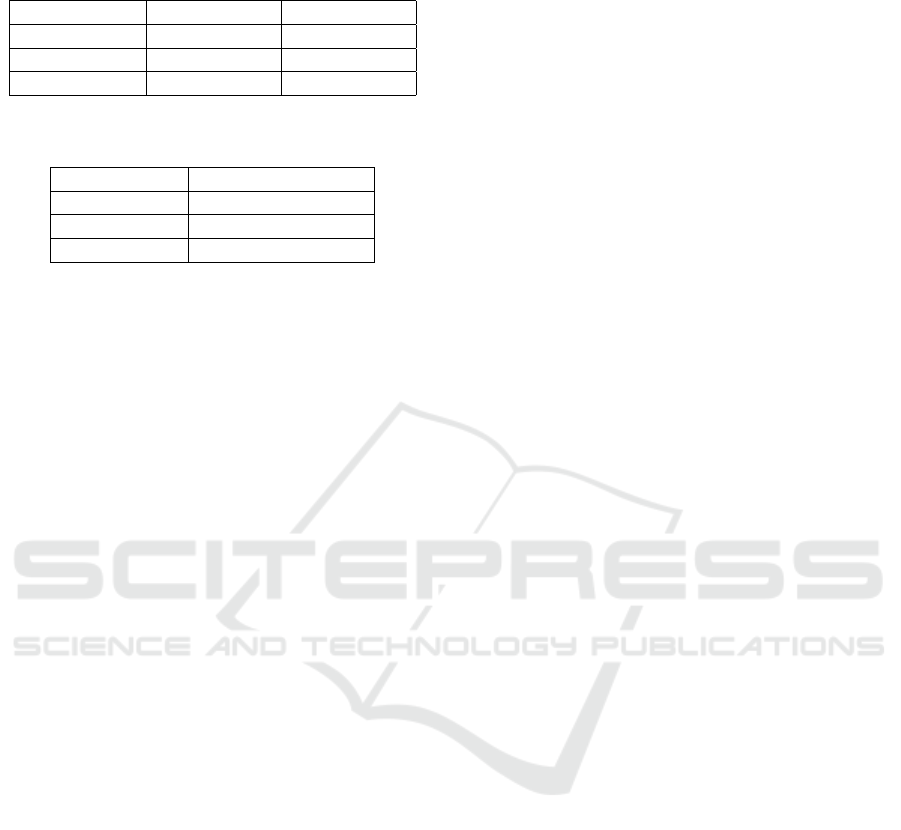
Table 3: Experiments: sensitivity to tangential force with
respect to taxel shapes.
along x [V/N] along y [V/N]
Parallelepiped 0.0342 0.0314
Spherical 0.00271 0.00276
Hemispheric 0.00668 0.00569
Table 4: Experiments: nonlinearity with respect to taxel
shapes.
Nonlinearity e
nl
[%]
Parallelepiped 3.18
Spherical 5.38
Hemispheric 11.7
ing the considered optoelectronic-based tactile sen-
sor: the photoreflector and the deformable layer. The
simulation has been used to determine how differ-
ent shapes of the reflective cells influence the per-
formance of the sensor. In particular, four different
shapes have been considered: parallelepiped, cylin-
drical, spherical, and hemispheric. Some tests have
been carried out to check the response of the simu-
lated model to different stimuli. Then, similar tests
have been repeated in a real setup in order to compare
the evaluated taxel shapes. Data from both the simu-
lation results and the measurements from the real sen-
sor have been used to discuss the best choice for the
taxel shape, also by considering the limitations due
to manufacturing processes. The results for proper-
ties such as linearity and sensitivity show differences
between simulations and experiments probably due
to the following reasons: in the simulation, the con-
sidered walls are completely reflective or absorbent,
while the real pads have white and black walls that are
not totally reflective or absorbent; the molds used for
realizing the silicone pads, being 3D printed, present
imperfections (i.e., grooves, small steps) that make
the actual walls not smooth, differently from those
in the simulation model, particularly for hemispheric
and spherical cases. The consequence of this lack of
smoothness is that, in the real case, the ray reflections
are locally quite different from the simulated case.
Future studies will be devoted to enhancing the sim-
ulation model by taking into account the aforemen-
tioned imperfections, e.g., by modifying the mechani-
cal model of the deformable layer taking into account
the non-smooth surfaces due to the production pro-
cess, or by investigating the possibility to consider
different reflection modalities in the ray tracing tech-
nique.
ACKNOWLEDGMENTS
This work was partially supported by the European
Commission under the Horizon Europe research grant
INTELLIMAN, project ID: 101070136
REFERENCES
Alqurashi, M. M., Ganash, E. A., and Altuwirqi, R. M.
(2022). Simulation of a low concentrator photovoltaic
system using comsol. Applied Sciences, 12(7).
Amiri, P., Casals, O., Maur, M. A. d., and Prades, J. (2022).
Ray tracing simulation of a gan-based integrated led-
photodetector system. In 2022 Int. Conf. on Numeri-
cal Simulation of Optoelectronic Devices (NUSOD).
Cirillo, A., Cirillo, P., De Maria, G., Natale, C., and Pirozzi,
S. (2014). A FE analysis of a silicone deformable in-
terface for distributed force sensors. AIP Conference
Proceedings, 1599(1):485–488.
Cirillo, A., Costanzo, M., Laudante, G., and Pirozzi, S.
(2021). Tactile sensors for parallel grippers: Design
and characterization. Sensors, 21(5).
Ferreira, G. M., Silva, V., Minas, G., and Catarino, S. O.
(2022). Simulation study of vertical p-n junction pho-
todiodes’ optical performance according to cmos tech-
nology. Applied Sciences, 12(5).
Khamis, H., Xia, B., and Redmond, S. J. (2019). A novel
optical 3d force and displacement sensor – towards in-
strumenting the papillarray tactile sensor. Sensors and
Actuators A: Physical, 291:174–187.
Lu, Z., Gao, X., and Yu, H. (2022). Gtac: A
biomimetic tactile sensor with skin-like heteroge-
neous force feedback for robots. IEEE Sensors Jour-
nal, 22(14):14491–14500.
NJL5908AR Datasheet (2015). NJL5908AR Datasheet
Ver.2015-02-17. New Japan Radio Co. LTD, Tokyo,
Japan.
Wang, S., She, Y., Romero, B., and Adelson, E. (2021).
Gelsight wedge: Measuring high-resolution 3d con-
tact geometry with a compact robot finger. In 2021
IEEE Int. Conf. on Robotics and Automation (ICRA).
Ward-Cherrier, B., Pestell, N., Cramphorn, L., Winstone,
B., Giannaccini, M. E., Rossiter, J., and Lepora, N. F.
(2018). The tactip family: Soft optical tactile sen-
sors with 3d-printed biomimetic morphologies. Soft
Robotics, 5(2):216–227.
ICINCO 2023 - 20th International Conference on Informatics in Control, Automation and Robotics
110