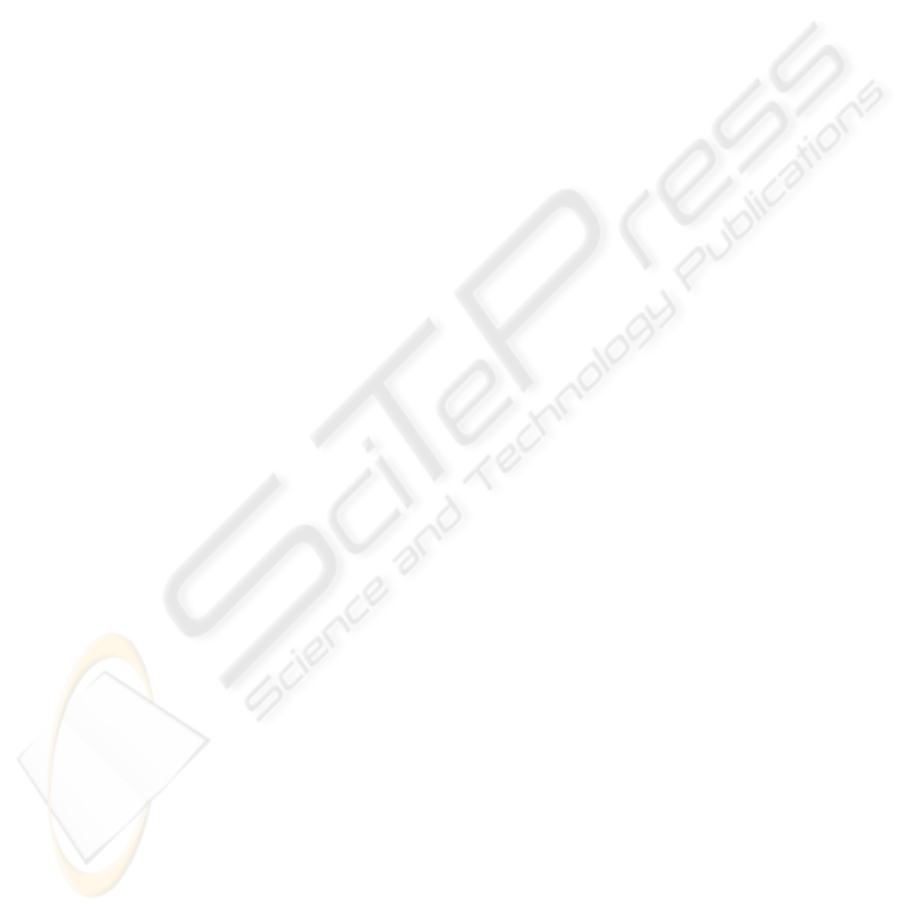
To avoid as much as possible temperature drifts of
the laser mirrors we should choose the length of the
resonator, where the signature is very poor. It means,
the laser operates on one chosen line in a wide range
of the resonator tuning.
Another application is a trace gas analyzer. Some
gases show a quite narrow dips in the absorption
spectrum. Choosing a suitable signature we can tune
the laser very easy to desired emission lines, which
can be absorbed by investigated gas medium. A
good example is a trace analyzer, where the spectral
line P14 of the carbon dioxide laser is desired in
combinations with P16, or P18, or P20 lines.
The picture of the laser histogram can be easy
modified using different isotopes of the carbon
or/and oxygen molecules like O
16
C
12
O
16
, O
16
C
13
O
16
,
O
16
C
12
O
18
, O
18
C
12
O
18
, O
18
C
13
O
18
, O
16
C
14
O
16
,
O
18
C
14
O
18
, O
16
C
13
O
19
, or O
17
C
12
O
17
. Then, different
signatures can be observed for the same length of the
laser resonator.
Another aspect of the experiment is to create an
expert system. As shown, stable and reproducible
signatures of the CO
2
laser can be a good standard to
calibrate servomechanisms used for investigations of
the laser histograms (series of signatures in line).
The servomechanism coupled with a given structure
of the laser can be applied for investigations of the
laser signatures in the large range of the laser tuning
independently of the laser medium. The adaptive
system to control the laser mirror is used for the
corrections of the mirror position errors. The system
searches the optimum voltage correction value, to
find the optimal position of the laser mirror. The
information about the optimum control is collected
for each investigated position of the step motor
(number of the pitches). Created in that way the data
base will be used in further investigations to develop
the expert system, which should be helpful for the
investigations of the laser histograms of different
lasers.
The automation of the described process can help
with searching suitable laser signatures for different
laser experiments, ex. very sophisticated signatures
for some heterodyning experiments (Buholz, 1981),
or well-ordered signatures (Plinski
2
, 2000).
The elaborated system for identification of the
laser lines can be used as a diffractive mechanism of
the laser marker, where the control of the lines
generated by a laser is obvious (Plinski
4
, 2000).
Reassuming, a carbon dioxide laser can be
designed as a chip spectral device, where choosing a
suitable operation frequency can be very easy
realized (comparing to expensive, and complicated
devices, where one of the laser mirrors is replaced
by a diffraction grating, which stimulates the laser
operation on a chosen line).
It is necessary to remark, that the results of the
investigations above are possible to obtain rather on
the laser in a single-mode operation regime. Then
only longitudinal modes are excited in the laser
cavity (Siegman, 1986). It is why an unstable
resonator is used, which stimulates a single-
frequency operation of the laser. In that way, high-
order transverse modes (disturbing the picture of the
signature) are suppressed by definition.
REFERENCES
Buholz, N. E., Selected five-color operation of a CO
2
laser. In Optical Engineering, Vol. 20, 1981, pp. 325-
327.
Mocker, H. W., Rotational level competition in CO
2
lasers. In IEEE Journal of Quantum Electronics, Vol.
QE-4, 1968, pp. 769-776.
Plinski
1
, E. F., Witkowski, J. S., Abramski, K. M.,
Algorithm of RF excited slab-waveguide laser design.
In Journal of Physics D: Applied Physics, Vol. 33,
2000, pp. 1-4.
Plinski
2
, E. F., Izworski, A., Witkowski, J. S., Calibration
of an automatic system using a laser signature. In
Journal of Systemics, Cybernetics and Informatics,
Vol. 1, No. 2, 2003 (Ed. International Institute of
Informatics and Systemics).
Plinski
3
, E. F., Witkowski, J. S., Well-ordered laser
signature. In Optics Communications, Vol. 176, No.
1,2,3, 2000, pp. 207-211.
Plinski
4
, E. F., Witkowski, J. S., Abramski, K. M.,
Diffractive mechanism for laser marker. In Optics and
Laser Technology, Vol. 32, 2000, pp. 33-37.
Shiffner, G., Prediction of CO
2
laser signatures. In IEEE
Journal of Quantum Electronics, Vol. QE-8, 1972, pp.
877-881.
Siegman, A. E., Lasers, Mill Valley, University Science
Books, California, 1986
Solnik W., Zajda Z., Automation of oxygenation process
in biological treatment plants, in Datorzinate 2000,
ser. 5, Riga, Rigas Teh. Univ. Zinat. Raksti,
2000, 12-17.
Waksberg, A. L., Boag, J. C., Sizgoric, S., Signature
variations with mirror separation for small sealed CO
2
lasers. In IEEE Journal of Quantum Electronics, Vol.
QE-7, 1971, pp. 29-35.
Witteman, W. J., The CO
2
laser, Springer Series in Optical
Sciences, Berlin, New York, 1987.
ICINCO 2004 - SIGNAL PROCESSING, SYSTEMS MODELING AND CONTROL
10