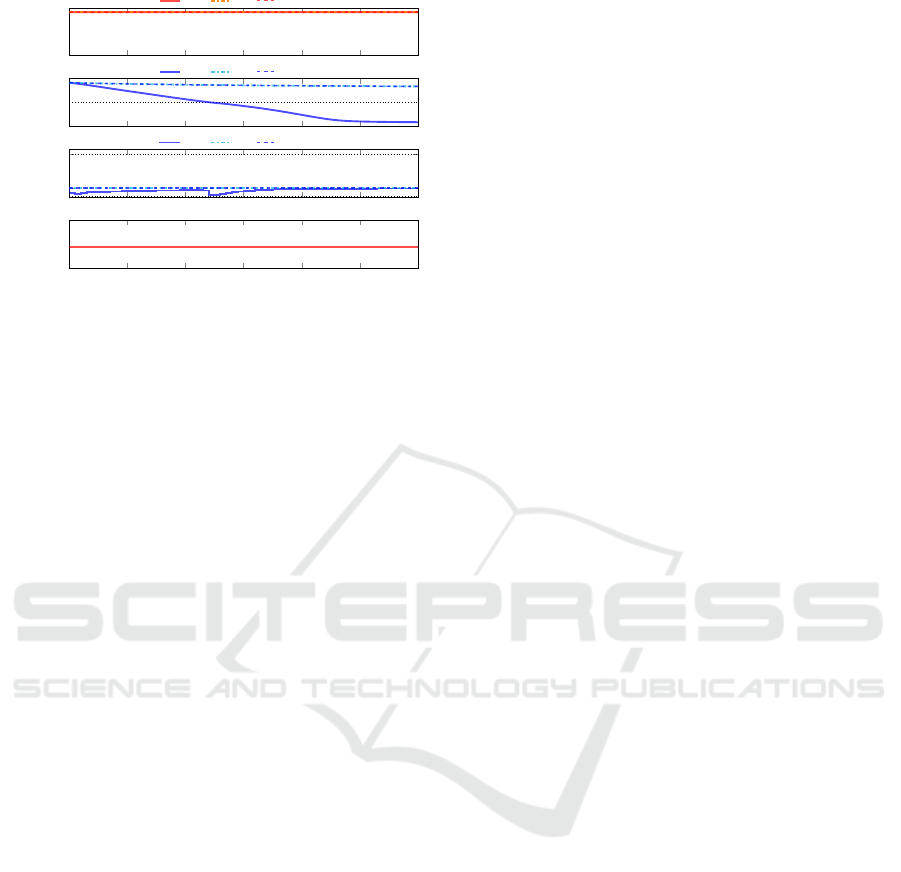
0
[U]
ogD*
16b
[U]
ogD
16
(M)
MPC
PID
Openloop
[U]
aqD
1,tol
[U]
aqD
1
(M)
MPC
PID
Openloop
A
F,min
A
0
F
A
F,max
A
F
(L/h)
MPC
PID
Openloop
0 5 10 15 20 25 30
O
0
E
Time (h)
O
E
(L/h)
Figure 9: Set-point tracking with infeasible initial condition
with MPC, PID, and open loop controllers.
5 CONCLUSION
This paper presents an NMPC (Nonlinear Model Pre-
dictive Control) approach for the uranium extraction-
scrubbing operation in the PUREX process. It was
shown that this approach favors the process control
objectives in stabilizing the system at the optimal
working condition with constraints satisfaction. As a
result, the process performance was increased quan-
titatively in terms of the amount of extracted ura-
nium. This study provides a good reference for future
developments on controlling extraction cycles in the
PUREX process. Constraint handling is the key factor
that makes MPC more beneficial for practical appli-
cations than the classical PID. Future developments
include stability guarantees, uncertainties handling,
and verification with the qualified simulation code
PAREX (Bisson et al., 2016) as a virtual plant in mul-
tiple application scenarios. Moreover, future studies
will be conducted at more sensitive point in the pro-
cess. Furthermore, the development of an observer is
essential to provide an output feedback MPC scheme
with limited measurements. Finally, experiments will
be conducted to evaluate the practical implementation
aspects of the developed control scheme.
ACKNOWLEDGEMENTS
The authors thank ORANO for partial financial sup-
port for the project.
REFERENCES
Andersson, J. A. E., Gillis, J., Horn, G., Rawlings, J. B., and
Diehl, M. (2019). CasADi – A software framework
for nonlinear optimization and optimal control. Math-
ematical Programming Computation, 11(1):1–36.
Bisson, J., Dinh, B., Huron, P., and Huel, C. (2016).
PAREX, A Numerical Code in the Service of
La Hague Plant Operations. Procedia Chemistry,
21:117–124.
Dinh, B., Baron, P., and Duhamet, J. (2008). The PUREX
Processs: Separation and Purification Operations. In
Treatment and Recycling of Spent Nuclear Fuel, pages
55–70. Le Moniteur.
Gardner, D. J., Reynolds, D. R., Woodward, C. S., and Ba-
los, C. J. (2022). Enabling new flexibility in the SUN-
DIALS suite of nonlinear and differential/algebraic
equation solvers. ACM Transactions on Mathemati-
cal Software (TOMS).
Hindmarsh, A. C., Brown, P. N., Grant, K. E., Lee, S. L.,
Serban, R., Shumaker, D. E., and Woodward, C. S.
(2005). SUNDIALS: Suite of nonlinear and differen-
tial/algebraic equation solvers. ACM Transactions on
Mathematical Software (TOMS), 31(3):363–396.
James, R. and David, M. (2022). Model Predictive Control:
Theory, Computation, and Design. Nob Hill Publish-
ing.
Komulainen, T., Doyle III, F. J., Rantala, A., and J
¨
ams
¨
a-
Jounela, S.-L. (2009). Control of an industrial copper
solvent extraction process. Journal of Process Con-
trol, 19(1):2–15.
Mayne, D. Q., Rawlings, J. B., Rao, C. V., and Scokaert, P.
O. M. (2000). Constrained Model Predictive Control:
Stability and Optimality. Automatica, 36:789–814.
Seborg, D. E., Edgar, T. F., Mellichamp, D. A., and Doyle
III, F. J. (2016). Process Dynamics and Control. John
Wiley & Sons, 4th edition.
Seemann, R. C. (1973). Predictive Control of a Mixer-
settler Extractor Separating the Rare-Earths. Techni-
cal report.
Shahcheraghi, S. H., Mousavi, S. M., and Dianatpour, M.
(2021). An Improved Control Strategy for an Indus-
trial Copper Solvent Extraction Process. Separation
Science and Technology, 57(11):1745–1761.
Vaudano, A. (2008). Overview of Treatment Processes.
In Monograph - Treatment and recycling of spent nu-
clear fuel. Le Moniteur.
W
¨
achter, A. and Biegler, L. T. (2005). On the Implementa-
tion of an Interior-Point Filter Line-search Algorithm
for Large-scale Nonlinear Programming. Mathemati-
cal Programming, 106(1):25–57.
Yang, H., He, L., Zhang, Z., Lu, R., and Tan, C. (2016).
Multiple-Model Predictive Control for Component
Content of CePr/nd Countercurrent Extraction Pro-
cess. Information Sciences, 360:244–255.
Yang, H., Meng, S., Sun, B., Wang, X., and Zhong, L.
(2010). The Multiple Models Predictive Control of
Component Content for the Rare Earth Extraction
Procession. In 2010 8th World Congress on Intelli-
gent Control and Automation. IEEE.
Nonlinear Model Predictive Control for Uranium Extraction-Scrubbing Operation in Spent Nuclear Fuel Treatment Process
43