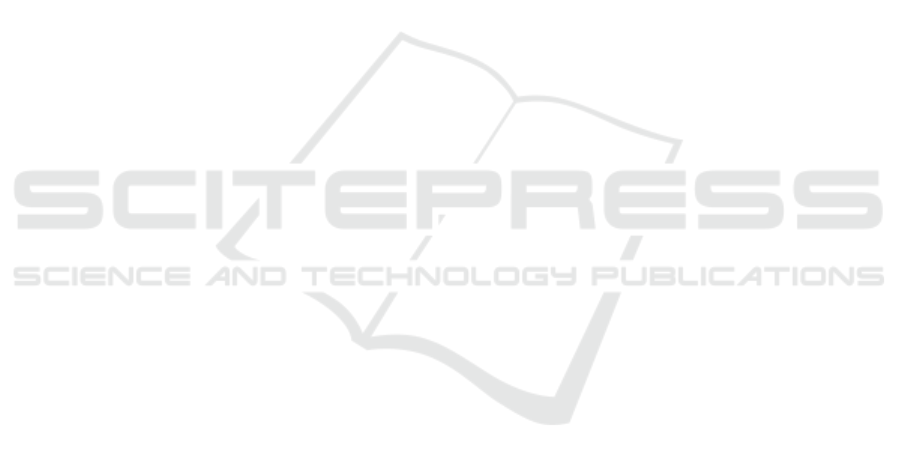
ACKNOWLEDGEMENTS
The research leading to these results has been sup-
ported by the AERIAL-CORE project (Horizon 2020
Grant Agreement No. 871479). The authors are
solely responsible for its content.
REFERENCES
Bellicoso, C. D., Buonocore, L. R., Lippiello, V., and Si-
ciliano, B. (2015). Design, modeling and control of a
5-dof light-weight robot arm for aerial manipulation.
In 2015 23rd Mediterranean Conference on Control
and Automation (MED), pages 853–858.
Cacace, J. and et al. (2021). Safe local aerial manipulation
for the installation of devices on power lines: Aerial-
core first year results and designs. Applied Sciences,
11(13).
Cacace, J., Finzi, A., Lippiello, V., Furci, M., Mimmo, N.,
and Marconi, L. (2016). A control architecture for
multiple drones operated via multimodal interaction
in search rescue mission. In 2016 IEEE International
Symposium on Safety, Security, and Rescue Robotics
(SSRR), pages 233–239.
Cacace, J., Finzi, A., Lippiello, V., Loianno, G., and San-
zone, D. (2013). Aerial service vehicles for indus-
trial inspection: Task decomposition and plan execu-
tion. In Ali, M., Bosse, T., Hindriks, K. V., Hoogen-
doorn, M., Jonker, C. M., and Treur, J., editors, Recent
Trends in Applied Artificial Intelligence, pages 302–
311, Berlin, Heidelberg. Springer Berlin Heidelberg.
Cacace, J., Giampetraglia, L., Ruggiero, F., and Lippiello,
V. (2023). A novel gripper prototype for helical bird
diverter manipulation. Drones, 7(1).
Cano, R., Perez, C., Prua
˜
no, F., Ollero, A., and Heredia, G.
(2014). Mechanical design of a 6-dof aerial manipu-
lator for assembling bar structures using uavs.
Chermprayong, P., Zhang, K., Xiao, F., and Kovac, M.
(2019). An integrated delta manipulator for aerial re-
pair: A new aerial robotic system. IEEE Robotics &
Automation Magazine, 26(1):54–66.
Franchi, A. (2019). Platforms with Multi-directional Total
Thrust, pages 53–65. Springer International Publish-
ing, Cham.
Hamaza, S., Georgilas, I., Fernandez, M., Sanchez, P.,
Richardson, T., Heredia, G., and Ollero, A. (2019).
Sensor installation and retrieval operations using an
unmanned aerial manipulator. IEEE Robotics and Au-
tomation Letters, 4(3):2793–2800.
IEEE (2009). Guide for maintenance methods on energized
power lines. Std 516-2009, pages 1–144.
Joseph, L. and Cacace, J. (2018). Mastering ROS for
Robotics Programming - Second Edition: Design,
Build, and Simulate Complex Robots Using the Robot
Operating System. Packt Publishing, 2nd edition.
Mishra, B., Garg, D., Narang, P., and Mishra, V. (2020).
Drone-surveillance for search and rescue in natural
disaster. Computer Communications, 156:1–10.
Miyazaki, R., Paul, H., Kominami, T., and Shimonomura,
K. (2020). Wire-suspended device control based
on wireless communication with multirotor for long
reach-aerial manipulation. IEEE Access, 8:172096–
172104.
Ollero, A., Tognon, M., Suarez, A., Lee, D., and Franchi,
A. (2022). Past, present, and future of aerial
robotic manipulators. IEEE Transactions on Robotics,
38(1):626–645.
Paul, H., Miyazaki, R., Ladig, R., and Shimonomura, K.
(2019). Landing of a multirotor aerial vehicle on an
uneven surface using multiple on-board manipulators.
In 2019 IEEE/RSJ International Conference on Intel-
ligent Robots and Systems (IROS), pages 1926–1933.
Ruggiero, F., Lippiello, V., and Ollero, A. (2018). Aerial
manipulation: A literature review. IEEE Robotics and
Automation Letters, 3(3):1957–1964.
Shimahara, S., Leewiwatwong, S., Ladig, R., and Shimono-
mura, K. (2016). Aerial torsional manipulation em-
ploying multi-rotor flying robot. In 2016 IEEE/RSJ
International Conference on Intelligent Robots and
Systems (IROS), pages 1595–1600.
Sibanyoni, S. V., Ramotsoela, D. T., Silva, B. J., and
Hancke, G. P. (2019). A 2-d acoustic source localiza-
tion system for drones in search and rescue missions.
IEEE Sensors Journal, 19(1):332–341.
Suarez, A., Heredia, G., and Ollero, A. (2018). Design of
an anthropomorphic, compliant, and lightweight dual
arm for aerial manipulation. IEEE Access, 6:29173–
29189.
Suarez, A., Nekoo, S. R., and Ollero, A. (2023). Ultra-
lightweight anthropomorphic dual-arm rolling robot
for dexterous manipulation tasks on linear infras-
tructures: A self-stabilizing system. Mechatronics,
94:103021.
Suarez, A., Real, F., Vega, V. M., Heredia, G., Rodriguez-
Casta
˜
no, A., and Ollero, A. (2020). Compliant bi-
manual aerial manipulation: Standard and long reach
configurations. IEEE Access, 8:88844–88865.
Tognon, M., Ch
´
avez, H. A. T., Gasparin, E., Sabl
´
e, Q.,
Bicego, D., Mallet, A., Lany, M., Santi, G., Re-
vaz, B., Cort
´
es, J., and Franchi, A. (2019). A truly-
redundant aerial manipulator system with application
to push-and-slide inspection in industrial plants. IEEE
Robotics and Automation Letters, 4(2):1846–1851.
Tosato, P., Facinelli, D., Prada, M., Gemma, L., Rossi, M.,
and Brunelli, D. (2019). An autonomous swarm of
drones for industrial gas sensing applications. In 2019
IEEE 20th International Symposium on ”A World of
Wireless, Mobile and Multimedia Networks” (WoW-
MoM), pages 1–6.
Trujillo, M. A., Martinez-de Dios, J. R., Martin, C., Vig-
uria, A., and Ollero, A. (2019). Novel aerial manip-
ulator for accurate and robust industrial ndt contact
inspection: A new tool for the oil and gas inspection
industry. Sensors, 19(6).
Uzakov, T., Nascimento, T. P., and Saska, M. (2020). Uav
vision-based nonlinear formation control applied to
inspection of electrical power lines. In 2020 Inter-
national Conference on Unmanned Aircraft Systems
(ICUAS), pages 1301–1308.
Design and Control of a Novel High Payload Light Arm for Heavy Aerial Manipulation Tasks
473