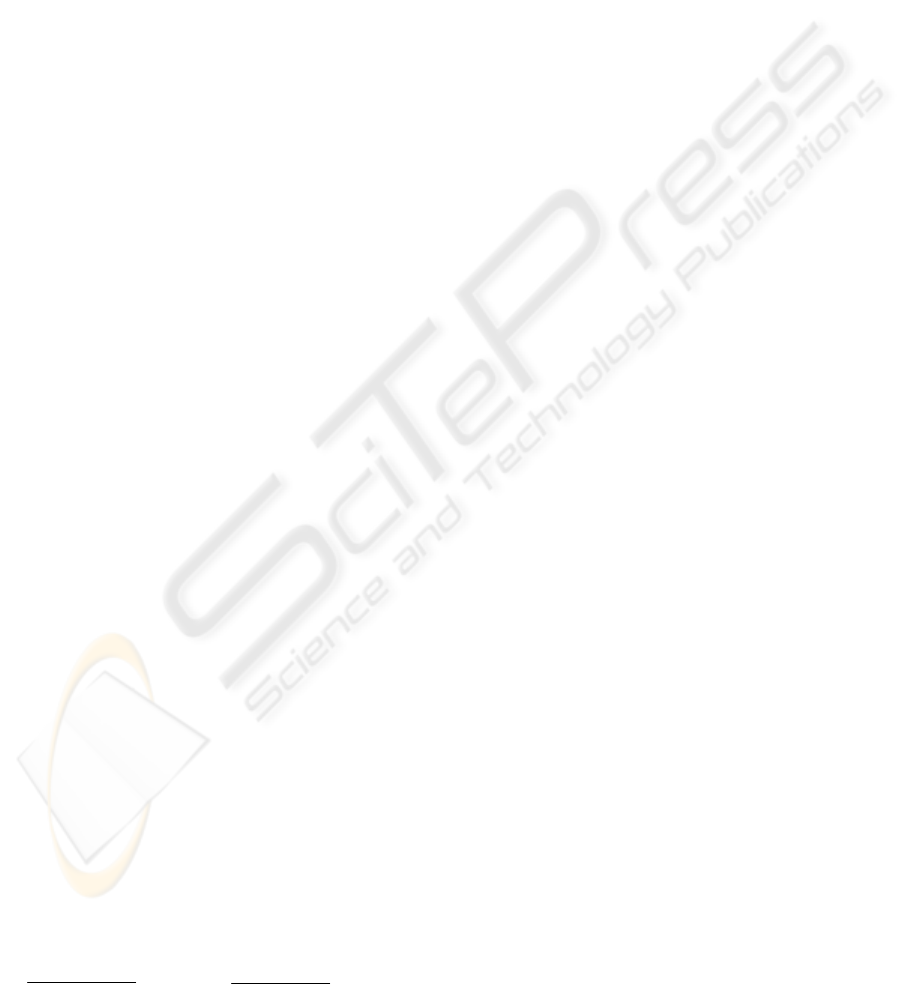
distributed fuzzy controllers, in a way that improves
certain performance measures without causing a
dramatic change in the control architecture. The
overall scheduling approach remains modular since
the production control modules are not modified but
tuned by the additional supervisory controller.
In the supervisory scheduling scheme it is
assumed that the demand and the cumulative
production are known. This is important for the
production surplus monitoring and control and for
scheduling decisions based on production surplus.
The expert knowledge that describes the supervisory
control objective builds on the assumption that
adaptive surplus bounds may improve the
production systems performance and can be
summarized in the following statements:
If the upper surplus bound is reduced there is an
immediate reduction of WIP.
If the upper surplus bound is increased there is
an increase of WIP and the total production rate
leading to a small reduction of backlog.
If the lower surplus bound is increased a
substantial reduction of backlog and an increase in
WIP is achieved.
If there is a reduction of lower surplus bound as
a result we have a deterioration of backlog with an
improvement of WIP.
Surplus bounds are decided by the output of IF-
THEN rules of the following form:
IF mx
e
is LMX
(k)
AND e
x
is LE
x
(k)
AND e
w
is
LE
w
(k)
THEN u
c
is LU
c
(k)
AND l
c
is LL
c
(k)
,
where, k is the rule number, mx
e
is the mean surplus
of the end product, LMX is a linguistic value of the
mx
e
with term set MX= {Negative Big, Negative
Small, Zero, Positive Small, Positive Big}, e
x
is the
error of end product surplus (the difference between
surplus x
e
and the lower bound of surplus), with
linguistic value term set E
x
= {Negative, Zero,
Positive}. The relative deviation of WIP is denoted
e
w
and LE
w
is the linguistic value chosen from the
term set E
w
= {Negative, Zero, Positive}. The upper
surplus bound correction factor u
c
takes linguistic
values LU
c
from U
c
= {Negative, Negative Zero,
Zero, Positive Zero, Positive} and the lower surplus
bound correction factor l
c
takes linguistic values LL
c
from the term set L
c
= {Negative, Negative Zero,
Zero, Positive Zero, Positive}.
The crisp arithmetic values,
*
c
u
and
*
c
l
, of the
corrections of the upper and lower surplus bounds,
respectively, are given by the following
defuzzification formulas:
∑
∑
⋅
=
)(
)(
*
*
*
cU
cUc
c
u
uu
u
c
c
µ
µ
, (5a)
∑
∑
⋅
=
)(
)(
*
*
*
cl
cLc
c
u
ll
l
c
c
µ
µ
, (5b) (5a) (5a)
where
)(
*
cU
u
c
µ
and
)(
*
cL
l
c
µ
are the MFs of the upper
and lower surplus bounds, respectively. These MFs
represent the aggregated outcome of the fuzzy
inference procedure. The correct selection of input
and output membership functions characterizes the
performance of the overall scheduling task.
Since the form of the fuzzy rules of both the
distributed and supervised approach for fuzzy
scheduling have been identified, a crucial point is
the selection of the MFs. The correct choice of the
MFs is by no means trivial but plays a crucial role in
the success of an application. Consequently, the
selection of MFs if not based on a systematic
optimization procedure cannot guarantee minimum
WIP level. This is the main drawback of the
heuristic selection of MFs in case of known (or
almost known) demand patterns. The evolutionary
algorithm developed and explained in the next
section, creates MFs that fit best to scheduling
objectives. In this context, the design of the fuzzy
controllers (distributed or supervisory) can be
regarded as an optimization problem in which the set
of possible MFs constitutes the search space.
3 EVOLUTIONARY FUZZY
SCHEDULING
The use of evolving genetic structures for the
production scheduling problem, has recently gained
a lot of acceptance for the automated and optimal
design of fuzzy logic systems (Tedford et al, 2001).
Here, we consider the application of an evolutionary
algorithm for the optimal selection of MFs.
The MF defined in the previous paragraphs are
used to construct the chromosome. The basic idea is
to represent the complete set of MFs by an
individual (chromosome) and to evolve shape and
location of the MFs. This is shown in Figure 1 for
the case of trapezoidal and triangular MFs. An initial
population is derived from the first chromosome by
repeated application of the mutation operator. The
objective is to optimize a performance measure
which in the EAs context is called fitness function.
In each generation, the fitness of every chromosome
is first evaluated based on the performance of the
production network system which is controlled
through the membership functions represented in the
chromosome. A specified percentage of the better
fitted chromosomes, is retained for next generation.
Parents are selected repeatedly from the current
chromosomes generation, and new chromosomes are
generated from the parents. One generation ends
when the number of chromosomes for the next
ICINCO 2005 - INTELLIGENT CONTROL SYSTEMS AND OPTIMIZATION
198