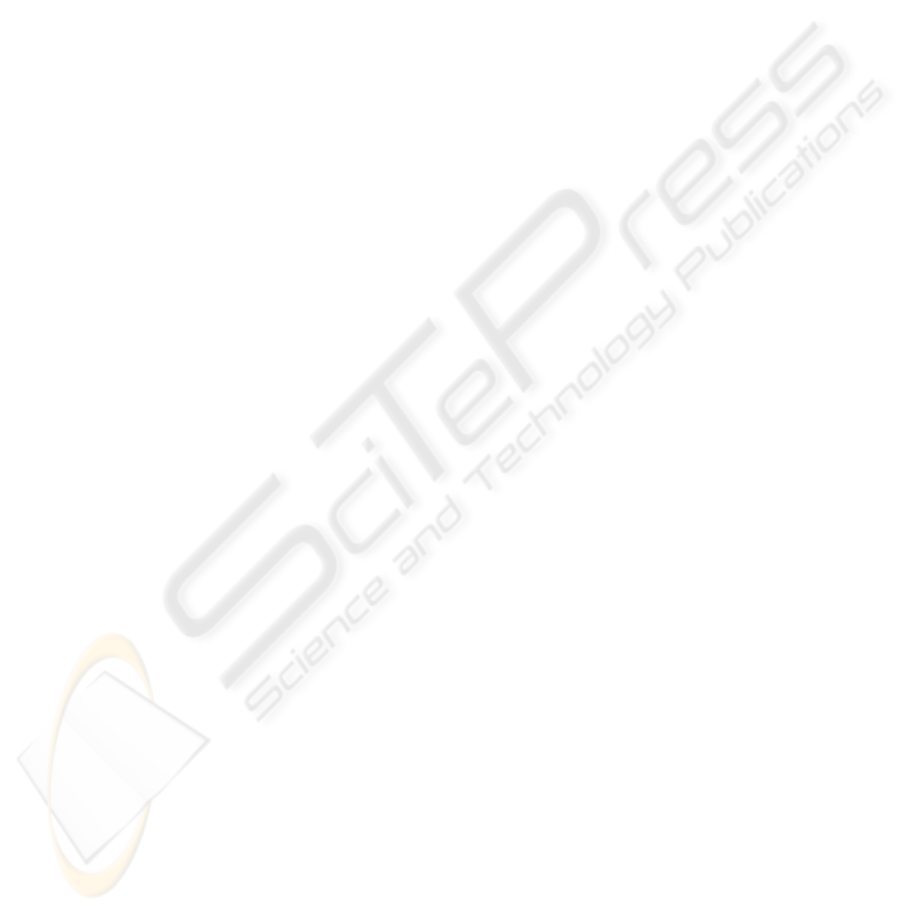
which corresponds to the measurement accuracy. On
the other hand, further adjusting of the model to the
new experimental data does not give the residual
reduction.
Hence, the calibration results confirm validity of
the proposed identification technique and its ability
to tune the joint offsets and link lengths from
observations of the leg parallelism. Other conclusion
is related to the modelling assumption: for further
accuracy improvement it is prudent to generalize the
manipulator model by including parameters
describing the orientation of the prismatic joint axes,
i.e. relaxing assumption (iv) (see sub-section 2.2).
5 CONCLUSIONS
This paper proposes further developments for a
novel calibration approach for parallel manipulators,
which is based on observations of manipulator leg
parallelism with respect to some predefined planes.
This technique employs a simple and low-cost
measuring system composed of standard comparator
indicators, which are sequentially used for
measuring the deviation of the relevant leg location
while the manipulator moves the TCP along the
Cartesian axes. From the measured differences, the
calibration algorithm estimates the joint offsets and
the link lengths that are treated as the most essential
parameters to be tuned. The validity of the proposed
approach and efficiency of the developed numerical
algorithm were confirmed by the calibration
experiments with the Orthoglide prototype, which
allowed essential reduction of the residuals and
corresponding improvement of the accuracy.
Future work will focus on the expanding the set of
the identified model parameters, their identifiably
analysis, and compensation of the non-geometric
errors.
REFERENCES
Chablat, D., Wenger, Ph., 2003. Architecture Optimization
of a 3-DOF Parallel Mechanism for Machining
Applications, the Orthoglide. IEEE Transactions On
Robotics and Automation, Vol. 19 (3), pp. 403-410.
Daney, D., 2003. Kinematic Calibration of the Gough
platform. Robotica, 21(6), pp. 677-690.
Huang, T., Chetwynd, D.G. Whitehouse, D.J., Wang, J.,
2005. A general and novel approach for parameter
identification of 6-dof parallel kinematic machines.
Mechanism and Machine Theory, Vol. 40 (2), pp. 219-
239.
Innocenti, C., 1995. Algorithms for kinematic calibration
of fully-parallel manipulators. In: Computational
Kinematics, Kluwer Academic Publishers, pp. 241-
250.
Iurascu, C.C. Park, F.C., 2003. Geometric algorithm for
kinematic calibration of robots containing closed
loops. ASME Journal of Mechanical Design, Vol.
125(1), pp. 23-32.
Jeong J., Kang, D., Cho, Y.M., Kim, J., 2004. Kinematic
calibration of redundantly actuated parallel
mechanisms. ASME Journal of Mechanical Design,
Vol. 126 (2), pp. 307-318.
Merlet, J.-P., 2000. Parallel Robots, Kluwer Academic
Publishers, Dordrecht, 2000.
Pashkevich, A., Wenger, P., Chablat, D., 2005. Design
Strategies for the Geometric Synthesis of Orthoglide-
type Mechanisms. Mechanism and Machine Theory,
Vol. 40 (8), pp. 907-930.
Pashkevich A., Chablat D., Wenger P., 2006. Kinematic
Calibration of Orthoglide-Type Mechanisms.
Proceedings of IFAC Symposium on Information
Control Problems in Manufacturing (INCOM’2006),
Saint Etienne, France, 17-19 May, 2006, p. 151 - 156
Renaud, P., Andreff, N., Pierrot, F., Martinet, P., 2004.
Combining end-effector and legs observation for
kinematic calibration of parallel mechanisms. IEEE
International Conference on Robotics and Automation
(ICRA’2004), New-Orleans, USA, pp. 4116-4121.
Renaud, P., Andreff, N., Martinet, P., Gogu, G., 2005.
Kinematic calibration of parallel mechanisms: a novel
approach using legs observation. IEEE Transactions
on Robotics and Automation, 21 (4), pp. 529-538.
Tlusty, J., Ziegert, J.C., Ridgeway, S., 1999. Fundamental
Comparison of the Use of Serial and Parallel
Kinematics for Machine Tools. CIRP Annals, Vol. 48
(1), pp. 351-356.
Wang, J. Masory, O. 1993. On the accuracy of a Stewart
platform - Part I: The effect of manufacturing
tolerances. IEEE International Conference on
Robotics and Automation (ICRA’93), Atlanta,
Georgia, pp. 114–120.
Wenger, P., Gosselin, C., Chablat, D., 2001. Comparative
study of parallel kinematic architectures for machining
applications. In: Workshop on Computational
Kinematics, Seoul, Korea, pp. 249-258.
Wenger, P., Gosselin, C. Maille, B., 1999. A comparative
study of serial and parallel mechanism topologies for
machine tools. In: Proceedings of PKM’99, Milan,
Italy, pp. 23–32.
CALIBRATION OF QUASI-ISOTROPIC PARALLEL KINEMATIC MACHINES: ORTHOGLIDE
91