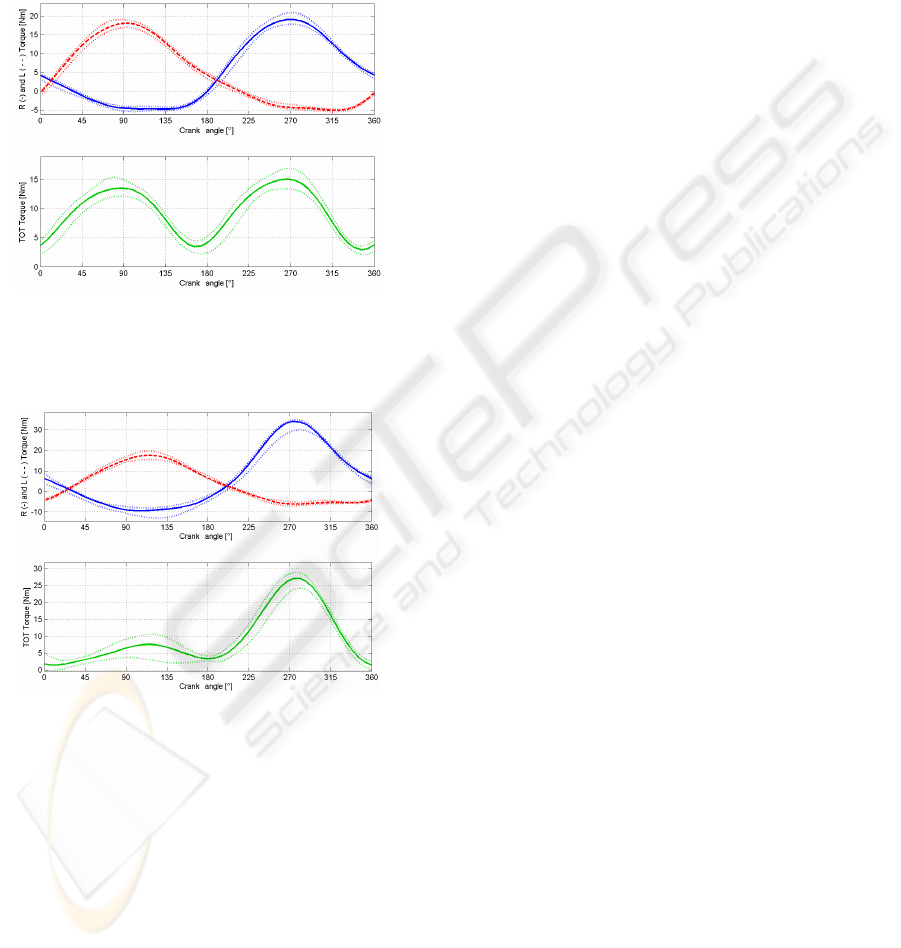
better waveform of the cycling and allows a better
comparison between healthy and non healthy
subjects and between the same patient before and
after the rehabilitation. Figure 10 shows the torque
from a healthy subject, while in Figure 11 the same
subject was asked to use only the right leg. The zero
crank angle is set at the maximum flexion of the left
hip.
Figure 10: Median torque from a healthy subject actively
cycling: (a) the left (dashed) and right (solid) components,
(b) total torque that show nearly symmetric peaks. In
dotted line the 5
th
-95
th
percentiles.
Figure 11: Same as the previous figure but related to an
healthy subject, asked to cycle only with the right leg; the
curves show highly asymmetric peaks.
The situation of a healthy subject asked to cycle only
with the right leg simulates only one of the many
possible cases of pathologic patients, where one of
the legs is very weak but not completely passive.
Indeed a healthy subject is unable to perform a true
passive pedaling, as shown in Figure 11(a), where
the left leg curve (dashed) is nearly flat in the
angular range 270-360°, indicating that the weight of
the leg is unconsciously partially compensated.
5 CONCLUSIONS
The paper deals with the design and the realization
of a measurement system able to measure relevant
quantities of the cycling, such as the torque (left,
right and total), power, energy, unbalance and jerk.
The experimental tests involved both healthy
subjects and spinal cord injured patients. Examples
of the obtained measurements had been shown
extensively in the figures. The results obtained up to
now allowed the doctors and physiotherapists to
have at their disposal additional and metrological
qualified information, useful for diagnostic purposes
and for checking the effects of the rehabilitation.
ACKNOWLEDGEMENTS
This work was supported by the Fondazione Cariplo
in the framework of the research program
HINT@Lecco. Authors would like to acknowledge
Mauro Rossini (Villa Beretta Rehabilitation Center)
for his helpful discussion.
REFERENCES
Comolli, L., Cantatore, A., Zappa, E., Bocciolone, M.,
Molteni, F., 2005. HINT@LECCO project:
metrological characterization of a cycle-ergometer,. In
SIAMOC 05, 6th Congress of the Italian Society of
Movement Analysis in Clinics.
Ferrante, S., Pedrocchi, A., Gioia, M., Ferrigno, G.,
Molteni, F., 2005. HINT@LECCO project: FES
cycling optimization and first clinical experiments of
on patients. In SIAMOC 05, 6th Congress of the
Italian Society of Movement Analysis in Clinics.
Ferrante, S., Pedrocchi, A., Ferrigno, G., Molteni, F.,
2006. Experimental campaign of FES cycling on
hemiplegics: first results. In SIAMOC 06, 7th
Congress of the Italian Society of Movement Analysis
in Clinics.
Gföhler, M., Angeli, T., Eberharter, T., Lugner, P., Mayr,
W., Hofer, C., 2001. Test Bed with Force-Measuring
Crank for Static and Dynamic Investigations on
Cycling by Means of Functional Electrical
Stimulation. IEEE Transactions On Neural Systems
And Rehabilitation Engineering, Vol. 9, No. 2, June
2001, pp. 169-180.
Mimmi, G., Pennacchi, P., Frosini, L., 2004.
Biomechanical Analysis of Pedalling for
Rehabilitation Purposes: Experimental Results on Two
Pathological Subjects and Comparison with
Non-pathological Findings. Computer Methods in
Biomechanics and Biomedical Engineering, Vol. 7,
No. 6, Dec. 2004, pp. 229-345.
(a)
(b)
(a)
(b)
METROLOGICAL CHARACTETIZATION OF A CYCLE ERGOMETER
27