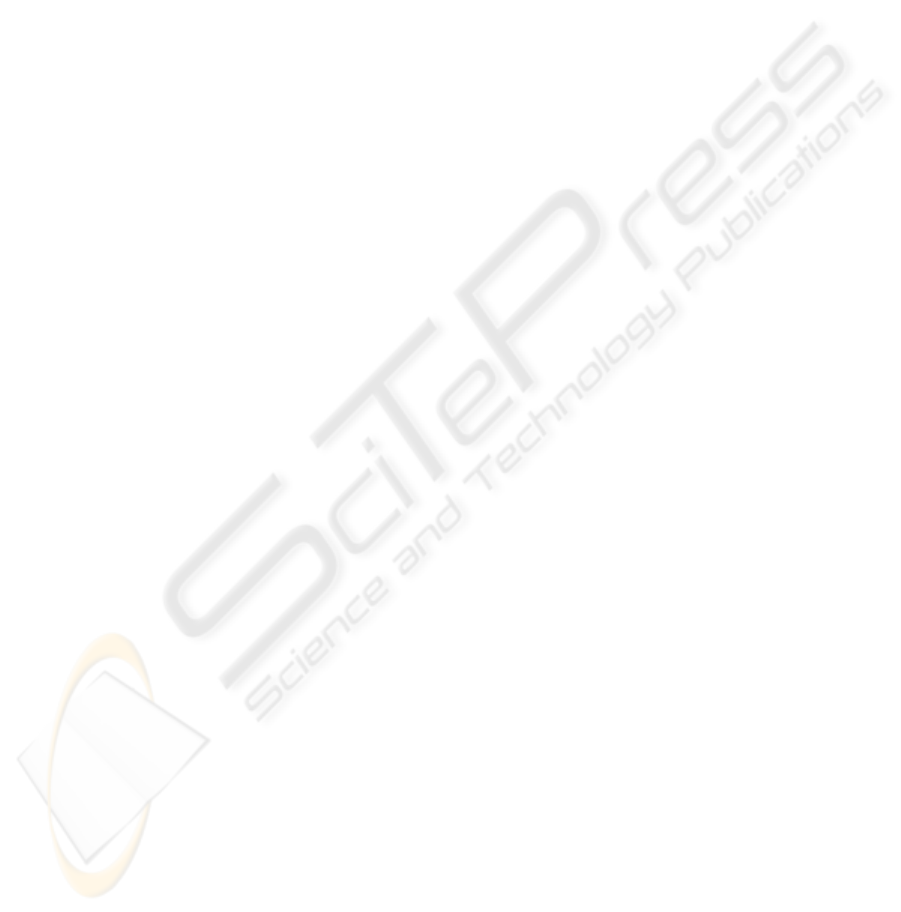
4 CONCLUSIONS
ECCR have a variety of advantages like:
- silent diving
- no bubbles
- maximized gas efficiency
- warm breathing gas
- humid breathing gas
Disadvantages are that the control of the pO
2
to
keep it within life sustaining limits at a constant
level depends on sensors which, with a low mean
time between failure (MTBF) of less than a year, are
prone to fail. State of the art solution is to deploy 3
pO
2
sensors for redundancy. This allows a reliable
detection of one sensor failure, but cases, where
more than one sensor show the same wrong values
cannot be detected, which may lead to a non life
sustaining pO
2
inside the loop followed by the death
of the diver. A stuck open solenoid is another failure
that may occur in a eCCR, resulting in a free flow of
O
2
, where the pO
2
inside the loop is increasing
rapidly, or the case where the solenoid is stuck
closed allowing no injection of fresh O
2
inside the
loop anymore.
The present paper describes a novel apparatus
that combines true sensor signal validation and a
reliable sensor failure detection with a safe injection
of O
2
, where cases like a free flow of O
2
are not
possible anymore.
In principle the apparatus can work with just one
pO
2
sensor, where in the case of a sensor failure a
alarm is given telling the diver to use his separate
emergency gas supply in open circuit mode and to
abort the dive.
As this system needs just one (or for redundancy
two pO
2
sensors, in the case of the failure of one pO
2
sensor, the dive can be continued with the other
working one). The costs for the yearly maintenance
are dramatically decreased (pO
2
sensors should be
changed once a year).
The authors are convinced that the further
development of this novel device will lead to a novel
kind of diving device for recreational purposes with
a dramatically increased safety, low weight of the
overall system and independency (180 min
maximum dive duration).
5 FUTURE WORK
Near future work will include a further development
of the presented electronics, an integration of a
second controller for redundancy, a head up display
mounted on the mouthpiece with LEDs for status
information and a breathing frequency sensor. As
the breathing frequency increases with increasing
work load (and O
2
metabolism), this parameter
allows another cross check giving more safety to the
final product.
Typical for electrochemical pO
2
sensors for
diving is that at the end of the dive the signal is
slightly deviating from the reference signal (during a
dive the sensors are very warm and humid gas under
high pO
2
, factors which present a quite extreme
environment – so even if most pO
2
Sensors are
temperature compensated changes in the slope of the
sensors are not unusual during a dive) Another
function that will be implemented in the next
firmware release is an advanced sensor signal
processing that, in the case of relatively small signal
deviations allows a sensor recalibration during the
dive (but only if the sensor is still linear, which can
be checked with 2 reference gases (O
2
and diluent).
REFERENCES
Divers Alert Network, 1992, Report on Diving Accidents
& Fatalities, Divers Alert Network, Box 3823, Duke
University Medical Center, Durham, NC 27710, 1994.
U.S. Navy Diving Manual, 2005, Volume 2 and Volume
4, SS521-AG-PRO-010, Direction of Commander,
Naval Sea Systems Command, USA
NOAA Diving Manual, Diving for Science and
Technology, 4
th
edition, US Department of Commerce,
National Technical Information Service, Springfield
Ehm, O.F., Hahn, M., Hoffmann, U., Wenzel, J., 1996,
Der neue Ehm, Tauchen noch sicherer, 9th edition,
ISBN 3-275-01484-6, Mueller Rueschlikon Verlags
AG, CH-6330 Cham.
Dederichs, H., Floren, G., Waldbrenner, M., Wilhelm, R.,
2004, Handbuch Technisches Tauchen, ISBN 3-275-
01492-7, Mueller Rueschlikon Verlags AG, CH-6330
Cham.
Mount, T., Gilliam, B., Bohrer R., Taylor, L., Sommers, L.
H., Crea, J., Nordsteam, R., 1992, Mixed Gas Diving,
ISBN 0-922769-30-3, Watersports Publishing, San
Diego, USA.
Deas, R.A., Evtukhov, M.V., 2003, Control electronics
system for rebreather, UK Patent Application, GB
2404539 A.
Deas, R.A., Evtukhov, M.V., 2003, Automatic Control
System for Rebreather, United States Patent
Application Publication, US 2003/0188744 A1
Baran, U., Frost, A.J., 2004, Diving Equipment Monitor,
PCT, WO 2004/112905 A1
Straw, P.E., 2005, Rebreather Setpoint Controller and
Display, PCT, WO 2005/107390 A2
Parker, M., 2005, Evolution Closed Circuit Rebreather
and Inspiration Closed Circuit Rebreather, Ambient
Pressure Diving Ltd., Helston, Cornwall, UK
NOVEL CONTROLLER FOR REBREATHER DIVING SYSTEMS - True Sensor Signal Validation and Safe Oxygen
Injection
49