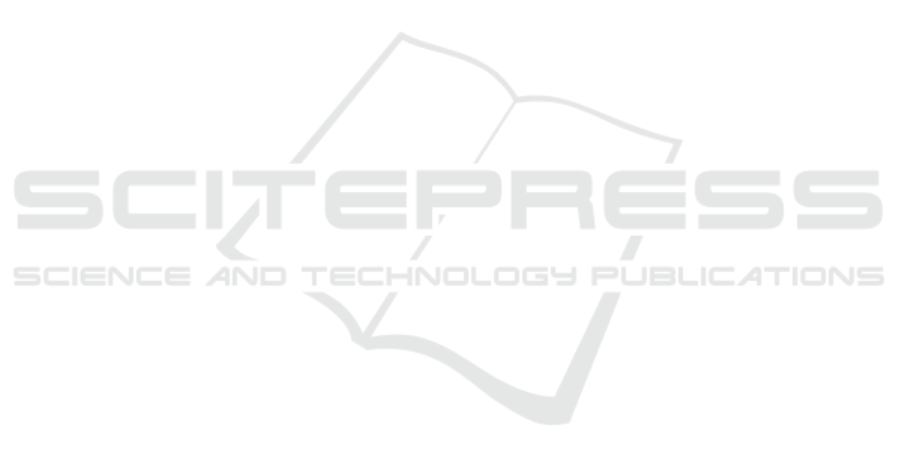
REFERENCES
Artemenko, A. (2021). Keynote: Advances and challenges
of industrial iot. In 2021 IEEE International Con-
ference on Pervasive Computing and Communications
Workshops and other Affiliated Events (PerCom Work-
shops), page 526–526.
Autor, D. H. (2015). Why are there still so many jobs? the
history and future of workplace automation. Journal
of Economic Perspectives, 29(3):3–30.
Brown, G. et al. (2018). Ultra-reliable low-latency 5G
for industrial automation. Technol. Rep. Qualcomm,
2:52065394.
Cheng, J., Chen, W., Tao, F., and Lin, C.-L. (2018). In-
dustrial iot in 5g environment towards smart manufac-
turing. Journal of Industrial Information Integration,
10:10–19.
Choi, H., Song, J., and Yi, K. (2018). Brightics-iot: To-
wards effective industrial iot platforms for connected
smart factories. In 2018 IEEE International Confer-
ence on Industrial Internet (ICII), page 146–152.
Choubey, S., Benton, R., and Johnsten, T. (2019). Pre-
scriptive equipment maintenance: A framework. In
2019 IEEE International Conference on Big Data (Big
Data), page 4366–4374.
Colombo, A. W., Karnouskos, S., Yu, X., Kaynak, O.,
Luo, R. C., Shi, Y., Leitao, P., Ribeiro, L., and
Haase, J. (2021). A 70-year industrial electronics
society evolution through industrial revolutions: The
rise and flourishing of information and communica-
tion technologies. IEEE Industrial Electronics Maga-
zine, 15(1):115–126.
Da Xu, L., He, W., and Li, S. (2014). Internet of things in
industries: A survey. IEEE Transactions on industrial
informatics, 10(4):2233–2243.
Flores, P., Moscoso-Martinez, M., Minchala, L. I.,
Vazquez-Rodas, A., and Astudillo-Salinas, D. (2018).
A simple reliable wireless bus design for home au-
tomation systems. In 2018 IEEE XXV International
Conference on Electronics, Electrical Engineering
and Computing (INTERCON), page 1–4.
Giorgetti, G., Gambi, E., Spinsante, S., Baldi, M.,
Morichetti, S., and Magnifico, I. (2008). An integrated
solution for home automation. In 2008 IEEE Inter-
national Symposium on Consumer Electronics, page
1–4.
Hassan, Q. F. (2018). Environment, People, and Time as
Factors in the Internet of Things Technical Revolution,
page 51–76. IEEE.
Hood, G. W. (2015). Industry standard models for de-
sign/discussion of manufacturing systems. In 2015 5th
Australian Control Conference (AUCC), page 12–15.
Industries, T. T. (2022). Rssi and snr.
Iyer, A. (2018). Moving from industry 2.0 to industry 4.0:
A case study from india on leapfrogging in smart man-
ufacturing. Procedia Manufacturing, 21:663–670.
Jayalaxmi, P., Saha, R., Kumar, G., Kumar, N., and Kim,
T.-H. (2021). A taxonomy of security issues in in-
dustrial internet-of-things: Scoping review for exist-
ing solutions, future implications, and research chal-
lenges. IEEE Access, 9:25344–25359.
Koziolek, H. (2018). Software architecture in process au-
tomation: Uml & the “smart factory”.
Lawrence, M. G. (2005). The relationship between relative
humidity and the dewpoint temperature in moist air:
A simple conversion and applications. Bulletin of the
American Meteorological Society, 86(2):225–234.
Li, C., Mantravadi, S., and Møller, C. (2020). Aau open
source mes architecture for smart factories – exploit-
ing isa 95. In 2020 IEEE 18th International Con-
ference on Industrial Informatics (INDIN), volume 1,
page 369–373.
Lin, J., Shen, Z., and Miao, C. (2017). Using blockchain
technology to build trust in sharing LoRaWAN IoT.
In Proceedings of the 2nd International Conference
on Crowd Science and Engineering, pages 38–43.
MATTIOLI, J., PERICO, P., and ROBIC, P.-O. (2020). Im-
prove total production maintenance with artificial in-
telligence. In 2020 Third International Conference
on Artificial Intelligence for Industries (AI4I), page
56–59.
Mekki, K., Bajic, E., Chaxel, F., and Meyer, F. (2019). A
comparative study of LPWAN technologies for large-
scale iot deployment. ICT express, 5(1):1–7.
Mohamed, M. (2018). Challenges and benefits of industry
4.0: An overview. International Journal of Supply and
Operations Management, 5(3):256–265.
NetSuite (2020). Iiot & manufacturing.
Pham, C., Bounceur, A., Clavier, L., Noreen, U., and Ehsan,
M. (2020). Radio channel access challenges in lora
low-power wide-area networks. In LPWAN Technolo-
gies for IoT and M2M Applications, pages 65–102.
Elsevier.
Pilsan, H. O., Amann, R., and Gerstenberg, M. (2019). Re-
alization of a small iiot node: A greenfield approach.
In 2019 20th International Conference on Research
and Education in Mechatronics (REM), page 1–5.
Powell, D., Riezebos, J., and Strandhagen, J. O. (2013).
Lean production and erp systems in small- and
medium-sized enterprises: Erp support for pull pro-
duction. International Journal of Production Re-
search, 51(2):395–409.
Reinsel, D., Gantz, J., and Rydning, J. (2018). The digiti-
zation of the world from edge to core.
Sauter, T., Soucek, S., Kastner, W., and Dietrich, D.
(2011a). The evolution of factory and building au-
tomation. IEEE Industrial Electronics Magazine,
5(3):35–48.
Sauter, T., Soucek, S., Kastner, W., and Dietrich, D.
(2011b). The evolution of factory and building au-
tomation. IEEE Industrial Electronics Magazine,
5(3):35–48.
Technologies, M. (2019). 6 challenges for industrial iot.
Wollschlaeger, M., Sauter, T., and Jasperneite, J. (2017).
The future of industrial communication: Automation
networks in the era of the internet of things and in-
dustry 4.0. IEEE industrial electronics magazine,
11(1):17–27.
IoTBDS 2023 - 8th International Conference on Internet of Things, Big Data and Security
254