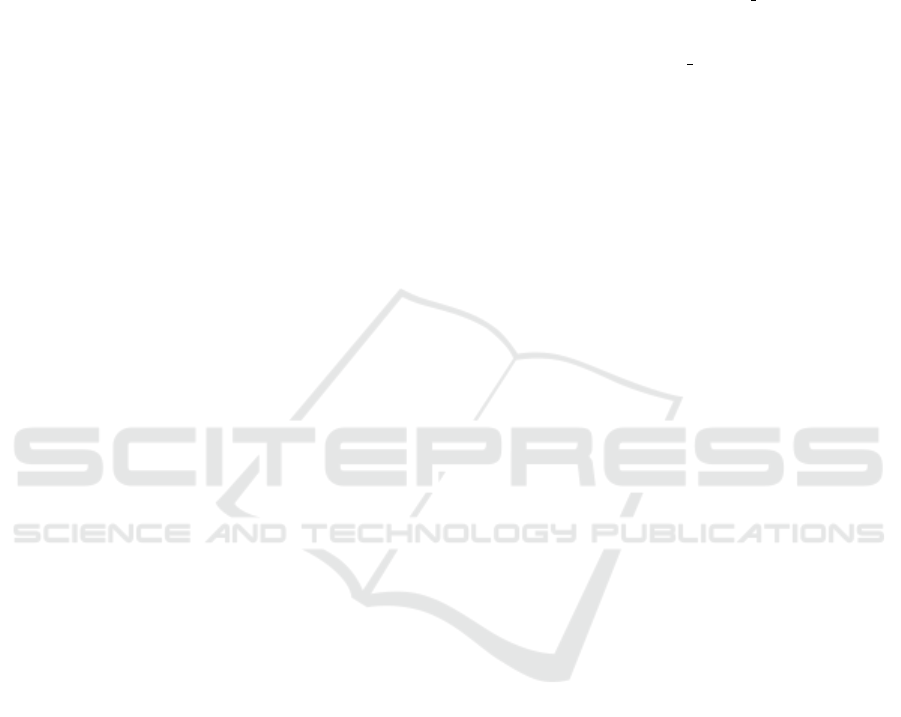
6 CONCLUSIONS
This paper proposed a low-cost printed circuit board
which can be easily reconfigurable to work with dif-
ferent force-torque sensors based on strain gauges.
Moreover it has an impedance control layer stackup
to allow fast and reliable data transmission and other
methods as ground stitching are employed to reduce
electromagnetic interference. Besides, the compo-
nents distributions were made in order to carry out
a fast assembly process of SMD components using
a pick-and-place machine and a solder oven. It is
intended that this design can be useful to the user
that requires a low cost system to measure forces in
robotics applications.
ACKNOWLEDGEMENTS
This work has been supported by the Instituto de In-
vestigaciones en Ingenier
´
ıa as well as the School of
Electrical Engineering from the University of Costa
Rica.
REFERENCES
Aguirre-Ollinger, G. and Yu, H. (2021). Omnidirectional
platforms for gait training: Admittance-shaping con-
trol for enhanced mobility. Journal of Intelligent &
Robotic Systems, 101(3):52.
Armleder, S., Dean-Leon, E., Bergner, F., and Cheng, G.
(2022). Interactive force control based on multimodal
robot skin for physical human-robot collaboration.
Advanced Intelligent Systems, 4(2):2100047.
Bussmann, K., Dietrich, A., and Ott, C. (2018). Whole-
body impedance control for a planetary rover with
robotic arm: Theory, control design, and experimental
validation. In 2018 IEEE International Conference on
Robotics and Automation (ICRA), pages 910–917.
Calanca, A., Muradore, R., and Fiorini, P. (2016). A re-
view of algorithms for compliant control of stiff and
fixed-compliance robots. IEEE/ASME Transactions
on Mechatronics, 21(2):613–624.
Chen, D., Song, A., and Li, A. (2015). Design and cal-
ibration of a six-axis force/torque sensor with large
measurement range used for the space manipulator.
Procedia Engineering, 99:1164–1170. 2014 Asia-
Pacific International Symposium on Aerospace Tech-
nology, APISAT2014 September 24-26, 2014 Shang-
hai, China.
Cheng, G., Dean-Leon, E., Bergner, F., Rogelio Guadar-
rama Olvera, J., Leboutet, Q., and Mittendorfer, P.
(2019). A comprehensive realization of robot skin:
Sensors, sensing, control, and applications. Proceed-
ings of the IEEE, 107(10):2034–2051.
Circuits, S. (2020). High-speed pcb design guide. pages
30-32.
Data Translation (2017). Dt9828 usb multi-sensor measure-
ment module. Datasheet. https://www.mccdaq.com/
PDFs/specs/DT9829-Datasheet.pdf.
DATAQ Instruments (2014). Di-718b 8b module data
logger system. Datasheet. https://www.dataq.com/
resources/pdfs/datasheets/di718b ds.pdf.
DATAQ Instruments (2018). Di-718bx 8b module data
logger. Datasheet. https://www.dataq.com/resources/
pdfs/datasheets/di718bx ds.pdf.
DATAQ Instruments (2019). Di-4718b usb or eth-
ernet data acquisition (daq) system. Datasheet.
https://www.dataq.com/resources/pdfs/datasheets/di-
4718b-data-logger-ds.pdf .
Dean, E., Ramirez-Amaro, K., Bergner, F., and Cheng, G.
(2019). Robot skin: Fully-compliant control frame-
work using multi-modal tactile events. P
¨
ADI Bolet
´
ın
Cient
´
ıfico de Ciencias B
´
asicas e Ingenier
´
ıas del ICBI,
7(Especial 1).
Dietrich, A., Bussmann, K., Petit, F., Kotyczka, P., Ott, C.,
Lohmann, B., and Albu-Sch
¨
affer, A. (2016). Whole-
body impedance control of wheeled mobile manipula-
tors. Autonomous Robots, 40(3):505–517.
Fr
´
emy, J., Ferland, F., Lauria, M., and Michaud, F. (2014).
Force-guidance of a compliant omnidirectional non-
holonomic platform. Robotics and Autonomous Sys-
tems, 62(4):579–590.
Iskandar, M., Quere, G., Hagengruber, A., Dietrich, A., and
Vogel, J. (2019). Employing whole-body control in
assistive robotics. In 2019 IEEE/RSJ International
Conference on Intelligent Robots and Systems (IROS),
pages 5643–5650.
JLCPCB (2023). Pcb manufacturing & assembly capabil-
ities. https://jlcpcb.com/capabilities/pcb-capabilities.
Last update on July 24, 2023.
Kebede, G. A., Ahmad, A. R., Lee, S.-C., and Lin, C.-
Y. (2019). Decoupled six-axis force–moment sensor
with a novel strain gauge arrangement and error re-
duction techniques. Sensors, 19(13).
Kim, K. S., Kwok, A. S., Thomas, G. C., and Sen-
tis, L. (2014). Fully omnidirectional compliance in
mobile robots via drive-torque sensor feedback. In
2014 IEEE/RSJ International Conference on Intelli-
gent Robots and Systems, pages 4757–4763.
Kim, K. S., Llado, T., and Sentis, L. (2016). Full-body
collision detection and reaction with omnidirectional
mobile platforms: a step towards safe human-robot in-
teraction. Autonomous Robots, 40(2):325–341.
Kollmitz, M., B
¨
uscher, D., Schubert, T., and Burgard, W.
(2018). Whole-body sensory concept for compli-
ant mobile robots. In 2018 IEEE International Con-
ference on Robotics and Automation (ICRA), pages
5429–5435.
Lin, C.-C., Su, C.-Y., Lin, S.-T., Chen, C.-Y., Yeh, C.-N.,
Lin, C.-H., Wang, L.-W., Kuo, S.-Y., and Chien, L.-J.
(2019). 6-dof force/torque sensor. In 2019 14th Inter-
national Microsystems, Packaging, Assembly and Cir-
cuits Technology Conference (IMPACT), pages 191–
194.
A Low-Cost Printed Circuit Board Design for External Force Measuring in Robotic Applications
217