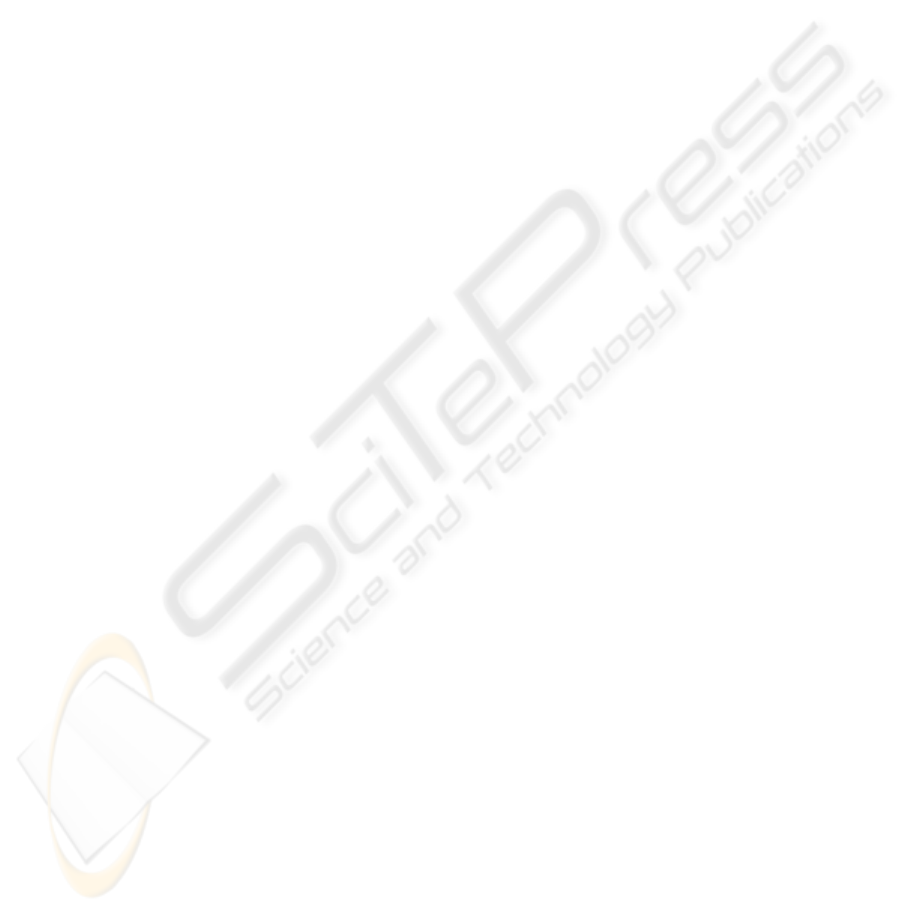
muscle fatigue. The average normalized MMG
RMS
,
TORQUE
RMS
, and TORQUE
PEAK
curves seem to
converge for values below approximately 80% of
maximum normalized amplitude and diverge above
it. Similar results were found by researchers
studying isometric contractions (Orizio et al.,
1989b). However, it is not possible to affirm that
volunteers used MVC, because data have been
normalized.
5 CONCLUSIONS
When computing spectral values based on MMG
monitoring of muscle contraction, it is important to
consider the effect of the sensor adhesion technique
because it can influence the calculus of e.g. mean
power frequency. The moduli of the signals acquired
by the triaxial accelerometer sensor present good
correlation with RMS and peak torque. MMG
MOD
can be a good indicator of torque loss during
isokinetic contractions. The MMG and torque
amplitudes (RMS and peak) seem to converge for
values below 80% of normalised data (presumably
80%MVC). The results obtained in the preliminary
tests, with three volunteers, showed that the sensor is
viable. These tests consist in the initial efforts for
assessing the sensor and it will be complemented
with a wider volunteer population.
ACKNOWLEDGEMENTS
Guilherme Nogueira would like to thank CNPq –
Conselho Nacional de Desenvolvimento Científico –
Fundação Araucária and FINEP for the financial
support.
REFERENCES
Brozovich, F. V., & Pollack, G. H. (1983). Muscle
contraction generates discrete sound bursts.
Biophysical Journal, 41(1), 35-40.
Cescon, C., Farina, D., Gobbo, M., Merletti, R., & Orizio,
C. (2004). Effect of accelerometer location on
mechanomyogram variables during voluntary,
constant-force contractions in three human muscles.
Medical and Biological Engineering and Computing,
42(1), 121-127.
Evetovich, T. K., Housh, T. J., Stout, J. R., Johnson, G.
O., Smith, D. B., & Ebersole, K. T. (1997).
Mechanomyographic responses to concentric
isokinetic muscle contractions. European Journal of
Applied Physiology and Occupational Physiology,
75(2), 166-169.
Fitts, R. H. (1994). Cellular mechanisms of muscle
fatigue. Physiol Rev, 74(1), 49-94.
Hudash, G., Albright, J., McAuley, E., Martin, R., &
Fulton, M. (1985). Cross-sectional thigh components:
computerized tomographic assessment. Med Sci Sports
Exerc, 17(4), 417-421.
Orizio, C. (1993). Muscle sound: bases for the
introduction of a mechanomyographic signal in muscle
studies. Crit Rev Biomed Eng, 21(3), 201-243.
Orizio, C., Gobbo, M., Diemont, B., Esposito, F., &
Veicsteinas, A. (2003). The surface mechanomyogram
as a tool to describe the influence of fatigue on biceps
brachii motor unit activation strategy. Historical basis
and novel evidence. European Journal of Applied
Physiology, 90(3 - 4), 326-336.
Orizio, C., Perini, R., & Veicsteinas, A. (1989a). Changes
of muscular sound during sustained isometric
contraction up to exhaustion. Journal of Applied
Physiology, 66(4), 1593-1598.
Orizio, C., Perini, R., & Veicsteinas, A. (1989b). Muscular
sound and force relationship during isometric
contraction in man. European Journal of Applied
Physiology and Occupational Physiology, 58(5), 528-
533.
Salles, F. A., Müller, R. W., Nogueira-Neto, G. N.,
Button, V. L., & Nohama, P. (2006). Sistema de
análisis de señales mecanomiográficas (MMG). Paper
presented at the XXIV Congreso Anual de la Sociedad
Española de Ingeniería Biomédica, Pamplona, Spain.
Shinohara, M., Kouzaki, M., Yoshihisa, T., & Fukunaga,
T. (1998). Mechanomyogram from the different heads
of the quadriceps muscle during incremental knee
extension. European Journal of Applied Physiology,
78(4), 289-295.
Stokes, M. J., & Cooper, R. G. (1992). Muscle sounds
during voluntary and stimulated contractions of the
human adductor pollicis muscle. Journal of Applied
Physiology, 72(5), 1908-1913.
Watakabe, M., Mita, K., Akataki, K., & Ito, K. (2003).
Reliability of the mechanomyogram detected with an
accelerometer during voluntary contractions. Medical
and Biological Engineering and Computing, 41(2),
198-202.
Zagar, T., & Krizaj, D. (2005). Validation of an
accelerometer for determination of muscle belly radial
displacement. Medical and Biological Engineering
and Computing, 43(1), 78-84.
MECHANOMYOGRAPHIC SENSOR - A Triaxial Accelerometry Approach
179