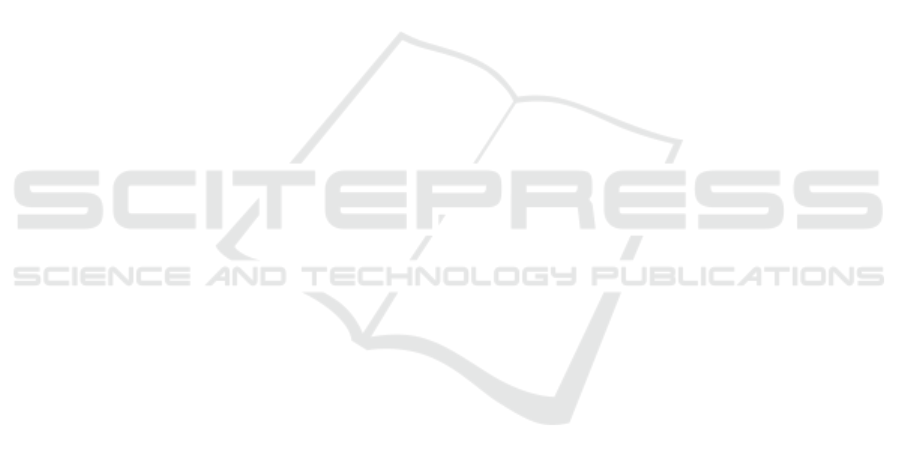
displacement of the ballast water tank. If the air
pressure is not removed, the drainage of the
submarine will increase rapidly due to the rapid
expansion of the gas in the ballast water tank in the
later recovery period, which is consistent with the
result of too fast floating speed in Figure 1 (b). The
displacement and floating speed can be effectively
controlled when the air pressure is removed properly.
Figure 1 (e) shows the trim change of the submarine.
If the air pressure is not released or released in
advance, a large trim will occur due to excessive and
insufficient displacement. If the air pressure is not
released, the trim will exceed 20 degrees. If the air
pressure is released too early, the submarine will sink
to the seabed with a large trim. Figure 1 (f) shows the
change of the submarine's heel. At the initial stage of
damage and water ingress, due to the sharp increase
of the heel of the submarine under the additional
force, after taking the blowing out measures, the
additional torque decreases, and the heel decreases
significantly, basically maintaining a normal state.
5 CONCLUSION
In view of the difficulty of attitude control in
emergency recovery of submarine ballast tank by
high-pressure air blowing, this paper takes the
pressure gas in ballast tank as the research object,
builds mathematical and physical models of high-
pressure air blowing and pressure relief, and analyzes
the influence of high-pressure air release timing on
recovery results in the process of emergency recovery
of submarine high-pressure air blowing combined
with submarine accident examples.
1) When applying high-pressure air to blow out
the main ballast water tank of the submarine to
retrieve the submarine, the duration of high-pressure
air blowing out and the time to relieve the pressure in
the ballast water tank are very important, which not
only seriously affect the submarine attitude in the
recovery process, but also directly determine whether
the submarine is successfully recovered.
2) As the recovery depth of the submarine
decreases, the gas in the ballast tank expands rapidly.
If the air pressure is not relieved, the submarine will
appear serious heeling and rolling phenomenon
during floating, and the floating speed and pitch are
too large, making the submarine appear dangerous
attitude.
3) If the pressure of the ballast water tank is
released too early in the recovery process, the
submarine will have insufficient positive buoyancy at
the later stage of recovery, resulting in failure of
emergency recovery.
4) It is necessary to develop a prediction system
for submarine high-pressure air blowing emergency
recovery movement law, evaluate submarine
movement status in real time, change the time and
opportunity of high-pressure air blowing off the main
ballast tank and the time to release air pressure, and
control submarine recovery movement posture by
changing submarine speed, steering and other
dynamic anti sinking measures, so as to provide
decision-making support for submarine commanders
to formulate emergency recovery plans.
REFERENCES
LIU H, PU J Y, LI Q X, et al. The experiment research of
submarine high-pressure air blowing of main ballast
tanks (J).Journal of Harbin Engineering University,
2013, 34(1): 34-39.
YANG S, YU J Z, CHENG D, et al. Theoretical analysis
and experimental validation on gas jet blowing-off
process of submarine emergency (J). Journal of Beijing
University of Aeronautics and Astronautics, 2009,
35(4):411-416.
LIU R J, XIAO C R, CHEN D B. Experiment and
simulation study of high pressure air blowing
submarine’ s ballast tanks(J). Journal of Sichuan
ordnance industry, 2014, 35(2):5-8.
ZHANG J H, HU K, LIU C B. Numerical simulation on
compressed gas blowing ballast tank of submarine
(J).Journal of Ship Mechanics, 2015, 19(4): 363-368.
LIU C B, DING F L, TIAN B L. Research on simulation
prediction of submarine emergency floating
maneuverability (J).Computer Simulation, 2013, 30(7):
29-32.
WU W Y, HAN Z Z, CHENG Z J. Research on accurate
water quantity control experiment of underwater high-
pressure air blowing off (J).Ship science and technology,
2015, 37(8): 132-134.
LIU H, LI Z H, LI Q X, et al. Forecasting of motion posture
and regular pattern during submarine power anti-sinking
(J). Journal of naval university of engineering, 2019,
31(1): 51-58.
00JIN T, LIU H, WANG J Q. Emergency recovery
manoeuvring under flooded submarine (J). Journal of
Ship Mechanic, 2010, 14(1-2): 34-43.
ANIT 2023 - The International Seminar on Artificial Intelligence, Networking and Information Technology
332