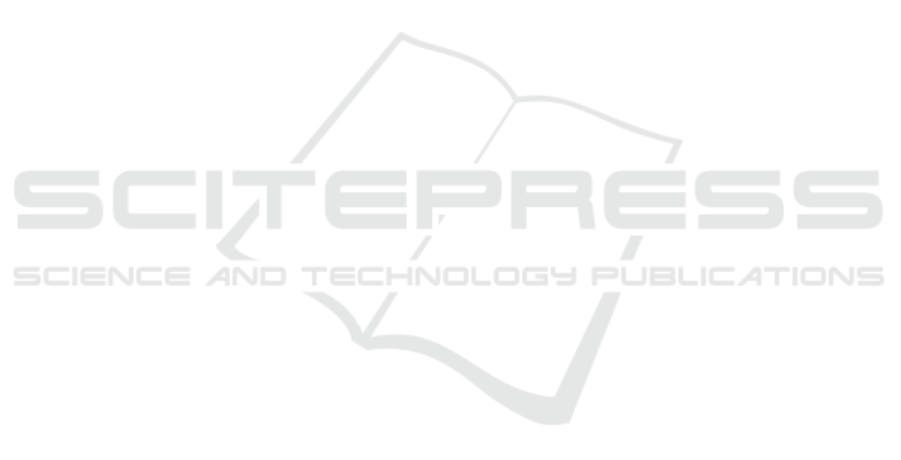
Balntas, V., Li, S., and Prisacariu, V. (2018). Relocnet:
Continuous metric learning relocalisation using neu-
ral nets. In Proceedings of the European Conference
on Computer Vision (ECCV), pages 751–767.
Bello, J. P., Silva, C., Nov, O., Dubois, R. L., Arora, A.,
Salamon, J., Mydlarz, C., and Doraiswamy, H. (2019).
Sonyc: A system for monitoring, analyzing, and mit-
igating urban noise pollution. Communications of the
ACM, 62(2):68–77.
Borrmann, D., Elseberg, J., and N
¨
uchter, A. (2013). Ther-
mal 3d mapping of building fac¸ades. In Intelligent
autonomous systems 12, pages 173–182. Springer.
Cejka, S., Frischenschlager, A., Faschang, M., Stefan,
M., and Diwold, K. (2018). Operation of modu-
lar smart grid applications interacting through a dis-
tributed middleware. Open Journal of Big Data
(OJBD), 4(1):14–29.
Czimmermann, T., Ciuti, G., Milazzo, M., Chiurazzi, M.,
Roccella, S., Oddo, C. M., and Dario, P. (2020).
Visual-based defect detection and classification ap-
proaches for industrial applications—a survey. Sen-
sors, 20(5):1459.
Diwold, K., Mayer, S., Einfalt, A., Parreira, J. X.,
Hodges, J., Anicic, D., and Mosshammer, R. (2018).
Grid watch dog: A stream reasoning approach for
lightweight scada functionality in low-voltage grids.
In Proceedings of the 8th International Conference on
the Internet of Things, pages 1–8.
Graf, F. and Gruber, M. (2018). Rapid incident detection in
tunnels through acoustic monitoring–operating expe-
riences in austrian road tunnels.
Hedman, K. W., Oren, S. S., and O’Neill, R. P. (2011). A re-
view of transmission switching and network topology
optimization. In 2011 IEEE power and energy society
general meeting, pages 1–7. IEEE.
Heittola, T., C¸ akır, E., and Virtanen, T. (2018). The machine
learning approach for analysis of sound scenes and
events. In Computational Analysis of Sound Scenes
and Events, pages 13–40. Springer.
Janda, K., M
´
alek, J., and Re
ˇ
cka, L. (2017). Influence of
renewable energy sources on transmission networks in
central europe. Energy Policy, 108:524–537.
K
¨
ahler, O., Prisacariu, V. A., and Murray, D. W. (2016).
Real-time large-scale dense 3d reconstruction with
loop closure. In European Conference on Computer
Vision, pages 500–516. Springer.
Klutke, G.-A., Kiessler, P. C., and Wortman, M. A. (2003).
A critical look at the bathtub curve. IEEE Transac-
tions on reliability, 52(1):125–129.
Koester, L. W., Taheri, H., Bigelow, T. A., Bond, L. J., and
Faierson, E. J. (2018). In-situ acoustic signature mon-
itoring in additive manufacturing processes. In AIP
Conference Proceedings, volume 1949, page 020006.
AIP Publishing LLC.
Lee, E., Hong, J., and Kim, D. (2018). Automatic instru-
ment status monitoring using deep neural networks.
ECCV Demo Sessions.
Morabito, R. (2017). Virtualization on internet of things
edge devices with container technologies: A perfor-
mance evaluation. IEEE Access, 5:8835–8850.
Palazzolo, E. and Stachniss, C. (2017). Change detection
in 3d models based on camera images. In 9th Work-
shop on Planning, Perception and Navigation for In-
telligent Vehicles at the IEEE/RSJ Int. Conf. on Intel-
ligent Robots and Systems (IROS).
Park, D. H., Darrell, T., and Rohrbach, A. (2019). Robust
change captioning. In Proceedings of the IEEE/CVF
International Conference on Computer Vision, pages
4624–4633.
Pliatsios, D., Sarigiannidis, P., Lagkas, T., and Sarigianni-
dis, A. G. (2020). A survey on scada systems: secure
protocols, incidents, threats and tactics. IEEE Com-
munications Surveys & Tutorials, 22(3):1942–1976.
Pudlo, G., Tenbohlen, S., Linders, M., and Krost, G. (2002).
Integration of power transformer monitoring and over-
load calculation into the power system control surface.
In IEEE/PES Transmission and Distribution Confer-
ence and Exhibition, volume 1, pages 470–474. IEEE.
Raith, J., Bonini, C., and Scala, M. (2020). Simulation of
long-term transformer operation with a dynamic ther-
mal, moisture and aging model. In 5th International
Colloquium on Transformer Research and Asset Man-
agement, pages 211–226. Springer.
Sakurada, K., Shibuya, M., and Wang, W. (2020). Weakly
supervised silhouette-based semantic scene change
detection. In 2020 IEEE International conference on
robotics and automation (ICRA), pages 6861–6867.
IEEE.
Sattler, T., Zhou, Q., Pollefeys, M., and Leal-Taixe, L.
(2019). Understanding the limitations of cnn-based
absolute camera pose regression. In Proceedings of
the IEEE/CVF conference on computer vision and
pattern recognition, pages 3302–3312.
Seitlinger, W. (2000). A thermo-hydraulic transformer
model. Proceedings of the Conference of Electrical
Power Supply Industry.
Sels, S., Verspeek, S., Ribbens, B., Bogaerts, B., Vanlan-
duit, S., Penne, R., and Steenackers, G. (2019). A cad
matching method for 3d thermography of complex ob-
jects. Infrared Physics & Technology, 99:152–157.
Shafiullah, G. (2016). Impacts of renewable energy integra-
tion into the high voltage (hv) networks. In 2016 4th
International Conference on the Development in the in
Renewable Energy Technology (ICDRET), pages 1–7.
IEEE.
Shi, K., Chen, Y., Yu, B., Xu, T., Yang, C., Li, L., Huang,
C., Chen, Z., Liu, R., and Wu, J. (2016). Detecting
spatiotemporal dynamics of global electric power con-
sumption using dmsp-ols nighttime stable light data.
Applied energy, 184:450–463.
Siebald, H., Hensel, O., Beneke, F., Merbach, L., Walther,
C., Kirchner, S. M., and Huster, J. (2017). Real-
time acoustic monitoring of cutting blade sharpness
in agricultural machinery. IEEE/ASME Transactions
on Mechatronics, 22(6):2411–2419.
Sinsel, S. R., Riemke, R. L., and Hoffmann, V. H. (2020).
Challenges and solution technologies for the integra-
tion of variable renewable energy sources—a review.
renewable energy, 145:2271–2285.
X-AMINOR: A Mobile Multi-Sensor Platform for Lifecycle-Monitoring of Transformers
127