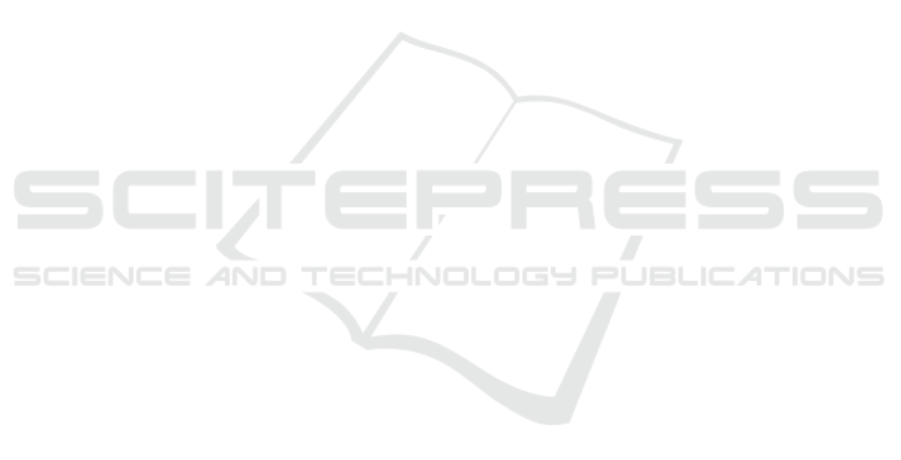
is oriented towards the measurement and characteri-
zation of the SMA pull-force, in order to determine
the maximum loads supported by the soft actuation
mechanism presented herein.
ACKNOWLEDGEMENTS
This work was funded by the project “iREHAB: Sis-
tema inteligente de Rehabilitaci
´
on usando un Ex-
oesqueleto para recuperar Habilidad motora en dis-
capacidades post-ACV, usando se
˜
nales Biol
´
ogicas
del paciente” sponsored by The Ministry of Science
Technology and Innovation (MinCiencias), program
918-2022 under GRANT CTO: 622-2022, Award ID:
91805.
REFERENCES
A. K. Mishra, V. S. Janani Kavi Priya, K. Pradeep, J. Sai
Vaishnav, and G. Kabhilesh, “Smart materials for ul-
trasonic piezoelectric composite transducer: A short
review,” Mater Today Proc, vol. 62, pp. 2064–2069,
Jan. 2022, doi: 10.1016/j.matpr.2022.02.514
M. Hodgins, G. Rizzello, D. Naso, A. York, and S. Se-
elecke, “An electro-mechanically coupled model for
the dynamic behavior of a dielectric electro-active
polymer actuator,” Smart Mater Struct, vol. 23, no. 10,
Oct. 2014, doi: 10.1088/0964-1726/23/10/104006
Z. Guo, Y. Pan, L. B. Wee, and H. Yu, “Design and control
of a novel compliant differential shape memory alloy
actuator,” Sens Actuators A Phys, vol. 225, pp. 71–80,
Apr. 2015, doi: 10.1016/j.sna.2015.01.016.
N. Bhatt, S. Soni, and A. Singla, “Analyzing the
effect of parametric variations on the perfor-
mance of antagonistic SMA spring actuator,”
Mater Today Commun, vol. 31, Jun. 2022, doi:
10.1016/j.mtcomm.2022.103728.
H. Jeong and W. D. Wang, “Self-adaptive detachable
pneumatic soft actuators using uniformly distributed
temporary-bonding-fasteners for wearable applica-
tions,” Sens Actuators A Phys, vol. 349, Jan. 2023,
doi: 10.1016/j.sna.2022.114083.
H. Jin, E. Dong, M. Xu, C. Liu, G. Alici, and Y. Jie, “Soft
and smart modular structures actuated by shape mem-
ory alloy (SMA) wires as tentacles of soft robots,”
Smart Mater Struct, vol. 25, no. 8, Jul. 2016, doi:
10.1088/0964-1726/25/8/085026.
G. Stano and G. Percoco, “Additive manufacturing aimed to
soft robots fabrication: A review,” Extreme Mechan-
ics Letters, vol. 42. Elsevier Ltd, Jan. 01, 2021. doi:
10.1016/j.eml.2020.101079.
Y. Wang, S. Zheng, Z. Song, J. Pang, and J. Li, “A Coupling
Dynamic Model for Studying the Physical Interaction
between a Finger Exoskeleton and a Human Finger,”
IEEE Access, vol. 8, pp. 125412–125422, 2020, doi:
10.1109/ACCESS.2020.3007799.
Ruth, D.J.S.; Sohn, J.-W.; Dhanalakshmi, K.; Choi,
S.-B. Control Aspects of Shape Memory Al-
loys in Robotics Applications: A Review over
the Last Decade. Sensors 2022, 22, 4860.
https://doi.org/10.3390/s22134860
D. Singh, R. Choudhury, M. Mukherjee, and Y. Singh,
“Development of non-linear models to evaluate the
NiTi SMA spring actuator”, JMES, vol. 16, no. 1, pp.
8754–8769, Mar. 2022.
Abdul Manan Khan, Youngshik Kim, Buhyun Shin, Mah-
yar Hasanzadeh Moghadam, Nader A. Mansour, Mod-
eling and control analysis of an arc-shaped SMA actu-
ator using PID, sliding and integral sliding mode con-
trollers, Sensors and Actuators A: Physical, Vol 340,
2022, 113523.
Castiblanco, J.C.; Mondragon, I.F.; Alvarado-Rojas,
C.; Colorado, J.D. Assist As Needed Exoskele-
ton for Hand Joint Rehabilitation Based on Mus-
cle Effort Detection. Sensors 2021, 21, 4372.
https://doi.org/10.3390/s21134372
K. Zuo, B. Wang, and Y. Wang, “Research on exoskele-
ton structure design of hand function rehabilitation
robot,” in 2022 12th International Conference on CY-
BER Technology in Automation, Control, and Intelli-
gent Systems, CYBER 2022, 2022, pp. 812–816. doi:
10.1109/CYBER55403.2022.9907104.
Mohammad H Elahinia and Mehdi Ahmadian 2005. An en-
hanced SMA phenomenological model: I. The short-
comings of the existing models. Smart Mater. Struct.
14 1297, 10.1088/0964-1726/14/6/022
Tanaka K 1986 A thermomechanical sketch of shape mem-
ory effect: one-dimensional tensile behavior Res.
Mech., Int. J. Struct. Mach. Mater. Sci. 18 251-63.
Shimawaki, S., Murai, T., Nakabayashi, M., Sugimoto,
H. (2019). Measurement of flexion angle of the fin-
ger joint during cylinder gripping using a three-
dimensional bone model built by X-ray computed to-
mography. Applied bionics and biomechanics, 2019.
Colorado J. (2012). BaTboT: a biologically in-
spired flapping and morphing bat robot actu-
ated by SMA-based artificial muscles. The-
sis (Doctoral), E.T.S.I. Industriales (UPM).
https://doi.org/10.20868/UPM.thesis.14657.
W. Coral, C. Rossi, J. Colorado, D. Lemus, and A. Bar-
rientos, SMA-Based Muscle-Like Actuation in Bio-
logically Inspired Robots: A State of the Art Re-
view, Smart Actuation and Sensing Systems - Re-
cent Advances and Future Challenges, Oct. 2012, doi:
10.5772/50209.
ICINCO 2023 - 20th International Conference on Informatics in Control, Automation and Robotics
688