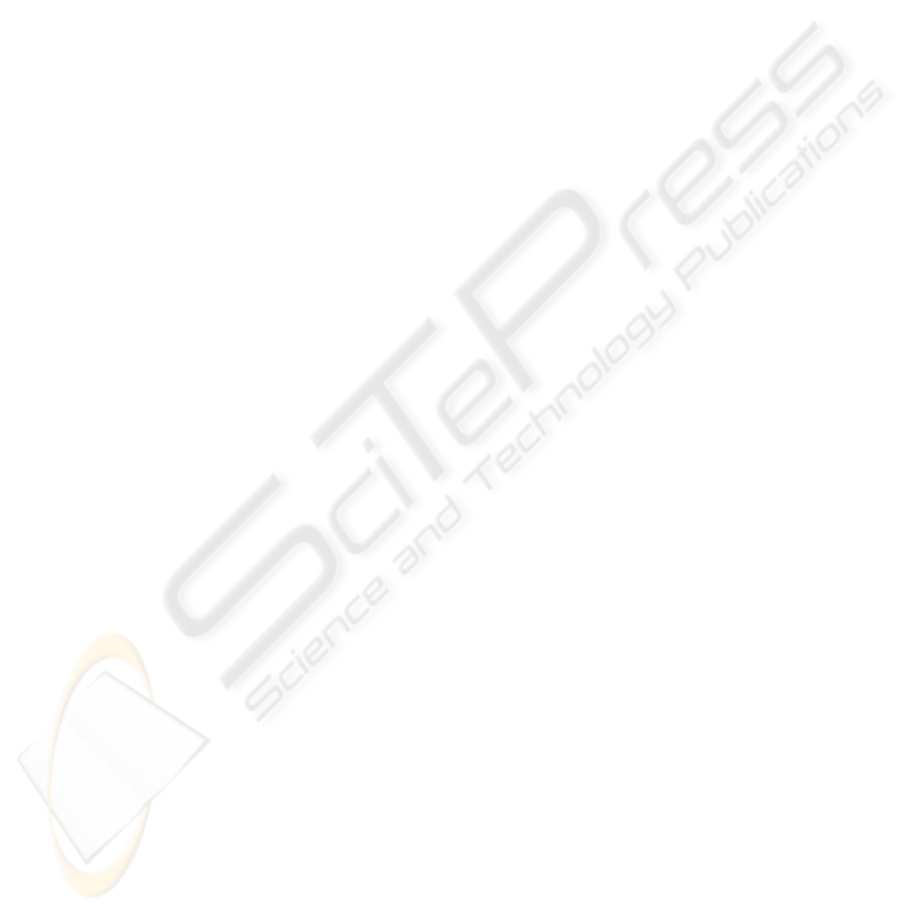
tuning using artificial neural network. In IEEE (Ed.),
38th IEEE Midwest Symposium on Circuits and
Systems, 2, pp. 641-644.
Jones, D. I., Mansoor, S. P., Aris, F. C., Jones, G. R.,
Bradley, D. A., & King, D. J. (2004). A standard
method for specifying the response of hydroelectric
plant in frequency-control mode. Electric Power
Systems Research , 68, 19-32.
Kang, J. K., Lee, J. T., Kim, Y. M., Kwon, B. H., & Choi,
K. S. (1991). Speed controller design for induction
motor drivers using a PDF control and load
disturbance observer. IECON (pp. 799-803). Kobe,
Japan: IEEE.
Kundur, P. (1994). Power System Stability and Control
New York. New York, USA: Mc Graw Hil.
Mansoor, S. P. (2000). PhD. Thesis. Behaviour and
Operation of Pumped Storage Hydro Plants. Bangor,
U.K.: University of Wales, Bangor.
Mansoor, S. P., Jones, D. I., Bradley, D. A., & Aris, F. C.
(1999). Stability of a pumped storage hydropower
station connected to a power system. IEEE Power
Eng. Soc. Winter Meeting (pp. 646-650). New York,
USA: IEEE.
Mansoor, S. P., Jones, D. I., Bradley, D. A., Aris, F. C., &
Jones, G. R. (2000). Reproducing oscillatory
behaviour of a hydroelectric power station by
computer simulation. Control Engineering practice ,
8, 1261-1272.
Minsky, M. L., & Papert, S. A. (1988). Perceptrons:
Introduction to Computational Geometry. Cambridge,
USA: MIT Press.
Narendra, K. S., & Mukhopadhyay, S. (1996). Adaptive
control using neural networks and approximate
models. American Control Conference (pp. 355-359).
Seattle, USA: IEEE.
Rumelhart, D. E., McClelland, J. L., & group, T. P.
(1986). Parallel distributed processing: Explorations
in the microstructure of cognition (Vol. 1).
Cambridge, USA: MIT Press.
Shu-Qing, W., Zhao-Hui, L., Zhi-Huai, X., & Zi-Peng, Z.
(2005). Application of GA-FNN hybrid control system
for hydroelectric generating units. International
Conference on Machine Learning and Cybernetics. 2,
págs. 840-845. IEEE.
Werbos, P. J. (1974). PhD. Thesis: Beyond regression:
New Tools for Prediction and Analysis in the
Behavioral Sciences. Cambridge, USA: Harvard
University, Cambridge, MA.
Widrow, B., & Hoff, M. E. (1960). Adaptive switching
circuits. IRE WESCON Convention Record, 4, págs.
96-104.
Working group on prime mover energy supply, I. (1992).
Hydraulic turbine and turbine control model for
system dynamic studies. IEEE Transactions on Power
Systems , 7, 167-179.
Yin-Song, W., Guo-Cai, S., & Ong-Xiang. (2000). The
PID-type fuzzy neural network control and it's
application in the hydraulic turbine generators. Power
Engineering Society meeting. 1, págs. 338-343. IEEE.
EVALUATION OF NEURAL PDF CONTROL STRATEGY APPLIED TO A NONLINEAR MODEL OF A PUMPED
STORAGE Hydroelectric Power Station
265