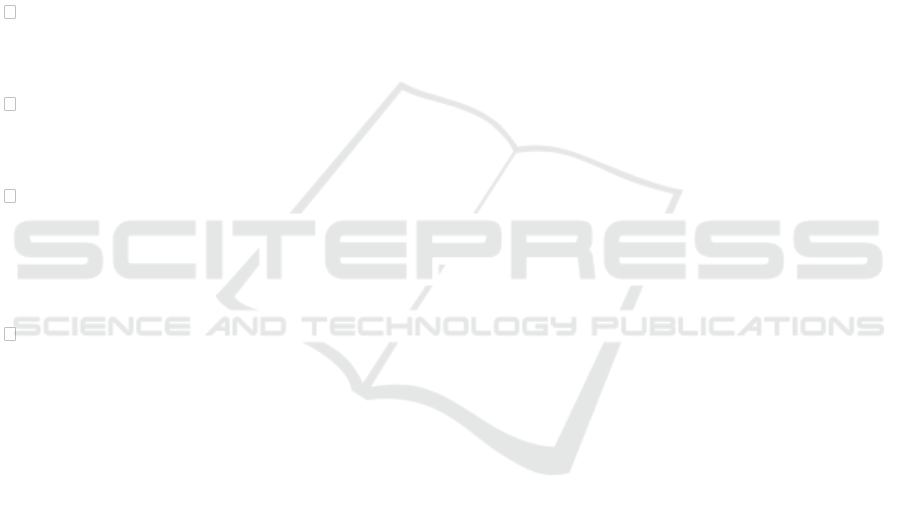
4 CONCLUSION
This paper focused on evaluation of coating
performance of steel substrate which is used in
conveyor rollers which works under highly abrasive
environments. Main objective is to increase the three-
body wear resistance by molybdenum coating using
plasma spray technique. The results obtained from the
experimental analysis proved the improvement in
wear resistance after molybdenum coating. EDAX
and SEM analysis are performed to composition
identification and to find thickness of the coating.
Enhanced resistance to mass loss indicates the
improvement in wear resistance of molybdenum
coated steel. Following observations are made from
the experimental result and analysis
The observed trend indicates that both the
uncoated and coated samples exhibit a linear variation
as the parameters such as speed, load, and grain size
increase.
At lower loads and speeds, the disparity in wear
between the coated specimen and the uncoated
specimen is negligible in comparison to higher loads
and speeds.
The findings indicate that when subjected to
higher loads, an oxide layer is generated on the
surface, acting as a lubricant and decreasing the
friction coefficient. As a result, the presence of
abrasives is reduced, leading to a decrease in mass
loss and material wear.
The experiment was conducted with a consistent
coating thickness ranging from 100 to 150 microns.
This approach can be expanded to create coatings of
different thicknesses.
This research highlights the potential of
molybdenum powder coatings to enhance the
durability and lifespan of steel rollers in conveyor
systems operating in harsh environments. The
findings contribute to the development of effective
strategies for reducing wear and optimizing the
performance of mining and construction equipment.
The experimentation was conducted using the
atmospheric plasma spray process, but it is possible
to expand the study by employing various thermal
spray processes and assessing their performance.
REFERENCES
C.S. , Ramesh, Adarsha H., Anoushka Chaturvedi, and
Nikitha Nair. 2018. “Investigations on the Effect of
Molybdenum (Mo) and Molybdenum Silicon Carbide
(Mo-10% Sic) Composite Coatings on Mild Steel
Substrate using HVOF Technique,.” Materials Today:
Proceedings (Materials Today) 5 (11): 24422-24427.
doi:https://doi.org/10.1016/j.matpr.2018.10.238.
Chávez, Carlos Alberto Guevara, Jorge Leobardo Acevedo
Dávila, Pedro Hernandez Gutierrez, Jose Jorge Ruiz
Mondragon, and Patricia del Carmen Zambrano-
Robledo. 2018. “Tribological and microstructural
behaviour in coatings applied using GTAW and HVOF
(thermal spraying process) and used to recover
AISI/SAE D2 grade tool steels.” Intl.Journal of
Welding 32 (10): 660-666. doi: doi:
10.1080/09507116.2017.1347347.
G, Bruno, Fanara C, Guglielmetti F, and Malard B. 2006.
“Characterization and residual stress analysis of wear
resistant Mo thermal spray-coated steel gear wheels,.”
Surface and Coatings Technology 200 (14-15): 4266-
4276.
H., Adarsha, Ramesh C.S. , Nair Nikitha,
Karisiddeshwaraswamy K.M., and Chaturvedi,
Anoushka . 2018. “Investigations on the Abrasive Wear
Behaviour of Molybdenum Coating on SS304 and A36
using HVOF Technique,.” Materials Today:
Proceedings, 5 (11): 25667-25676.
Han, Ya-guang, Yong Yang, Lei Wang,, Xue-guang Chen,
Zhenhua Chu, Xu-ning Zhang, Yanchun Dong, et al.
2017. “Microstructure and properties of in-situ TiB 2
matrix composite coatings prepared by plasma
spraying.” Applied Surface Science 431. doi:Applied
Surface Science.
Huang, , Long, Xiangtao Deng, Ye Jia, Chengru Li, and
Zhaodong Wang. 2018. “Effects of using (Ti,Mo)C
particles to reduce the three-body abrasive wear of a
low alloy steel.” Wear 410-411.
doi:10.1016/j.wear.2018.06.008.
Hwang, Byoungchul, Sunghak Lee, and Jeehoon Ahn.
2004. “Correlation of microstructure and wear
resistance of molybdenum blendcoatings fabricated by
atmospheric plasma spraying.” Materials Science and
Engineering 152-163.
M.M.A. , Bepari, and Shorowordi K.M. 2004. “Effects of
molybdenum and nickel additions on the structure and
properties of carburized and hardened low carbon
steels,.” Journal of Materials Processing Technology,
155-156: 1972-1979.
doi:https://doi.org/10.1016/j.jmatprotec.2004.04.060.
Matache, Gheorghe & Puscasu, Cristian & Paraschiv,,
Alexandru & Trusca, and Oana. 2015. “Investigation of
some Intrinsic Properties of Thermal Sprayed
Molybdenum Coatings for Railway Axle
Applications.” Investigation of some Intrinsic
Properties of Thermal Sprayed Molybdenum Coatings
for Railway Axle Applications 811: 19-23.
N, González, Juan Zapata Pérez, Martínez V, Gadow R, and
García J. 2020. “Manufacturing parameter analysis for
alumina coating on steel substrate by automated image
processing of isolated splats samples.” PLoS ONE 15:
e0240928.
Patel G C, Manjunath, Pradeep N B, Girisha L, Harsha H
M, and Arun Kumar Shettigar. 2022. “Experimental
analysis and optimization of plasma spray parameters
on microhardness and wear loss of Mo-Ni-Cr coated
Enhancement of Three-Body Wear Resistance of Steel Substrate Using Molybdenum Coating for Steel Roller Conveyor
123