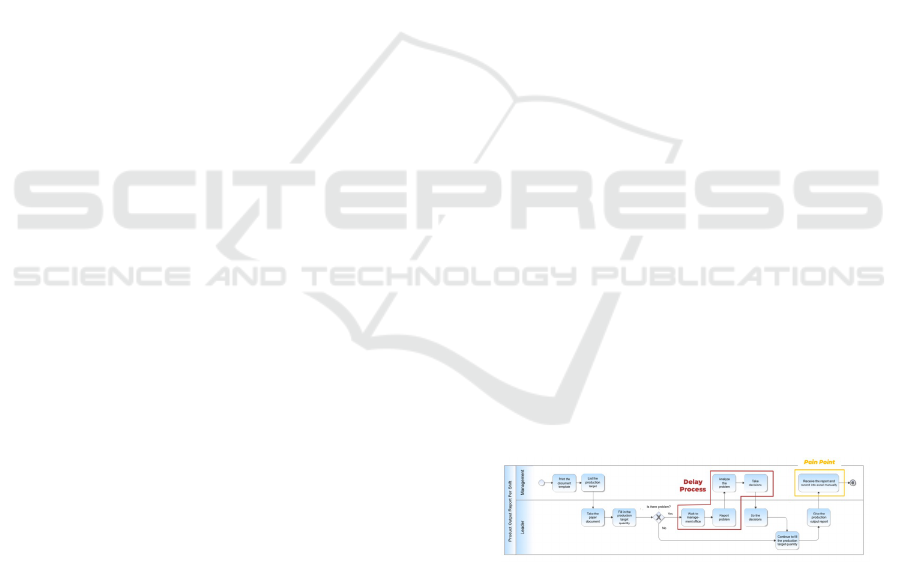
data to users to help evaluate and correct the input
data (Laudon and P, 2014). There are three phases on
the implementation of information system; pre imple-
mentation, implementation, and post implementation
(Dachyar and Dewi, 5 05).
2.3 Digital Manufacturing Supply
Chain
Digital Manufacturing Supply Chain can be defined
as real-time acquisition of data about the management
and decision-making of all supply chain business ac-
tivities, using digital information technology, and try-
ing to reduce supply chain risks and improve supply
chain performance through intelligent management
(Liu, 2 01). Most of the benefits in manufacturing
from digital transformation can be summarized in five
groups; to increased productivity where development
and design processes, quality with high-resolution
measurements, the costs involved in data capture and
analysis of the manufacturing process, product cus-
tomization, and safety in the workplace where dan-
gerous tasks can be performed by robots (Albukhitan,
2020). Digital transformation implies technological
advances that support existing processes (Liu, 2 01).
Technology architecture contributes to the essential
requirements of IoT applications: Security, Adapt-
ability, Intelligence, Real Time, and Regulation Com-
pliant (Saragih et al., 2018).
2.4 Business Process Reengineering
Business Process Reengineering (BPR) is the funda-
mental rethinking and radical redesign of business
processes to achieve dramatic improvements in crit-
ical contemporary performance measures, such as
cost, quality, service and speed (Herzog et al., 9 10).
BPR in Manufacturing Supply Chain is a process of
modeling and documenting information architecture
can be a sufficient starting point to ensure the suc-
cess of BPR (Nabelsi and Gagnon, 5 05). The BPR
approach and the use of RFID create efficiencies in
terms of time & cost (Bevilacqua et al., 2011). In
practice, there are many ways to do BPR. However,
there are 10 best practices; task elimination, task com-
position, integral technology empower, order assign-
ment, resequencing, specialist-generalist, integration,
parallelism, and numerical involvement (Mansar and
Reijers, 2007). Make a model using enterprise archi-
tecture (EA) notation is a strategic framework map-
ping of the new business process (Dachyar et al., 0
10).
3 METHODOLOGY
The water pump production process improvement
model uses a Business Process Reengineering ap-
proach to determine scenarios in the design of infor-
mation systems as a solution. The data used in this
research are interview with stakeholders, observation,
and production output documents. Activities will be
created into an As-Is model with enterprise architec-
ture (EA) notation using iGrafx software. This model
will produce output in the form of the total time of the
entire production reporting process. Based on these
results, an analysis of the problem regarding the waste
of activities will be carried out. After knowing the
problem, a new business process model will be de-
signed, namely the To-Be model. BPR best practices
are carried out to obtain alternative solutions in the
form of several scenarios. The next phase is the de-
sign of the information system, which is consist of 4
phases, namely database design, system design, sys-
tem usage flow, and interface design.
4 RESULT
Figure 1 shows the current water pump production
output reporting process. In the last process, namely
receiving reports and recording reports into Excel
manually, it creates a vulnerability for human error,
which are:
• Writing numbers on production report paper can
be wrong due to mistakes in writing back from
targets that are on the computer to paper
• Error reading the number written by the leader re-
garding the number of units produced
• Error in entering data into excel
Figure 1: Production Output Reporting As-Is Model.
In addition, in the middle of the process, if there
is a problem, the leader must walk to the office and
report the problem, then the section head will analyze
the problem so that decision making is a process that
has high barriers or a delay process. From the simu-
lation results on iGrafx (Table 1) it is found that the
average waiting time for this process is 0.42 hours.
When divided by the production takt time of 1 water
pump model, which is 33 seconds/unit, an opportu-
nity loss of 45 units/shift is obtained.
ICAISD 2023 - International Conference on Advanced Information Scientific Development
228