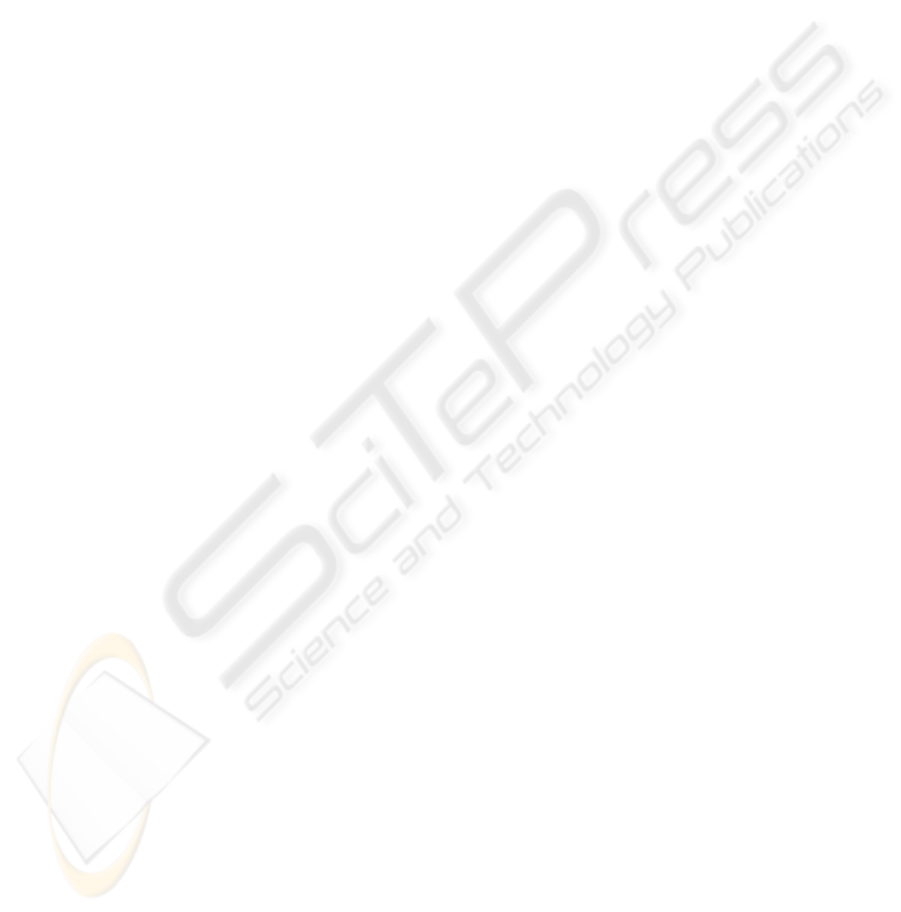
method (Casas, 2004) and a solution filtering
algorithm based on the least median of squares
(Casas, 2006). Once the positions of the emitter
probes have been obtained, the trajectory of the
resectoscope is obtained as well.
In order to verify the system, an experiment set-
up has been designed with the motor workbench
managed by the computer system in auto-calibration
mode. Figure 8 illustrates the results obtained. It
shows the position of an emitter probe located at the
end of the resectoscope. An emitter transducer is
attached to the mock up, which moves using a
predefined pattern. With three receivers, the results
are very accurate (few millimetres), and even the
bounces and oscillations of the mechanical system
itself can be detected.
5 CONCLUSIONS
Training surgery residents who start with endoscopic
operations remain a challenge. This paper has
described an electromechanical system developed
for learning the TUR technique. It consists of a
trainer’s workbench with a wireless sensing device
connected to several trainees’ workbenches with
motorised devices. These devices have a
resectoscope mounted on an electromechanical
structure able to reproduce all the movements of an
actual endoscopic operation.
The system has several operating modes that will
make it possible to:
– Reproduce the movements of an expert
surgeon in the hand of the trainee.
– Reproduce the pre-recorded movements of an
actual operation in the hand of the trainee.
– Assess the level reached by the student before
participation in any operations or in solving
problems requiring a certain degree of experience.
As a complement, a millimetrically accurate,
ultrasound-based positioning system has been
developed. This will be mounted on a resectoscope
in order to capture the movements performed in an
real operation. The management software of the
training room allows easy integration of these data
with the endoscopic video, to rely on an adequate
operations database.
What remains is to assess this tool in the
practical conditions of training urology residents in
the use of medical equipment, which will doubtless
offer most interesting data regarding the use or need
for modifications of the global system.
ACKNOWLEDGEMENTS
This work has been partially supported by the
Spanish Ministry of Science and Technology under
CICYT project numbers TIC2003-07766 and
TIN2006-15617-C03-02
REFERENCES
Anastasi, G., Bandelloni, R., Conti, M., Delmastro, F.,
Gregori, E. Mainetto, G., 2003. Experimenting an
Indoor Bluetooth-based Positioning Service.
ICDCSW’03, Proc. of the 23rd Int. Conf. on
Distributed Computing Systems Workshops, 480-483.
Ballaro, A., Briggs, T., Garcia-Montes, F., MacDonald,
D., Emberton, M., Mundy, A.R., 1999. A computer
generated interactive transurethral prostatic resection
simulator. The Journal of Urology, 162 (5), 1633-
1635.
Casas, R., 2004. BLUPS: Bluetooth and Ultrasounds
Positioning System. Doctoral Dissertation, University
of Zaragoza.
Casas, R., Marco, A., Guerrero, J.J., Falcó, J., 2006.
Robust Estimator for Non-Line-of-Sight Error
Mitigation in Indoor Localization. EURASIP J.
Applied Signal Processing, vol. 2006, article ID
43429, 1–8.
Fukuju, Y., Minami, M., Morikawa, H., Aoyama, T.,
2003. DOLPHIN: An Autonomous Indoor Positioning
System in Ubiquitous Computing Environment. Proc.
of the IEEE Workshop on Software Technologies for
Future Embedded Systems, 53-56.
Gettman, M.T., Hoznek, A, Salomon, L, Katz, R,
Borkowski, T, Antiphon, P, Lobontiu, A, Abbou, C.C.,
2003. Laparoscopic radical prostatectomy: Description
of the extraperitoneal approach using the Da Vinci
robotic system. The Journal of Urology, 170 (2 Pt 1),
416-419.
Gomes, M.P.S.F., Barret, A.R.W., Timoney, A.G., Davies,
B.L., 1999. A computer-assisted training/monitoring
system for TURP structure and design. IEEE Trans.
Information Technology in Biomedicine, 3 (4), 242-
251.
Katz, R, Nadu, A, Olsson, L.E., Hoznek, A, De La Taille,
A, Salomon, L, Abbou, C.E., 2003. A simplified 5-
step model for training laparoscopic urethrovesical
anastomosis. The Journal of Urology, 169 (6), 2041-
2044.
Kerfoot, B.P., Baker, H, Volkan, K, Church, P.A.,
Federman, D.D., Masser, B.A., De Wolf, W.E., 2004.
Development of validated instrument to measure
medical student learning in clinical urology: A step
toward evidence based education. The Journal of
Urology, 172 (1), 282-285.
Mahajan, A., Walworth, M., 2001. 3-D Position Sensing
Using the Differences in the Time-of-Flights from a
BIODEVICES 2008 - International Conference on Biomedical Electronics and Devices
80