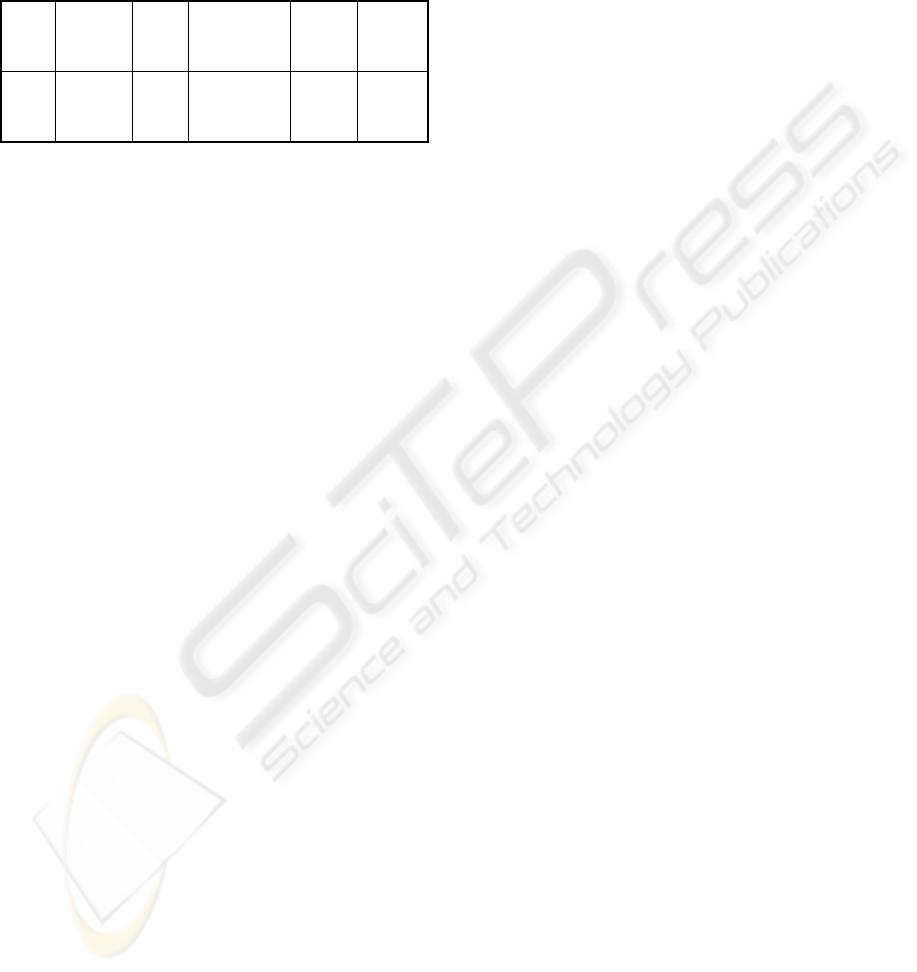
efficient system. While the dynamic system is much
more effective than foam, materials and installation
cost much more, and the time and maintenance
required for the pumping system is highly cost
ineffective due to electricity consumption.
Table 1: HAZOP table.
Guide
Word
Deviation Ln2
line
needs
to
stop?
Consequences Causes Suggest
ed
Action
More 120psi
Pressure
at PG1
No
need
Alarm will be
at 120 psi
VENTS
are off
no
handler
ON
Start
handler ,
check
VENT
There are four principal areas of hazard related to
the use of
Ln2. These are: flammability, high pressure gas,
materials, and personnel. All categories of hazard
are usually present in a system concurrently, and
must be considered when introducing a Ln2 system
or process The high pressure gas hazard is always
present when ln2 is used or stored. Since the
liquefied gases are usually stored at or near their
boiling point, there is always some gas present in the
container. The large expansion ratio from liquid to
gas provides a source for the build-up of high
pressures due to the evaporation of the liquid. The
rate of evaporation will vary, depending on the
characteristics of the fluid, container design,
insulating materials, and environmental conditions
of the atmosphere. Container capacity must include
an allowance for that portion which will be in the
gaseous state. These same factors must also be
considered in the design of transfer lines and piping
systems A very brief contact with ln2 at -195.8C
temperatures is capable of causing burns similar to
thermal burns from high temperature contacts.
Prolonged contact with these temperatures will
cause embitterment of the exposed members because
of the high water content of the human body. The
eyes are especially vulnerable to this type of
exposure, so that eye protection is necessary.
1.1 Designing Safety System for
Dynamic Vacuum Pipeline
The HAZOP study is done for Dynamic vacuum
pipeline system but it is done before installation of
pipeline. HAZOP: It is a hazard and operability
study. The Hazops procedure involves taking a full
description of a process and systematically
questioning every part of it to establish how
deviations from the design intent can arise. Once
identified, an assessment is made as to whether such
deviations and their consequences can have a
negative effect upon the safe and efficient operation
of the manufacturing plant. If considered necessary,
action is then taken to remedy the situation. This
study helps to design the safety system required for
Dynamic vacuum ln2 pipe line system. An essential
feature in this process of questioning and systematic
analysis is the use of keywords to focus the attention
of the team upon deviations and their possible
causes. These keywords are divided into two sub-
sets:
Primary Keywords which focus attention upon a
particular aspect of the design intent or an associated
process condition or parameter. Secondary
Keywords which, when combined with a primary
keyword, suggest possible deviations. The entire
technique of Hazops revolves around the effective
use of these keywords, so their meaning and use
must be clearly understood by the team. Examples of
often used keywords are listed below. Primary
words: Incase of Dynamic vacuum pipeline system
is Pressure, Vacuum, Temp, and Flow etc.
Secondary words: More, less, In the HAZOP study
we have to write a report on Purpose, Objective, and
Scope of study, Team members, and Data collection
by team members in following format. Showed in
Table 1.
But it has been observed that the users do not install
sufficient safety system while installation of
Dynamic vacuum pipeline system. For long term
success of Dynamic vacuum pipe line, it is very
clear that control over vacuum, and pressure are very
important. Usually, the manufacturers design
Dynamic vacuum pipeline system with many safety
release valves (SRV) to stop over pressurization.
Usually these valves are present at both sides of any
ln2 valve. Typically SRV operates at 120PSI,
170PSI as per requirement. But it is a one kind of
breakdown maintenance. It means, if the pressure
goes more than 120PSI the SRV fires. But one
important point is ignored and that it the firing of
SRV happens inside production floor. The ln2 gets
fired with smoky jet with loud cranking noise. It is
big disturbance to all operators around the line. It
also may decrease the percentage of O2 in
atmosphere. So, the operators need to go away from
work place causing production disturbance. Any
production disturbance can cost thousands of dollars.
So it is required to control the pressure with different
perspective. The Dynamic vacuum line should have
an additional safety system which should alarm on
over pressurization. The SRV is needed but that
should be the last choice. The control over vacuum
A SAFETY SYSTEM FOR DYNAMIC VACUUM LIQUID NITROGEN PIPELINE - For World Class Manufacturing
Operation in Semiconductor Industry
149