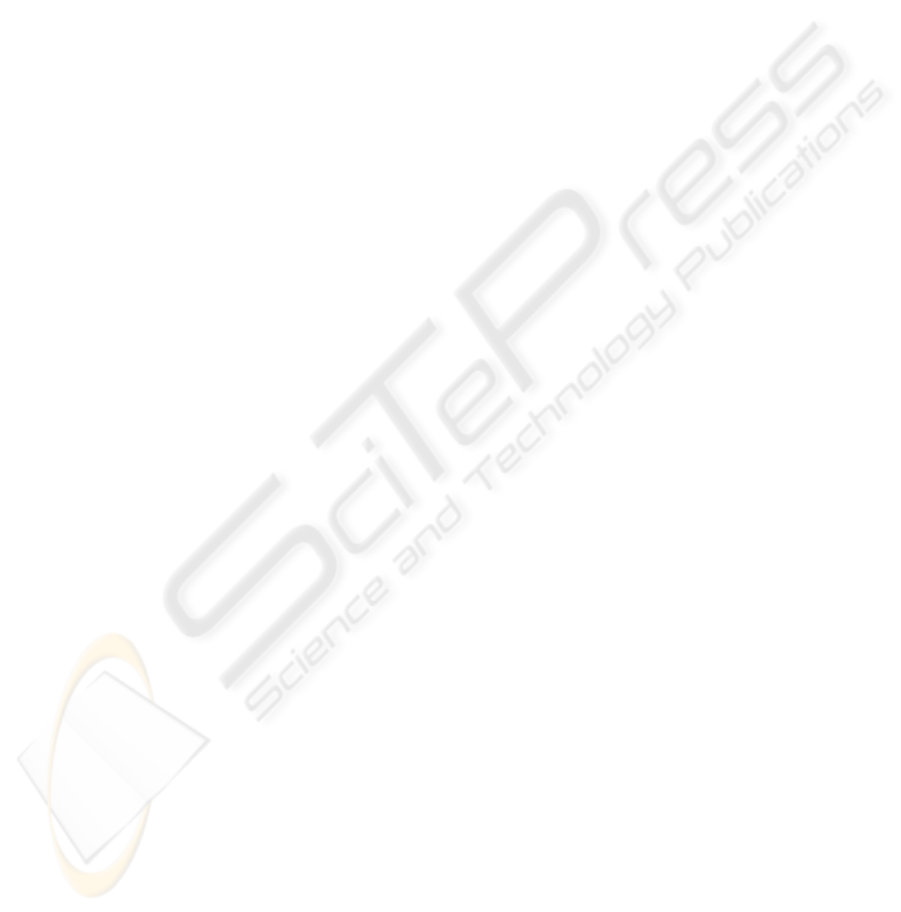
4. Bansal, R.: Coming Soon to a Wal-Mart Near You. IEEE Antennas and Propagation
Magazine, 45, 6, 2003, pp 105-106
5. Roberti, M. “Wal-Mart Spells Out RFID Vision,” RFID Journal, June 16, 2003. Available
on the Internet at 09.182.51.148/article/articleview/211?Redirect=/article/articleview/463
6. Vollmer, D.: RFID: From Compliance to Competitive Advantage. Presentation, RedPrairie
Corp., Dallas, TX, 2004.
7. Michael, K., McCathie, L.: The Pros and Cons of RFID in Supply Chain Management, IEE
Proceedings of the International Conference on Mobile Business (ICMB’05)
8. Organisation for Economic Co-operation and Development (OECD): Radio-Frequency
Identification (RFID): Drivers, Challenges and Public Policy Considerations, 2006
9. Garfinkel, S. and Holtzman, H.: Understanding RFID Technology”, 1st ed., pp. 15-22,
Addison Wesley Professional, 2005
10. Hassan, T., and Chatterjee, S.:A Taxonomy for RFID”, Proceedings of the 39th Hawaii
International Conference on Systems Science, Kauai, HI, January 2006, IEEE Computer
Society Press, Los Alamitos, CA, 2006
11. Federal Trade Commission: Radio Frequency IDentification: Applications and Implications
for Consumers, 2005
12. Bhuptani, M. & Moradpour, S.: RFID Field Guide Deploying Radio Frequency Identifica-
tion. New York, New York: Prentice Hall.
13. Craft, B.A., “Secure Integration of Radio Frequency Identification of Radio Frequency
Identification (RFID) Technology into a Supply Chain, 2005, Thesis
14. Symbol Technologies: Understanding the Key Issues in Radio Frequency Identification
(RFID). White Paper Retrieved at http://www.symbol.com/products/whitepapers/rfid_key
_issues.html
15. Lewis, S.: A Basic Introduction to RFID Technology and its use in the Supply Chain, 2004,
White Paper: LaranRFID
16. Finkenzeller, K, RFID Handbook: Fundamentals and applications in contactless smart
cards and identification, 2nd Edition, John Wiley & Sons Ltd, 2003
17. Jong, E., Hil, M., Nederpelt, M., VandenBerghe, J., Köster, J.: Making Waves: RFID
Adoption in Returnable Packaging, RFID Benchmark Study, 2003
18. Weinstein, R.: RFID: A Technical Overview and its application to the Enterprise, IEEE
Computer Society, 2005
19. Blue, L., Powell, K.: EPC and Radio Frequency Identification (RFID) Standards. Matrics,
2004
20. RFIDJournal.: A Summary of RFID Standards, 2004. Retrieved at
http://www.rfidjournal.com/article/articleprint/1335/-1/1
21. RFID Standards (n.d). Retrieved February 19, 2007 from http://www.scansource.com/
europe/upload/RFID_Standards.pdf
22. Data System International: Understanding RFID Compliance Standards, 2004. White Paper
23. EPCglobal: The Pace of EPC/RFID Adoption Continues to Accelerate, 2006. Retrieved at
www.epcglobalinc.org/about/media_centre/press_rel/EPCglobal_Inc_1000th_sub_press_release.pdf
24. Department of Defense.: Defense Acquisition Regulations System. Retrieved at
http://a257.g.akamaitech.net/7/257/2422/01jan20071800/edocket.access.gpo.gov/2007/E7-
2209.htm
25. US Department of Commerce.: Radio Frequency Identification – Opportunities and Chal-
lenges in Implementation, 2005 Washington, April– www.technology.gov/reports
26. Waktola, E.: EPC Mandates, Momentum and Milestones in the Retail Supply Chain. Re-
trieved at http://www.logisticsit.com/absolutenm/templates/article-datacapture.aspx?arspx?
articleid=2048&zoneid=14
27. Gerst, M., Bunduchi, R., Graham: Current issues in RFID standardization, 2004, Unpub-
lished
28. Roberti, M.: RFID Vendors to Launch Patent Pool, 2005. RFIDJournal
59