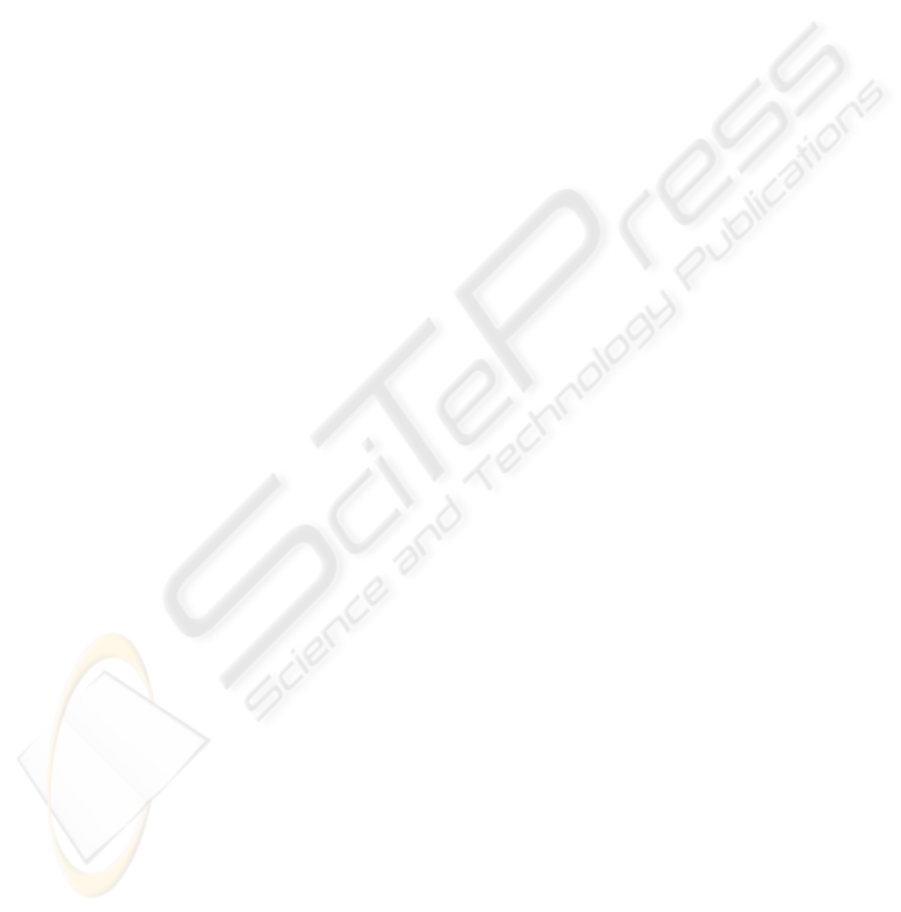
Weiser and Mr. Steffen Heute who both contributed
greatly to the development of the Epizactor.
REFERENCES
Chen Y, & McInroy JE. (2004). Decoupled control of
flexure-jointed hexapods using estimated joint-space
mass-inertia matrix. IEEE Transactions on Control
Systems Technology, 12(3), 413- 421.
Chung YG, & Lee B. (2000). Torque Optimizing Control
with singularity-robustness for kinematically
redundant robots. Journal of Intelligent and Robotic
Systems, 28, 231-258.
Dasgupta B, & Mruthyunjaya TS. (1998). A Newton-Euler
formulation for the inverse dynamics of the Stewart-
Platform manipulator. Mech. Mach. Theory, 33(8),
1135-1152.
El-Shenawy A, Wellenreuther A, Baumgart A, &
Badreddin E. (2007). Comparing Different Holonomic
Mobile Robots. Paper presented at the 2007 IEEE
International Conference on Systems, Man and
Cybernetics, Montreal, Canada.
Gough V, & Whitehall S. (1962, oder 1949). Universal
Tyre Test Machine. Paper presented at the IX Int.
Techn. Congr. F.I.S.I.T.A.
Hebsacker M, & Codourey A. (1998). Die Auslegung der
Kinematik des Hexaglide – Methodik für die
Auslegung paralleler Werkzeugmaschinen. Paper
presented at the VDI Fachtagung Parallele Strukturen,
TU Braunschweig.
Honegger M. (1999). Konzept einer Steuerung mit
Adaptiver Nichtlinearer Regelung für einen
Parallelmanipulator. Dissertation, ETH, Zürich.
Huynh P. (2001). Kinematic performance comparison of
linar type parallel mechanisms, application to the
design and control of a hexaslide. Paper presented at
the 5th International conference on mechatronics
technology (ICMT), Singapore.
Kesselring F. (1951). Bewertung von Konstruktionen.
Düsseldorf: Deutscher Ingenieur-Verlag.
Khalil W, & Guegan S. (2004). Inverse an Direct Dynamic
Modeling of Gough-Stewart Robots. IEEE
Transactions on Robotics, 20(4), 754-762.
Merlet JP. (1988). France Patent No. 2628670.
Pott PP. (unpublished). Untersuchung von Kinematiken für
handgehaltene Roboter. Dissertation, Universität
Mannheim, Mannheim.
Pott PP, Scharf H-P, & Schwarz MLR. (2005). Today's
State of the Art of Surgical Robotics. Journal of
Computer Aided Surgery, 10(2), 101-132.
Pott PP, & Schwarz MLR. (2007). The Relation of
Workspace and Installation Space of Epicyclic
Kinematics with six Degrees of Freedom. Zeitschrift
für Biomedizinische Technik, 52(5), 323-336.
Pott PP, Schwarz MLR, Köpfle A, Schill M, Wagner A,
Badreddin E, et al. (2003). ITD - A handheld
manipulator for medical applications - Concept and
design. Paper presented at the 3rd annual meeting of
CAOS, Marbella, Spain.
Pott PP, Wagner A, Badreddin E, & Schwarz MLR.
(submitted). Inverse Dynamic Model and a control
application of a Novel 6-DOF Hybrid Kinematics
Manipulator. IEEE Transactions on Mechatronics.
Pott PP, Wagner A, Köpfle A, Badreddin E, Männer R,
Weiser P, et al. (2004). A handheld surgical
manipulator: ITD - Design and first results. Paper
presented at the CARS, Chicago, Illinois, USA.
Pott PP, Weiser HP, Scharf H-P, & Schwarz MLR. (2004).
A gearing mechanism with 4 degrees of freedom for
robotic applications in medicine. Biomedizinische
Technik, 49(6), 177-180.
Stewart D. (1965). A Platform with six Degrees of
Freedom. Proc. of Mech. Eng., 180(1), 371-386.
Wagner A, Badreddin E, Weiser P, Köpfle A, Männer R,
Pott PP, et al. (2004). System Design and Position
Control of a Handheld Surgical Robotic Device. Paper
presented at the Mechatronics & Robotics Conference,
Aachen, Germany.
Wagner A, Pott PP, Köpfle A, Schwarz MLR, Scharf H-P,
Weiser P, et al. (2006, 12.-14.9.2006). Efficient
inverse dynamics of a parallel robot with two movable
platforms. Paper presented at the MECHATRONICS
2006 - 4th IFAC-Symposium on Mechatronic
Systems, Heidelberg.
Wenzel R, & Müller J. (1971). Entscheidungsfindung in
Theorie und Praxis. Stuttgart: VDI-Seminar.
ICINCO 2008 - International Conference on Informatics in Control, Automation and Robotics
110