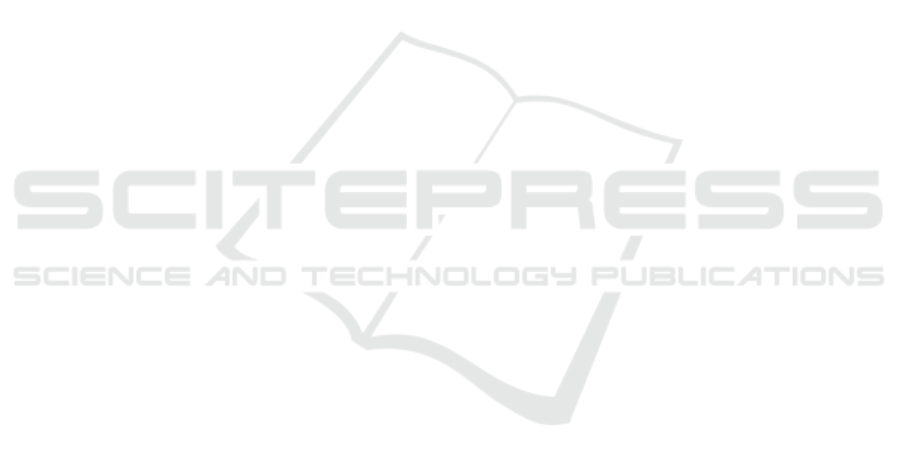
REFERENCES
Abbas, S. et al. (2023). Fractional Differential Equations
and Inclusions. World Scientific.
Allahem, A., Karthikeyan, A., Varadharajan, M., and
Rajagopal, K. (2022). Computational model of a
fractional-order chemical reactor system and its con-
trol using adaptive sliding mode control. Fractals,
30(10):2240243–87.
Ardjal, A., Bettayeb, M., Mansouri, R., and Zouak, B.
(2021). Design and implementation of a model-free
fractional order intelligent pi fractional order sliding
mode controller for water level tank system. ISA
transactions.
Camacho, O. and Smith, C. A. (2000). Sliding mode con-
trol: an approach to regulate nonlinear chemical pro-
cesses. ISA transactions, 39(2):205–218.
Ceballos, J., Coloma, N., Di Teodoro, A., and Ochoa-
Tocachi, D. (2020). Generalized fractional cauchy–
riemann operator associated with the fractional
cauchy–riemann operator. Advances in Applied Clif-
ford Algebras, 30(5):1–22.
Ceballos, J., Coloma, N., Di Teodoro, A., Ochoa-Tocachi,
D., and Ponce, F. (2022). Fractional multicomplex
polynomials. Complex Analysis and Operator Theory,
16(4):1–30.
Coloma, N., Di Teodoro, A., Ochoa-Tocachi, D., and
Ponce, F. (2021). Fractional elementary bicomplex
functions in the riemann–liouville sense. Advances in
Applied Clifford Algebras, 31(61).
Di Teodoro, A., Ochoa-Tocachi, D., Aboukheir, H., and
Camacho, O. (2022). Sliding-mode controller based
on fractional order calculus for chemical processes.
In 2022 IEEE International Conference on Automa-
tion/XXV Congress of the Chilean Association of Au-
tomatic Control (ICA-ACCA), pages 1–6. IEEE.
Di Teodoro, A., Ochoa-Tocachi, D., Aboukheir, H., and Ca-
macho, O. (2023). Sliding mode control based on a
generalized reduced fractional order model: Theoret-
ical approach. In The conference on Latin America
Control Congress, pages 47–58. Springer.
Dimassi, H., Winkin, J. J., and Wouwer, A. V. (2019).
A sliding mode observer for a linear reaction–
convection–diffusion equation with disturbances. Sys-
tems & Control Letters, 124:40–48.
Esp
´
ın, J., Castrillon, F., Leiva, H., and Camacho, O. (2022).
A modified smith predictor based–sliding mode con-
trol approach for integrating processes with dead
time. Alexandria Engineering Journal, 61(12):10119–
10137.
Gude, J. J. and Garc
´
ıa Bringas, P. (2022). Influence of the
selection of reaction curve’s representative points on
the accuracy of the identified fractional-order model.
Journal of Mathematics, 2022.
Haghighi, A. and Ziaratban, R. (2020). A non-integer slid-
ing mode controller to stabilize fractional-order non-
linear systems. Advances in Difference Equations,
2020(1):1–19.
Herrera, M., Camacho, O., Leiva, H., and Smith, C. (2020).
An approach of dynamic sliding mode control for
chemical processes. Journal of Process Control,
85:112–120.
Kadu, C., Khandekar, A., and Patil, C. (2018). Design
of sliding mode controller with proportional integral
sliding surface for robust regulation and tracking of
process control systems. Journal of Dynamic Systems,
Measurement, and Control, 140(9):091004.
Kilbas, A. A., Marichev, O., and Samko, S. (1993). Frac-
tional integrals and derivatives (theory and applica-
tions).
Kilbas, A. A., Srivastava, H. M., and Trujillo, J. J.
(2006). Theory and applications of fractional differ-
ential equations, volume 204. elsevier.
Li, Y., Chen, Y., and Podlubny, I. (2010). Stability
of fractional-order nonlinear dynamic systems: Lya-
punov direct method and generalized mittag–leffler
stability. Computers & Mathematics with Applica-
tions, 59(5):1810–1821.
Mehri, E. and Tabatabaei, M. (2021). Control of quadruple
tank process using an adaptive fractional-order sliding
mode controller. Journal of Control, Automation and
Electrical Systems, 32:605–614.
Miller, K. S. and Ross, B. (1993). An introduction to the
fractional calculus and fractional differential equa-
tions. Wiley.
Obando, C., Rojas, R., Ulloa, F., and Camacho, O.
(2023). Dual-mode based sliding mode control ap-
proach for nonlinear chemical processes. ACS omega,
8(10):9511–9525.
Patel, V., Guha, D., and Purwar, S. (2023). Distur-
bance observer-based higher-order sliding mode con-
troller for frequency regulation of hybrid power sys-
tems. International Journal of Automation and Con-
trol, 17(2):188–226.
Podlubny, I. (1994). Fractional-order systems and
fractional-order controllers. Institute of Experimen-
tal Physics, Slovak Academy of Sciences, Kosice,
12(3):1–18.
Prado, A. J., Herrera, M., Dominguez, X., Torres, J., and
Camacho, O. (2022). Integral windup resetting en-
hancement for sliding mode control of chemical pro-
cesses with longtime delay. Electronics, 11(24):4220.
Rasul, T. and Pathak, M. (2016). Control of nonlinear chem-
ical process using sliding mode control. In 2016 IEEE
1st International Conference on Power Electronics,
Intelligent Control and Energy Systems (ICPEICES),
pages 1–5. IEEE.
Salinas, L. R., Santiago, D., Slawi
˜
nski, E., Mut, V. A.,
Chavez, D., Leica, P., and Camacho, O. (2018). P+
d plus sliding mode control for bilateral teleoperation
of a mobile robot. International Journal of Control,
Automation and Systems, 16(4):1927–1937.
Sardella, M. F., Serrano, E., Camacho, O., and Scaglia, G.
(2020). Linear algebra controller design based on the
integral of desired closed-loop behavior: Application
to regulation and trajectory tracking in a typical chem-
ical process. Industrial & Engineering Chemistry Re-
search, 59(45):20131–20140.
Siddiqui, M. A., Anwar, M. N., and Laskar, S. H. (2020).
Sliding mode controller design for second-order un-
ICINCO 2023 - 20th International Conference on Informatics in Control, Automation and Robotics
138