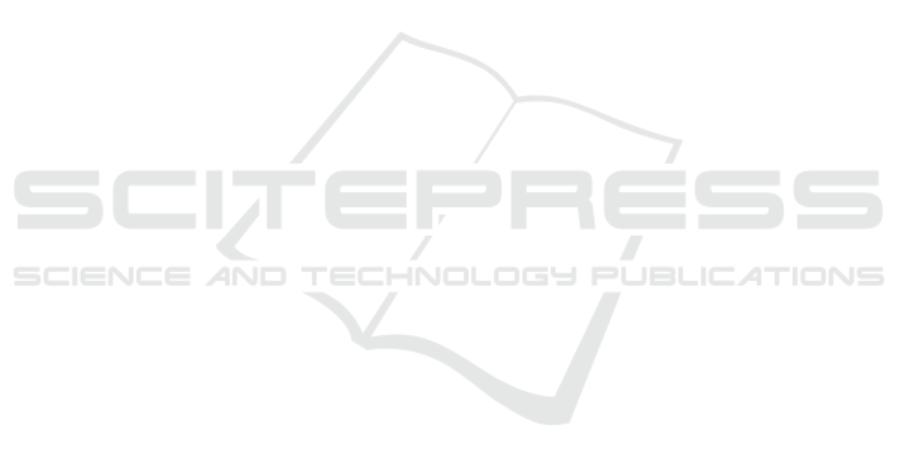
surprises and assumptions, v) summarize your under-
standing at the end of each session to determine what
to focus on next, vi) build an understanding of user
work and of the environment being designed, vii) un-
derstand, design and build a first cut at a user environ-
ment, and viii) iterate the prototype with real users
doing real work. These guidelines are still valid to-
day, mainly for Contextual Inquiry (CI), i.e., the CD
method recommended for early project phases.
In 1993, (Holtzblatt and Jones, 1993) described
CI in further detail, affirming the challenges addres-
sed by Wixon et al., e.g., that “people speak about
their work in abstractions” and pointing out the “diffe-
rence between summary information and ongoing ex-
perience”. According to Holtzblatt and Jones, when
asked about a computer system, people provide a
summary or their general opinion which is often a
strongly abstracted statement derived from everyday
experience. This might lead also to people not repor-
ting positive aspects because they are frequently not
aware of what they like about a system as it works
well and does not call attention to itself. We can af-
firm these problems as we experienced similar beha-
viours when talking to stakeholders. (Beyer and Holt-
zblatt, 1997) published the first book describing CD
in-depth and involving an extensive guide to the pre-
paration and implementation of a CD process. They
explain all CD phases and provide practical exam-
ples of roles, artifacts, analysis methods and results.
(Holtzblatt et al., 2005) introduced Rapid Contex-
tual Design (RCD) which was our primary guide, ac-
counting for the immense effort involved with CD.
RCD provides a more dense guide for practitioners
and focuses on the core CD techniques that most ea-
sily drive customer data into the corporate design pro-
cess. Starting in 2013, CD was overhauled in or-
der to account for changes in technology and its in-
fluence on humans’ lives, e.g., through “always-on,
always-connected, and always-carried devices” (Holt-
zblatt and Beyer, 2017).
2.2 Application Use Cases
(Gellatly et al., 2010) describe the first of several CD
projects undertaken by the General Motors UX de-
sign team. The project called “Journey” focused on
gaining a deeper understanding of how drivers inte-
ract with today’s entertainment, communication, na-
vigation, and information systems in their vehicles. It
followed the CD process as described by (Beyer and
Holtzblatt, 1997; Holtzblatt et al., 2005) and speci-
fically aimed at i) documenting user intents for en-
tertainment, communication, navigation and informa-
tion system usage, ii) studying the balance between
in-car systems and carried-in devices usage, iii) de-
termining how users’ outside lives should be suppor-
ted in-car, iv) capturing how in-car tasks interact with
the driving task, v) determining effects of individual
differences in tolerance to sensory overload, mental
models of navigation and age, and vi) uncovering the
values that customers have around brand, design and
aesthetics. The process comprised CI, interpretation
sessions, affinity diagram, work models and visioning
and is thus similar to ours regarding methodology.
However, while Gellatly et al. focus on the description
of their findings, our paper emphasizes more strongly
the experiences with CD and related lessons learned.
(Coble et al., 1995) describe a CI process con-
ducted to gather physicians’ requirements for a cli-
nical information system. Their CI sessions compri-
sed orientation, interview and wrap-up. Following the
CI session, data were analyzed and used to derive a
sequence, a flow and a context model, and detailed
observations and a user profile. The sequence mo-
del documented the sequences of activities the phy-
sician performed. The flow model documented the
information and items flowing between physician and
other people or places. The context model documen-
ted external influences which affected how the physi-
cian cared for patients. The observations contained
the details of what the physician did and were the
primary source for requirements. The process fol-
lowed in our research projects differed in that our
main data consolidation and analysis tool was the
affinity diagram as suggested by (Holtzblatt et al.,
2005). Coble et al. describe their CI efforts as ex-
tensive and time-consuming which complies with our
experiences. E.g., they report 80 physician hours, 130
staff hours in direct participation, 90 staff hours in
post-session documentation and additional 1300 staff
hours in data analysis sessions over three months.
(Fouskas et al., 2002) applied CI for gathering
users’ requirements in the context of mobile exhibi-
tion services. They describe their process with a fo-
cus on the method itself, aiming at providing a guide
for further investigations and experiments in using the
CD methodology (with emphasis on CI). Their paper
is thus of similar nature compared to ours, however,
we believe that i) the application domain does actu-
ally influence “best practices” for the conduction of
CD/CI and ii) the characteristics of interactive soluti-
ons have changed since 2002, which is also affirmed
by (Holtzblatt and Beyer, 2014). Other major diffe-
rences can be found in the project phase discussed;
Fouskas et al. do not describe the analysis of the data
gathered via CI, which is one of the main contributi-
ons of our paper. Further, they suggest the derivation
of a unified requirements specification report from CI
Contextual Design in Industrial Settings: Experiences and Recommendations
431