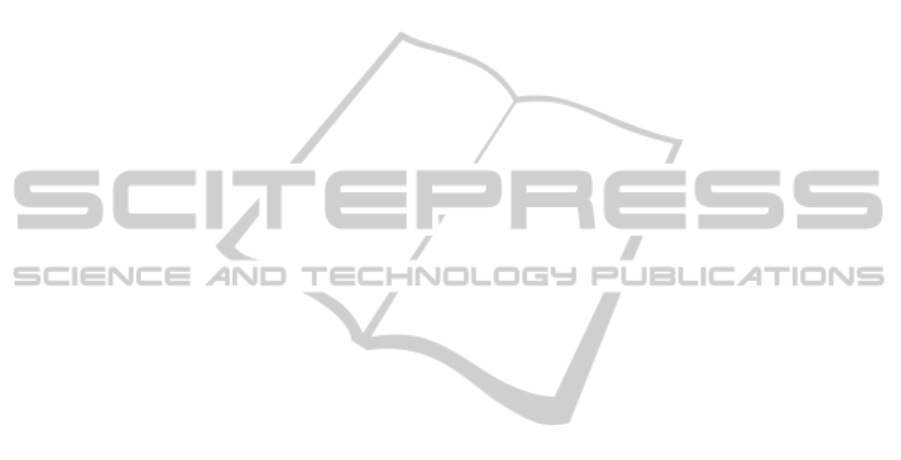
model was created and simulated with the program
system ANSYS.
A comparison study of the mechatronic handling
device prototypes was performed using obtained
experimental results. An experimental set-up was
used specially created for investigation of such
micro robots.
The mathematical and simulation models were
verified, as well as the system of its behaviour
(force, displacement and stiffness). It has been
proven that the prototype showed very similar data
in the experimental tests to the theoretical data.
ACKNOWLEDGEMENTS
The authors gratefully acknowledge the partially
support through the projects:
MeCHa-PiCS project funded by the DFG under
the contract KA-2 “Mechatronic handling devices
based on piezo-ceramic structures for micro- and
nano-applications” and
SpeCy-MiNT project funded by Bulgarian
Science Fund under the Contract Nr. DO
0171/16.12.2008 “Specialized Mechatronic Systems
for Micro and NanoTechnology”.
REFERENCES
Kortschack, A, Shirinov A., Trüper T., Fatikow S., 2005.
“Development of mobile versatile nanohandling
microrobots: design, driving principles, haptic
control”. In Journal Robotica, vol. 23, pp.419 – 434.
Albut, A., Zhou, Q. et al., 2003. “Development of Flexible
Force-Controlled Piezo-Bimorph Micro-gripping
System”. In Proceedings of 2nd VDE World
Microtechnologies Congress, MICRO.tec 2003,
Munich, Germany, pp:507-512, October 13-15.
Klocke V., 1998. “Nanotechnik, Motionfrom the
Nanoscale World”. In CD-ROM Version 1.5.
Patentschrift Hoerbiger Fluidtechnik GmbH, Piezo-Ventil,
AT 396392 B, 25.8 (1993).
Lubitz, K. Schuh, C. et al., 2000. „Properties and
Reliability of large PZT multilayer actuators”. In
ACTUATOR 2000, 7th International Conference on
New Actuators, Bremen, Germany, pp: 58-61.
Kasper, R., Al-Wahab, M., 2004. “Mechanically
Structured Piezoelectric Actuators”. In ACTUATOR
2004, 9
th
International Conference on New Actuators,
Bremen, Germany, pp: 68-71.
Kasper R., Al-Wahab M., Kostadinov, K., Chakarov D.,
W. Heinemann, 2004. “Mechatronic handling device
based on piezo ceramic structures for micro and nano
applications”. In 10
th
International Conference on New
Actuators, Bremen, Germany, pp: 154-158.
Chakarov D. et al., 2006. “Kinematics model of
nonholonomic wheeled mobile robots for mobile
manipulation tasks”. In The Proceedings of the
International Conference on bionics and prosthetics,
biomechanics and mechanics, mechatronics and
robotics, Bulgaria-Varna.
Bar-Itzhack, Itzhack Y., 2000. “New method for
extracting the quaternion from a rotation matrix”. In
AIAA Journal of Guidance, Control and Dynamics 23
(6):1085–1087(Engineering Note) doi:10.2514/2.4654
Kostadinov K., Kasper R., Tiankov T., Al-Wahab M.,
Chakarov D., Gotseva D., 2006. “Unified Approach
For Functional Task Formulation in Domain of
Micro/Nano Handling Operations”. In W. Menz and
St. Dimov (Eds.), 4M2005 Second Int. conference on
Multi- Material Micro Manufacture (Grenoble,
20.09.-22.09.2006), Elsevier, pp. 255-258.
Kostadinov K. Gr., Ionescu F., Hradynarski R., Tiankov
T., 2005. „Robot based assembly and processing
micro/nano operations”. In W. Menz and St. Dimov
(Eds.), 4M2005 First International conference on
Multi- Material Micro Manufacture (Karlsruhe,
29.06.-01.07.2005), Elsevier, pp.295-298.
Shulev A., T. Tiankov, M. Al-Wahab, I. Roussev, R.
Kasper, K. Kostadinov, 2010. “Optical approach for
positioning control of handling devices for micro-
manipulations”. In Ed.: E. Djukendjiev -
“Proceedings of the 7
th
Int. Conference on bionics and
prosthetics, biomechanics and mechanics,
mechatronics and robotics”, (ICBMM), ISBN 978-
9934-10-027-7, pp. 62-65.
MICRO/NANO-MANIPULATORS WITH STRUCTURED PIEZO CERAMIC ACTUATORS
247