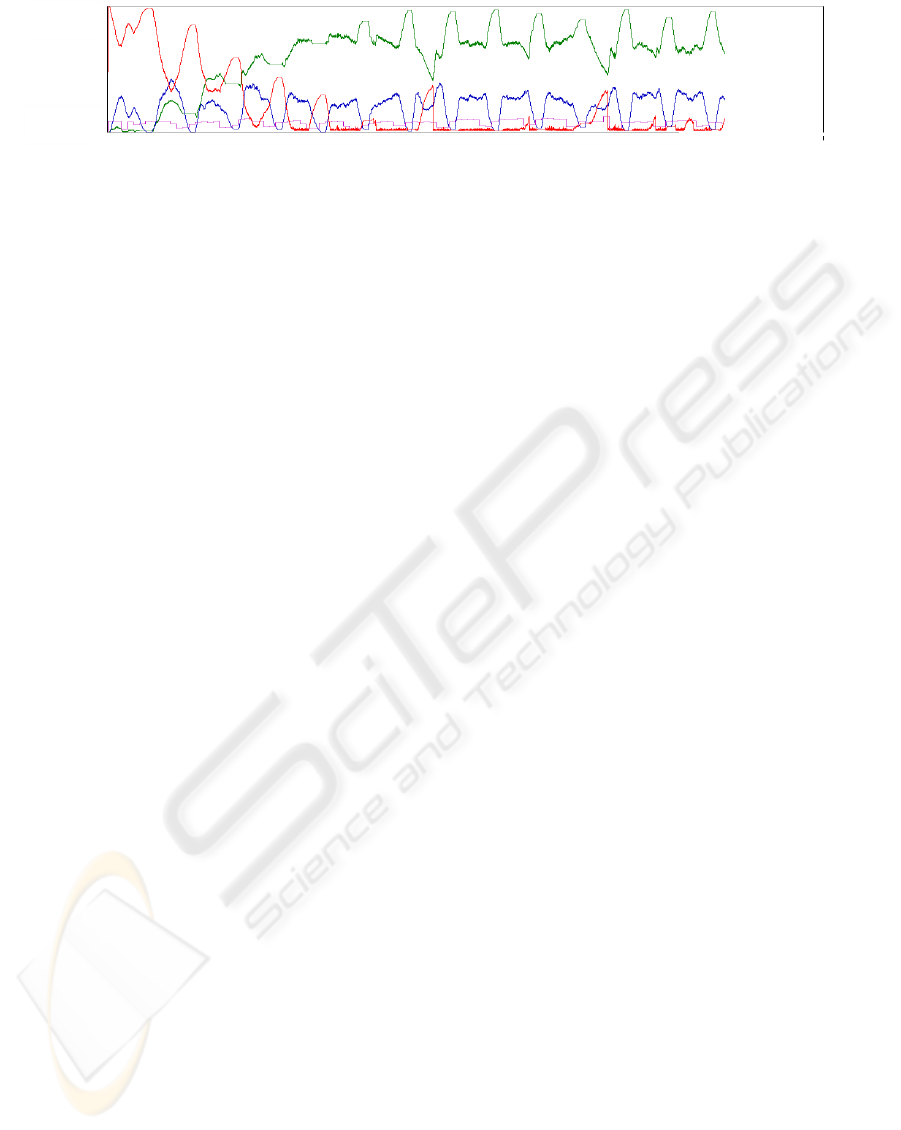
Figure 10: Example of time evolution of the carriers’ number in each waiting area.
0
600
Time
uantit
o
waitin
carriers
0
10000000.0
a flexible manufacturing system. The International
Journal of Flexible Manufacturing Systems, Vol.4,
pp.5-16.
Branislav, H., Mrafko, L., Bielko, V., 2002. A
compraison of the AGV control approaches unsing
Petri Nets. International conference on Systems,
Man and Cybernetics, Tunisia.
Breton, L., Maza, S., Castagna, P., 2006. A multi-agent
based conflict-free routing approach of bi-
directional automated guided vehicles. American
Control Conference, USA.
Castagna, P., Mebarki, N., Maza, S., 2004. Evaluation
du nombre d’AGVs sur un système de production
de type Job shop. 5ème Conférence Francophone
de Modélisation et SIMulation (MOSIM’04),
pp.619-626, France.
Collinot, A., Droguoul, A., 1996. La méthode de
conception multi-agent cassiopée: Application à la
robotique collective. Technical Report LAFORIA,
LIP6.
Egbelu, P.J., Tanchoco, J.M.A., 1984. Characterization
of automatic guided vehicle Dispatching rules.
International Journal of Production Research,
Vol.22, No.3, pp.359-374.
Egbelu, P.J., 1987. The use of non-simulation
approaches in estimating vehicle requirements in an
automated guided vehicle based transport systems.
Material flow, No.4, pp.209-221.
Gaskins, R.J., Tanchoco, J.M.A., 1987. Flow path
design for automated guided vehicle systems.
International Journal of Production Research,
Vol.27, No.6, pp.915-926.
Krishnamurthy, N.N., Batta, R., Karwan, H., 1993.
Developing conflict-free routes for automated
guided vehicles. Operations Research, 41(6),
pp.1077-1090.
Kim, C.W., Tanchoco, J.M.A., 1991. Conflict-free
shortest-time bi-directional AGV routing.
International Journal of Production Research,
Vol.29, No.12, pp.2377-2391.
Lawley, M., Reveliotis, S., Ferreira, P., 1999. Design
guidelines for deadlock handling strategies in
flexible manufacturing systems. International
Journal of Manufacturing Systems, Vol.9, pp.5-30.
Maza, S., Castagna, P., 2001. Conflict-free AGV
routing in bi-directional networks. 8th IEEE
International conference on Emerging Technologies
and Factory Automation, pp.761-764, France.
Maza, S., Castagna, P., 2005a. A performance-based
structural control policy for conflict-free routing of
bi-directional Automated Guided Vehicles.
Computers in industry, Elsevier publication,
Vol.56, n°7, pp.719-733.
Maza, S., Castagna, P., 2005b. Sequence-based
hierarchical conflict-free routing strategy of bi-
directional automated guided vehicles. 16th IFAC
World Congress, Praha.
Oboth, C., Batta, R., Karwan, M., 1999. Dynamic
conflict-free routing of automated guided vehicles.
International Journal of Production Research,
Vol.37, No.9, pp.2003-2030.
Pia Fanti, M., Maione, B., Mascolo, S., Turchiano, B.,
1997. Event-based feedback control for deadlock
avoidance in flexible production systems. IEEE
Transactions on Robotics and Automation, Vol.13,
No.3, pp.347-363.
Reveliotis, S.A., Conflict resolution in AGV systems.
IIE Transactions, Vol.32, No.7, pp.647-659.
Reveliotis, S.A., Ferreira, P., 1996. Deadlocks
avoidance policies for automated manufacturing
cells. IEEE Transactions on Robotics and
Automation, Vol.12, No.3, pp.845-857.
Silberschatz, A., Peterson, J.L., 1991. Operating system
concepts, Addison Wesley.
Taghaboni, F., Tanchoco, J. M. A., 1995. Comparison of
Dynamic Routing
Techniques for Automated Guided Vehicle Systems.
International Journal of Production Research, Vol.10,
No.33, 2653-2669.
Tanchoco, J.M.A., Egbelu, P.J., 1986. Potentials for bi-
directional guide-path for automated guided vehicle
based systems. International Journal of Production
Research, Vol.24, No.5, pp.1075-1097.
ON THE USE OF AUTOMATED GUIDED VEHICLES IN FLEXIBLE MANUFACTURING SYSTEMS
483