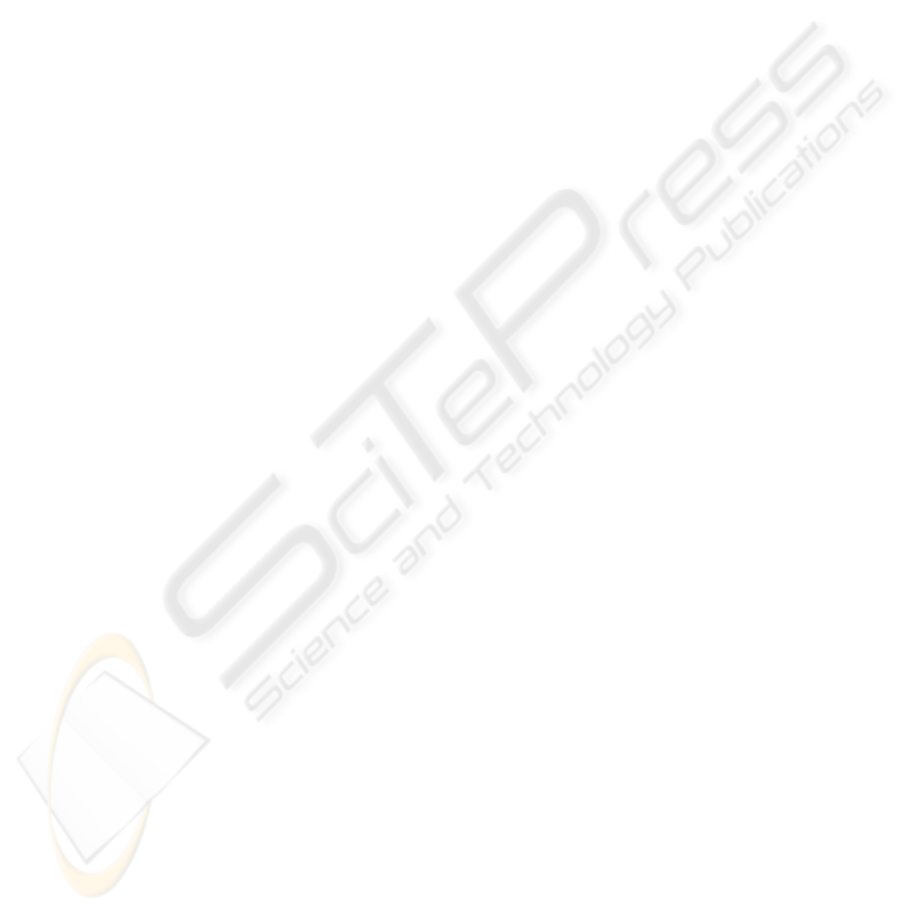
understanding the right shape of velocity table curve
during the software development. The user was
forced to experience the same brake activation
response for the whole walk. In that way the step
time and step percentage profile were forced to be
tightly constant. The user was so forced to walk at
fixed velocity. The user was helped in do this by
walking on a tapis roulant so that he could slightly
feel the unnatural step regulation. The amount of
tests was collected varying walking velocity and
brake activation position.
5 CONCLUSIONS
A final prosthesis prototype is the result of a long
design process. Experience and skills are supported
now by coded methodologies and analysis tool. This
process starts from a design approach leading
towards details optimization. It’s important to
underline the methodology contribution to several
re-engineering stages. By means of final release a
large development in direct signal acquisition and
testing became possible. The proposed methodology
for step analysis was done with the constant help and
experience supply of patients and INAIL staff. The
presented methodology is basic for the further FSM
development with self-learning and adaptive
features.
REFERENCES
Dornig A., Le molle, CLUP 1973
Canina M., Vicentini F., Rovetta A., Innovative Design,
Development And Prototyping Of Knee Prosthesis, in
Proceedings of ROBTEP 2004, Automation – Robotics
in theory and practice, 2004
Canina M., Vicentini F., Rovetta A., Innovative Wide
Sensors Integration for Smart Bio-robotic Prosthesis
Control , in Proceedings of RAAD’04, 13th
International Workshop on Robotics , 2004
AAVV, Otto Bock Manuale Protesi, Protesi per arto
inferiore - SCHIELE & SCHON 1988
AAVV, Biomechanics of the musculo-skeletal system (II
edition) – Wiley 1999
Nam P. Suh, The principles of Design – Oxford University
Press 1990
Kapandji, Fisiologia articolare – Soc Editrice DEMI-
Roma 1974
AAVV, Ausili e ortesi in medicina, Vol. 3 – Editrice
Ricerca Medica (Na) 1998
Rovetta A., Canina M., Campa G., Della Santina S.,
Biorobotic design criteria for Innovative Limb
Prosthesis, 9th International Symposium on
Intelligent Robotic Systems, SIRS’2001, Toulouse,
France, 18-20 July 2001
Rovetta A., Canina M., Allara P., Campa G., Della
Santina S., Biorobotic design criteria for Innovative
Limb Prosthesis, Icar 2001, International Conference
on Advanced Robotics, Budapest, 22-26 August 2001
Rovetta, M.Canina, P. Allara, G. Campa, S. Della
Santina, “Biorobotic design criteria for Innovative
Limb Prosthesis”, Mechanika – 2001, Proceedings of
the International Conference, Kaunas, Lituania, April
2001
M. Canina, G. Verni, P. Valentini, Gamba “intelligente”
cambia il passo secondo il terreno, in La Repubblica
Salute anno 7 n. 286, 20 settembre 2001
Hugh Herr, “ Presentation highlights: Prosthetic and
orthotic limbs”, J. Rehabilitation Res.& Dev. Vol. 39
N° 3 (supplement) pp11-12, 2002
D. Zlatnik, “Intelligently controlled above knee
prosthesis,” the 4
th
Int. conf. on motion and vibration
control.
J. H. Kim, J. H. Oh, 2001, “ Development of an above
knee prosthesis using MR damper and leg simulator,”
Proc. Conf. Rob. Aut., Seoul, 1998
J. Slavica, J. Tamara, G. Vladimir, P. Dejan, “Three
machine learning techniques for automatic
determination of rules to control locomotion,” IEEE
Trans. Biomedical Eng., Vol. 46, N°3, pp 300-310,
1999
M. S. Ju, Y. F. Yang and T.C. Hsuch, “Development of
actively controlled electro-hydraulic above-knee
prosthesis,” Proc. Romansy 10/ the 10
th
CISM-
IFToMM symposium, theory and practice of robots
and manipulators, Spring-Verlag Ed., pp 367-372,
1995
M. Canina et all., “Innovative system for the accumulation
of energy of the step in a limb prosthesis,” accepted at
11
th
World Cong. Mech. Mach. Science, August 18-
21, 2003, China.
B. M. Nigg, W. Herzog, 1999, “Biomechanics of the
musculo-skeletal system,” 2
nd
edition, John Wiley and
Sons, England.
D. A. Winter, “ Biomechanics and motor control of
human movement,” Wiley-Interscience Publication,
2
nd
edition, 1990
L. Peeraer et all., “ Development of EMG-based mode and
intent recognition algorithms for a computer-
controlled above-knee prosthesis,” J. Biomed. Eng.
vol. 12, May, pp178-182, 1990
D. Popovic & all., “ Optimal control for the active above
knee prosthesis,” J. biomed. Eng. Vol. 19, pp. 131-
150, 1991
A. Rovetta, X. Wen, “ Biorobotic in a new artificial leg,”
IEEE Int. Symp. on Int. Rob. and Manipulators,
Krakow, 1990
.
LOWER LIMB PROSTHESIS: FINAL PROTOTYPE RELEASE AND CONTROL SETTING METHODOLOGIES
241