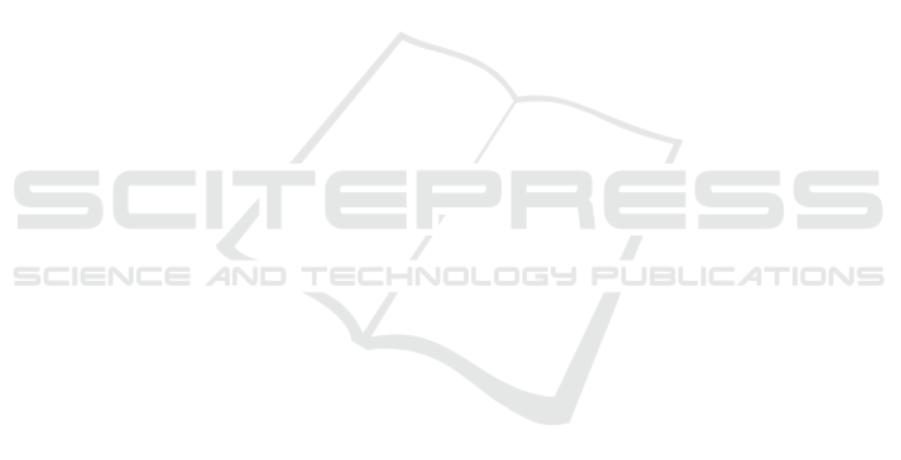
In the experimental range, reducing the apparent
gas velocity and filter particle size and increasing
the filter material thickness can increase the
characteristic parameter b in the rising section of
filtration efficiency, and reduce the characteristic
parameter a in the falling section of filtration
efficiency, so as to improve the filtration efficiency
during the entire filtration time.
From the perspective of filtration efficiency of
granular bed filter, the operating conditions can be
selected as the apparent gas velocity of 0.25 m/s, the
filter material thickness is 150 mm, and the filter
material particle size is 0.38~0.83 mm. Under the
experimental conditions, the filtration efficiency of
the granular bed filter is 99.20%.
REFERENCES
Wang S M, Shi Q M, Wang S Q, et al. Resource property
and exploitation concepts with green and low-carbon
of tar-rich coal as coal-based oil and gas(J). Journal of
China Coal Society, 2021, 46(05): 1365-1377.
https://doi.org/10.13225/j.cnki.jccs.ST21.0860
Ren L, Yang F L, Jia Y J, et al. Effect of conditions of
low-rank coal pyrolysis on gas phase product
Distribution and Semi-coke Structure (J). Coal
Conversion, 2019, 42(06): 17-27.
https://doi.org/10.19726/j.cnki.ebcc.201906003
Li T, Wang Q, Shen Y F, et al. Effect of filter media on
gaseous tar reaction during low-rank coal pyrolysis (J).
Journal of Fuel Chemistry and Technology, 2021, 49(3):
257-264. https://doi.org/10.19906/j.cnki.JFCT.2021009
Du X, Huang M L, Qi B B, et al. Experimental study on
the two-stage purification of retorting gas in the
process of pulverized coal pyrolysis (J). Journal of
China Coal Society, 2018, 43(10): 2911-2917.
https://doi.org/10.13225/j.cnki.jccs.2018.0246
Yang S Q, Du L, Li S G, et al. Advances on dust removal
technology of high temperature pyrolysis of coal gas
containing dust and oil (J). Clean Coal Technology,
2021, 27(01): 193-201.
https://doi.org/10.13226/j.issn.1006-6772.A20110301
Zhang Y Q, Liang P, Yu J, et al. Studies of granular bed
filter for dust removal in the process of coal pyrolysis
by solid heat carrier(J). Royal Society of Chemistry,
2017, 7(33): 20266-20272.
https://doi.org/10.1039/C7RA01467H
Yan S, Sun G G, Sun Z P, et al. Advances in research on
granular bed filter for dust removal (J). Chemical
Industry and Engineering Progress, 2017, 36(09):
3152-3163.
https://doi.org/10.16085/j.issn.1000-6613.2017-0014
Wang Q L, Sun G G, Zhou F W, et al. Experimental Study
on Removal of PM2.5 by Cyclone-Granular Bed (J).
Journal of Filtration & Separation, 2016, 26(03):
1-4+12. https://doi.org/10.3969/j.issn.1005-8265.2016.
03.001
Wang M, Du X, Wang Y. Analysis and optimization on
two-stage dust removal of cyclone separator-granular
bed filter (J). Chemical Engineering (China), 2020,
48(04): 55-59.
https://doi.org/CNKI:SUN:IMIY.0.2020-04-012
Fan Y J, Liu J Q, Ma C, et al. Cold model experiments on
gas-solid separation performance of granules moving
bed (J). Clean Coal Technology, 2021, 27(04): 90-96.
https://doi.org/10.13226/j.issn.1006-6772.CE21032901
CHEN Junlin, LI Xunfeng, WANG Yongwei, et al.
Numerical study on the dust removal characteristics in
granular bed filter (J). Journal of Engineering
Thermophysics, 2018, 39(09): 1997-2004.
https://doi.org/CNKI:SUN:GCRB.0.2018-09-018
Liu S X, Huang F, Chang L, et al. Mathematical modeling
and experimental study on filtration efficiency of
granular filtration bed (J). Journal of China Coal
Society, 2016, 41(S2): 542-547.
https://doi.org/10.13225/j.cnki.jccs.2016.0259
Yan S. Research on entrainment of pyrolysis fly ash of oil
shale and dust removal performances of granular bed
filter (D). China University of Petroleum (Beijing),
2018.
https://doi.org/10.27643/d.cnki.gsybu.2018.001410
Wang M, Rong L, Wang Y, et al. Performance analysis of
granular bed filter based on semi-coke filter medium(J).
Coal Conversion, 2019, 42(06): 41-48.
https://doi.org/10.19726/j.cnki.ebcc.201906006
Bruno M W, Cleiton B P, Nilson R M, et al. Filtration of
Dust in an Intermittent Moving Granular Bed Filter:
Performance and modeling(J). Separation and
Purification Technology, 2014, 133(8): 108-119.
https://doi.org/10.1016/j.seppur.2014.06.051
ANIT 2023 - The International Seminar on Artificial Intelligence, Networking and Information Technology
492