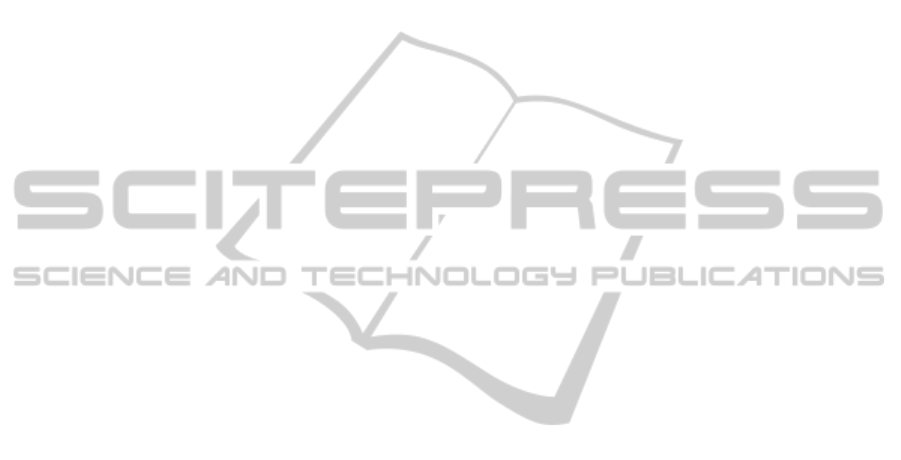
possible to control the mechanical manipulator, the
heaters and the flux of liquid nitrogen Also the sun
simulator beam will be controlled with a diaphragm
and the scroll pump will be turned on and off with a
switch on the power line. In this way both the
students and the researchers will have the possibility
of carrying out experiments of a certain complexity
also remotely.
ACKNOWLEDGEMENTS
The authors wish to thank the Italian Space Agency
for supporting the LARES mission, and in particular
the thermo-vacuum facility, under contracts
I/043/08/0, I/043/08/1, I/034/12/0 and I/034/12/1.
REFERENCES
Aliane, N., 2007. LABNET: A Remote Control
Engineering Laboratory. International Journal of
Online Engineering. Vol. 3, n. 2.
Bosco, A., Cantone, C., Dell'Agnello, S., Delle Monache,
G. O., Franceschi, M. A. Garattini, M., Napolitano, T.,
Ciufolini, I., Agneni, A., Graziani, F., Ialongo, P.,
Lucantoni, A., Paolozzi, A., Peroni, I. Sindoni, G.,
Bellettini, G., Tauraso, R., Pavlis, E. C., Currie, D.G.,
Rubincam, D. P., Arnold, D. A., Matzner, R.,
Slabinski V. J., 2007. Probing gravity in NEO with
high-accuracy laser-ranged test masses. International
Journal of Modern Physics D. Vol. 16, pp. 2271-2285.
Cappelletti, C., Martinotti, G., Graziani, F., 2011.
UniCubeSat: a test for the gravity gradient solar array
boom. In Proceedings of 62nd International
Astronautical Congress, IAC 2011. Cape Town, South
Africa, 3-7 October 2011.
Casini, M., Prattichizzo, D., Vicino, A., 2001. The
Automatic Control Telelab: a remote control
engineering laboratory. In Proceedings of the 40th
IEEE Conference on Decision and Control. Orlando,
04-07 Dec 2001. Vol.4, pp. 3242 – 3247.
Ciufolini, I., 1996. On a new method to measure the
gravitomagnetic field using two orbiting satellites.
Nuovo Cimento A. Vol. 109, n. 12, pp. 1709–1720.
Ciufolini, I., Currie, D.G., Paolozzi, A., 2003. The LARES
mission for testing the dynamics of General Relativity.
In: Proceedings of IEEE Aerospace Conference, Big
Sky, Montana, USA, 5-12 March 2003. Vol. 2, pp.
693-703.
Ciufolini, I. and Pavlis, E. C., 2004. A confirmation of the
general relativistic prediction of the Lense-Thirring
effect. Nature. Vol. 431, pp. 958–960.
Ciufolini, I., 2007. Dragging of inertial frames. Nature.
Vol. 449, pp. 41-47.
Ciufolini, I., Paolozzi, A., Pavlis, E.C., Ries, J., Koenig,
R., Matzner, R., Sindoni, G., and Neumayer, H., 2011.
Testing gravitational physics with satellite laser
ranging. The European Physical Journal Plus. Vol.
126, id 72.
Ciufolini, I., Paolozzi, A., Paris, C., 2012. Overview of the
LARES Mission: orbit, error analysis and
technological aspects. Journal of Physics, Conference
Series. Vol. 354, pp. 1-9.
Ciufolini, I., Paolozzi, A., König, R., Pavlis, E. C., Ries,
J., Matzner, R., Gurzadyan, V., Penrose, R., Sindoni,
G., Paris, C., 2013a. fundamental physics and general
relativity with the LARES and LAGEOS satellites.
Nuclear Physics B - Proceedings Supplements. Vols.
243-244, pp. 180-193.
Ciufolini, I., Moreno Monge, B., Paolozzi, A., Koenig, R.,
Sindoni, G., Michalak, G., Pavlis, E. C., 2013b. Monte
Carlo simulations of the LARES space experiment to
test General Relativity and fundamental physics.
Classical and quantum gravity. Vol. 30, n. 23, pp.1-
11.
Graziani, F., Pulcrano, G., Santoni, F., Perelli, M.,
Battagliere, M. L., 2009. EduSAT: An Italian Space
Agency outreach program. In Proceedings of 60th
International Astronautical Congress 2009, IAC 2009.
Daejeon, South Korea, 12-16 October 2009.
Herrera, O. A., Alves, G. R., Fuller, D., Aldunate R. G.,
2006. Remote lab experiments: opening possibilities
for distance learning in engineering fields. In
Education for the 21st Century- Impact of ICT and
Digital Resources. IFIP International Federation for
Information Processing. Vol. 210, pp. 321-325.
Jaggers, C. H., Meshishnek, M. J., Coggi, J. M., 1993.
Thermal control paints on LDEF: Results of M0003
sub-experiment 18. In NASA. Langley Research
Centre, LDEF: 69 Months in Space. Part 3: Second
Post-Retrieval Symposium, pp. 1075-1092 (SEE N93-
28254 10-99).
Marco, J., Bhojaraj, H., & Hulyal, R., 2003. Evaluation of
thermal control materials degradation in simulated
space environment. In Proceedings of the 9th
International Symposium on Materials in a Space
Environment. 16-20 June 2003, Noordwijk, The
Netherlands. ESA SP-540, Noordwijk, Netherlands:
ESA Publications Division, ISBN 92-9092-850-6,
2003, pp. 359-366.
May, D., Terkowsky, C., Haertel, T., Pleul, C., 2013.
Bringing Remote Labs and Mobile Learning together.
International Journal of Interactive Mobile
Technologies. Vol. 7, n. 3.
NASA, 1995. Analysis of Materials Flown on the Long
Duration Facility: Summary of Results of the
Materials Special Investigation Group. Technical
report. Boeing Defense and Space Group, NASA CR,
May 1995.
Paolozzi, A Ciufolini, I., Vendittozzi, C., F. Passeggio, L.
Caputo, G. Caputo, 2009. Technological challenges
for manufacturing LARES satellite. In Proceedings of
the 60th International Astronautical Congress, IAC
2009. 12-16 October 2009.
Paolozzi, A., Ciufolini, I. and Vendittozzi, C., 2011.
Engineering and scientific aspects of LARES satellite.
LARES-lab:AThermo-vacuumFacilityforResearchandE-learning-TestsofLARESSatelliteComponentsandSmall
Payloadsfore-Learning
473