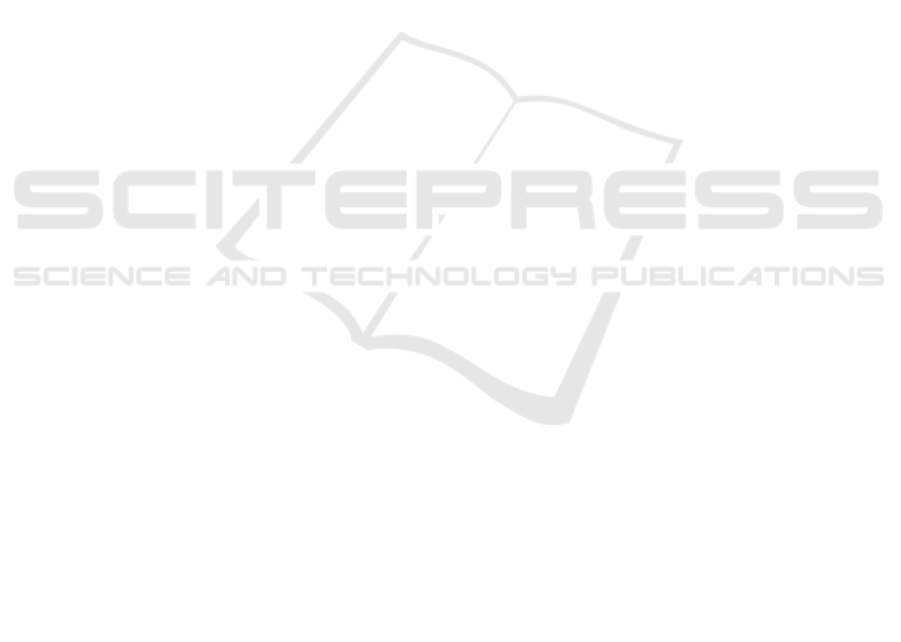
REFERENCES
Sorrentino, G., Circosta, S., Galluzzi, R., Amati, N., &
Tonoli, A. (2022). Implementation of a Field-Oriented
Control Strategy for Electromagnetic Shock Absorbers.
International Symposium on Electromobility (ISEM)
IEEE conference.
Hua, Y., Cai, Q., & Zhu, S. (2022). Energy-Regenerative
Semiactive Lateral Suspension Control in High-Speed
Trains Using Electromagnetic Damper Cum Energy
Harvester. IEEE Transactions on Vehicular
Technology, 71(5), 4801–4812.
Azam, A., Ahmed, A., Hayat, N., Ali, S., Khan, A.S.,
Murtaza, G. and Aslam, T. (2021). Design,
fabrication, modelling and analyses of a movable
speed bump-based mechanical energy harvester
(MEH) for application on road. Energy, 214,
p.118894.
Chen, K., Li, Z., Tai, W.-C., Wu, K., & Wang, Y. (2020).
MPC-based Vibration Control and Energy Harvesting
Using an Electromagnetic Vibration Absorber With
Inertia Nonlinearity. ArXiv (Cornell University).
Hamza, A., & Ben Yahia, N. (2020). Heavy trucks with
intelligent control of active suspension based on
artificial neural networks. Proceedings of the
Institution of Mechanical Engineers, Part I: Journal of
Systems and Control Engineering, 235(6),952–969.
Wang, Z., Zhang, T., Zhang, Z., Yuan, Y., & Liu, Y. (2020).
A high-efficiency regenerative shock absorber
considering twin ball screws transmissions for
application in range-extended electric vehicles. Energy
and Built Environment, 1(1), 36–49.
https://doi.org/10.1016/j.enbenv.2019.09.004
Casavola, A., Tedesco, F., & Vaglica, P. (2020). H 2 and
H ∞ Optimal Control Strategies for Energy Harvesting
by Regenerative Shock Absorbers in Cars
†. Vibration, 3(2), 99–115.
Kopylov, S., Chen, Z., & Abdelkareem, M. A. A. (2020).
Implementation of an Electromagnetic Regenerative
Tuned Mass Damper in a Vehicle Suspension
System. IEEE Access, 8, 110153–110163.
Xie, L., Cai, S., Huang, G., Huang, L., Li, J. and Li, X.
(2020). On Energy Harvesting From a Vehicle
Damper. IEEE/ASME Transactions on chatronics,
25(1), pp.108–117.
Gillespie, T. D., Saied Taheri, Sandu, C., & Duprey, B. L.
(2021). Fundamentals of vehicle dynamics. Sae
International.
Donahue, M.D., & Hedrick, J.K. (2002). Implementation of
an Active Suspension, Preview Controller for Improved
Ride Comfort.
Demetgul, M., & Guney, I. (2017). Design of the Hybrid
Regenerative Shock Absorber and Energy Harvesting
from Linear Movement. Journal of Clean Energy
Technologies, 5(1), 81–84.
Zheng, P., Gao, J., Wang, R., Dong, J., & Diao Jincheng.
(2018). Review on the Research of Regenerative Shock
Absorber.
Hurtado, G., Romero, J.A,. and Carlos,S.(2016) Energy
Harvesting Simulator IEEE
Design of Regenerative Suspension System Using Spiral Drive Mechanism
149