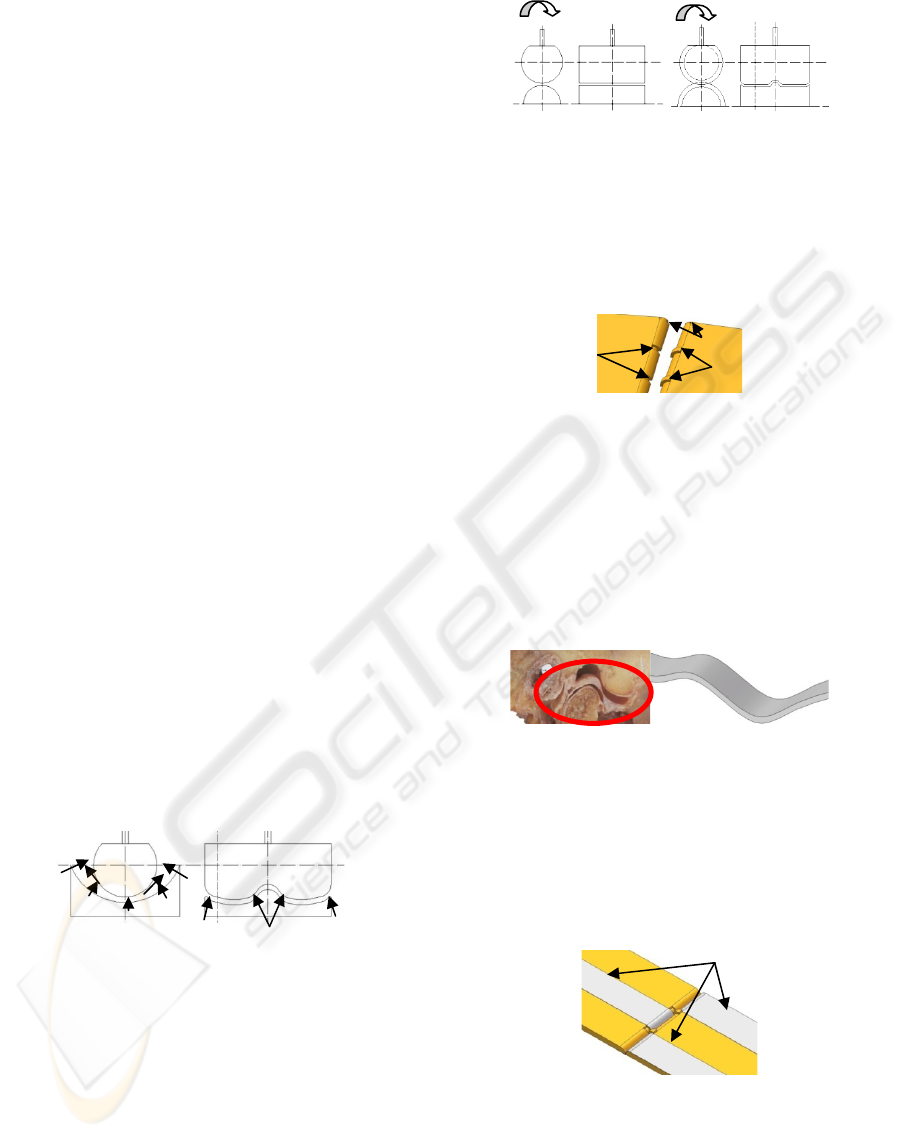
The ligaments are the driver of body structures.
Usually, one arthrosis connects with one more
ligaments. When the arthrosis move, the ligaments
around it will cooperated drive the arthrosis to move
with a non-repeated track.
3 DESIGN OF THE BIAXIAL
JOINT
3.1 The Essentials of the Joint Design
In this project, a bionic joint would be designed for
the joint of electronic devices. Therefore some
essentials of the main joint design as follow:
While design joints the rolling friction should be
selected for decreasing the affect of friction.
Usually the wire is easily failed when folded
repeatedly. So the wire should cling on the joint
surface to acquire the support. Also the curvature
radius of joint should be enlarged at full steam.
As articular discs, some filling would be
accepted and it can make joint surfaces fit further
with each other, increase stability of joints and
absorb the large forces of compression and shear.
Imitate the body drivers, some special drivers
should be selected with the small structure and for
parallel movement.
3.2 The Surfaces Design of Joint
In body, the hinge joint has two parts, concave and
convex, and movement takes place on sagittal plane,
e.g., the elbow and ankle. With the analysis on the
structures of hinge joint, it is described as Figure 2.
Figure 2: The sketch of hinge joint. The N means the
support forces, f is the frictions, F is the transverse forces.
For avoiding the friction, the concave part will be
replaced by convex, and the two parts are tangent.
See Figure 3 (a). Transverse displacement should
also be considered. Simulate the cooperation of the
neck and convexity, some keys and slots should be
designed. So the joint is showed as Figure 3 (b).
(a) (b)
Figure 3: The sketch of joint.(a) joint with double convex,
(b) joint with key and slot.
As the analysis before, the curvature radius should
be enlarged. So the section of the joint part can be
designed as demisemi circularity. So the biaxial joint
structure is described as Figure 4.
Figure 4: The sketch of final biaxial joint structure.
3.3 The Design of Medium in Joint
For the fit and stable of the structure of synovial
joints, there are other structures inside the joint, such
as articular cartilages.
See the sagittal section of temporomandibular
joint in Figure 5 (a), the articular disc suit on the
surfaces of two joint parts.
(a) (b)
Figure 5: (a) The sagittal section of temporomandibular
joint. (b) The sketch of connective band.
Simulate the structure and function of the articular
disc, a connective band is design as Figure 5 (b). It is
suited on the surfaces of two joint parts.
For keeping balance, three bands from different
directions interlude the joint cavity. See Figure 6.
Figure 6: The biaxial joint with connective band.
3.4 The Design of the Joint Driver
In the movement of articular, muscles drive the
joint. They compress and elongate to change the
direction between two attachments on the different
f
f
F
F F F
Connective band
Slot
Key
Dot for muscle
THE DESIGN OF BIAXIAL JOINT FOR MOBILE ELECTRONICS WITH THE ANALYSIS ON ARTHROSIS
139