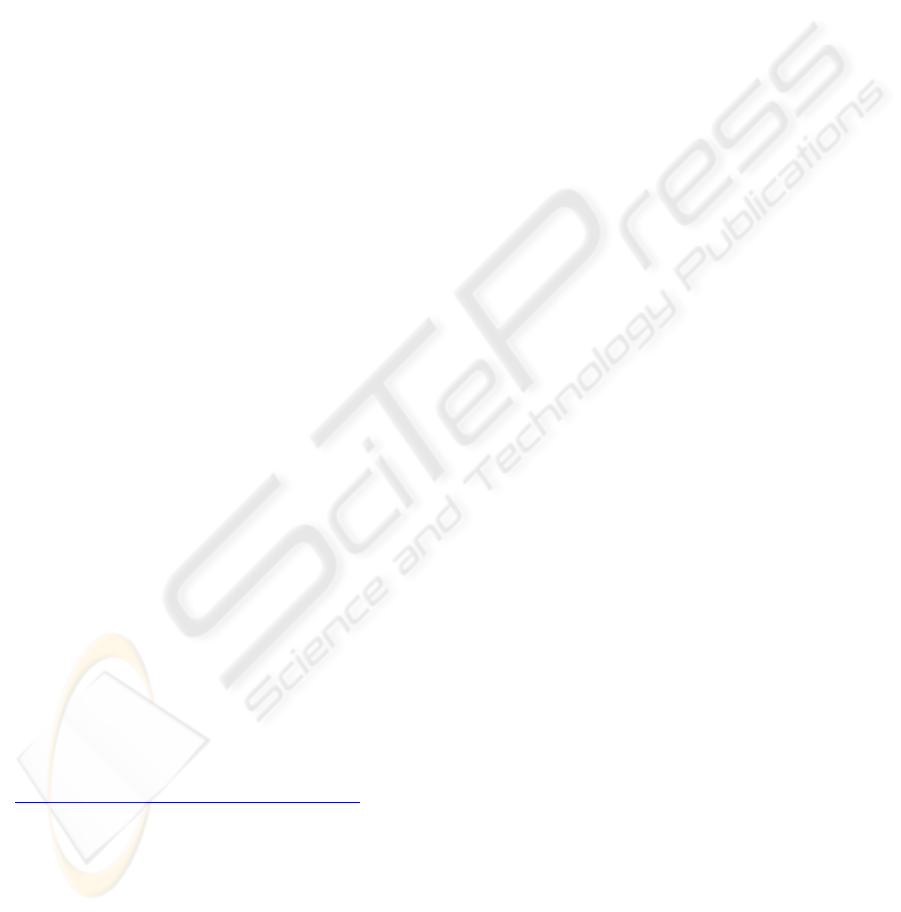
5 CONCLUSION
This work has direct benefits to corporate
management. The analytical framework could
enable executives to work with concrete criteria
when comparing their organization with others. The
assessment could serve as the starting point for
development of an implementation process that
would be adapted to the specific planning and
control needs of an SME. The SME is well known
for its flexibility and adaptability in the face of
operational and technological changes, and SMEs
are increasingly the site of complex and cutting-edge
manufacturing systems. The firms are looking to
integrate these systems in order to improve
performance. It is still uncertain, however, if SMEs
have the will or even the capacity to formalize
business processes. This would be a critical asset if
the firm decides to undertake the implementation of
an integrated management system. If an ERP
system is to deliver all the benefits promised by its
vendor, the new technologies must fully integrate all
corporate functions.
REFERENCES
Banker, R. D., Janakiraman, S.N., Donstans, C., Slaughter,
S.A. (2000). “Determinants of ERP adoption: an
empirical analysis,” AIM, University of Texas.
Bingi, P., Sharma, M.K., Godla, J. (1999). “Critical issues
affecting an ERP implementation,” Information
Systems Management, 16 (3) 7-14.
Chen, I.J. (2001). “Planning for ERP systems: analysis and
future trends,” Business Process Management Journal,
7 (5) 374-386.
Holland, C., Light, B., Gibson, N. (1999). “A Critical
Success Factors Model for Enterprise Resources
Planning Implementation,” 7th European Conference
on Information Systems, Copenhagen, 273-287.
Julien, P.A. et al. (1997). Les PME: Bilan et Perspectives,
(2nd Revised Edition), Cap-Rouge, Les Presses Inter
Universitaires.
Konicki, S. (2001). “Nike just didn’t do it right, says I2
technologies,” Information Week,
http://www.informationweek.com/827/nike.htm,
(March 5).
Lawrence, P.R., Lorsch, J.W., Organization and
Environment, Richard D. Irwin Inc, 1969.
Markus, L., Tanis, C. (2000). Framing the domains of IT
management, projecting the future… through the past,
Chap. 10, The Enterprise System Experience from
Adoption to Success, Editor Robert W Zmud, Michael
F. Price Chair in MIS, University of Oklahoma, 173-
207.
Nah, F.F-H, Lau, J. L-S. (2001), “Critical factors for
successful implementaion of enterprise systems,”
Business Process Management Journal, 7 (3) 285-296.
Palaniswamy, R., Frank T. (2000). “Enhancing
manufacturing performance with ERP sytems,”
Information Systems Management (Summer) 43-69.
Raymond, L., Blili, S. (1997). “Adopting EDI in a
Network Organization: The Case of Subcontracting
SMEs,” European Journal of Purchasing and Supply
Management, 3 (3) 165-175.
Raymond, L., Julien, P.A., Carrière, J.B., Lachance, R.
(1996). “Managing technological change in
manufacturing SMEs: a multiple case analysis,”
International Journal of Technology Management,
11(3-4) 270-285.
Raymond, L., Rivard, S., Jutras, D., “Évaluation du
potentiel d'adoption de l'ERP dans les PME,” Cahier
de la chaire de gestion stratégique des technologies de
l’information, HEC Montreal, June 2003.
Raymond, L. and St-Pierre, J. “Performance Effects of
Commercial Dependency for Manufacturing SMEs,”
International Business Trends: Contemporary
Business Readings, D.L. Moore and S. Fullerton
(Ed.), National Meeting of the Academy of Business
Administration, Key West, Florida, 2002, 133-142.
Roy, V. and Aubert, B.A. (2000). “A Resource-Based
View of the Information Systems Sourcing Mode”,
Cahier du GreSI, No. 99-08, HEC-Montréal.
Somers, T., Nelson, K. (2001). “The Impact of Critical
Success Factors Across the Stages of Enterprises
Resources Planning Implementations,” Proceedings of
the 34th Hawaii International Conference on System
Sciences.
Songini, M.L. (2002). “GM locomotive unit put ERP
rollout back on track,” Computer World, (February
11).
ICEIS 2004 - INFORMATION SYSTEMS ANALYSIS AND SPECIFICATION
618