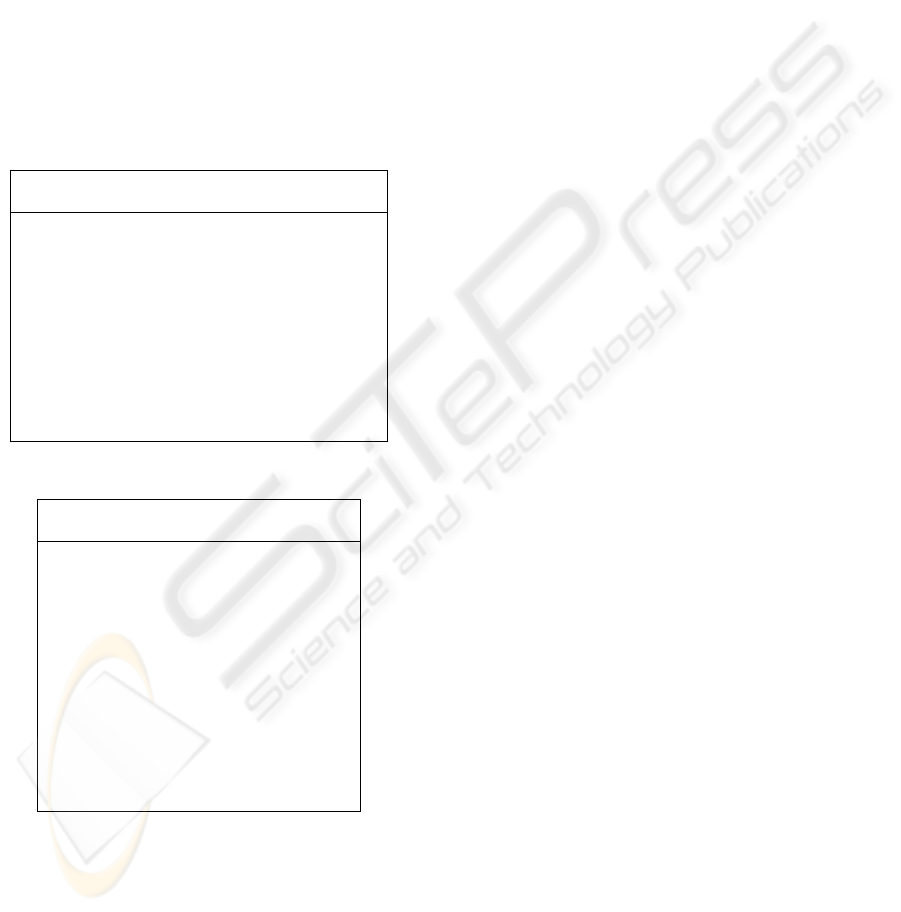
sufficient to guarantee fast and almost continuous
unloading operations by the quay cranes.
Long times are recorded for trailers when
waiting for quay cranes to load TEUs (more than 7
minutes for QC3 and about 6 minutes for QC4).
Then, one more trailer could help operations in the
yard area, because the maximum number of queued
trailers below a quay crane is three (see Table 9),
such that the other two are available for yard cranes.
Table 9 shows the results for the number of
entities in queue (the minimum value is always 0).
Table 10 shows the utilization of resources, i.e.
the percentage number of busy units or the
percentage busy time for single-unit resources (the
minimum is always 0, the maximum is always 1).
Table 9: Number of entities in queue of busy resources.
Busy
Res.
Average Min.
Aver.
Max.
Aver.
Max.
Value
TR1 0.0111 0.00 0.0199 1.0000
TR2 0.0114 0.00 0.0230 1.0000
YC1 0.6708 0.4637 0.9167 6.0000
YC2 0.0026 0.00 0.0062 1.0000
YC3 0.0056 0.00 0.0109 1.0000
TR3 0.2018 0.1911 0.2100 1.0000
TR3* 0.8882 0.8837 0.8906 1.0000
TR4 0.5703 0.5653 0.5770 1.0000
TR4* 0.1392 0.1339 0.1446 1.0000
QC3 1.5947 1.5753 1.6095 3.0000
QC4 1.3124 1.2990 1.3337 3.0000
Table 10: Utilization of resources.
Resource Average Min.
Aver.
Max.
Aver.
QC1 0.6104 0.6019 0.6218
QC2 0.6122 0.6036 0.6265
QC3 0.9919 0.9913 0.9926
QC4 0.9378 0.9324 0.9439
TR1 0.4818 0.4614 0.5013
TR2 0.4828 0.4660 0.5049
TR3 0.9897 0.9890 0.9899
TR4 0.9360 0.9307 0.9425
YC1 0.5712 0.5302 0.5970
YC2 0.1150 0.0892 0.1692
YC3 0.1617 0.1055 0.1812
YC4 0.8642 0.8612 0.8724
YC5 0.9825 0.9818 0.9831
Results for quay cranes indicate that unloading
with QC1 and QC2 terminates before loading with
QC3 and QC4. QC3 is used more than QC4 because
of the high number of empty TEUs. Considerations
about yard cranes are similar. Trailers TR1 and TR2
complete their tasks much earlier than TR3 and TR4,
which are practically always busy. Then, the
transport processes could benefit from more trailers.
5 CONCLUSIONS
This paper presents simulates a maritime terminal
container (TCT) in standard operating conditions.
Results prove the benefit from new control strategies
different from those currently used. A new control
approach could reduce terminal operating cycles in
standard and, above all, in perturbed operating
conditions.
REFERENCES
Bielli, M., Boulmakoul, A., Rida, M., 2006. Object
oriented model for container terminal distributed
simulation. European Journal of Operational
Research, Vol. 175, No. 3, pp. 1731-1751.
Cantarella, G.E., Cartenì, A., de Luca, S., 2006. A
comparison of macroscopic and microscopic
approaches for simulating container terminal
operations. In Proc. of EWGT2006 Joint conference,
Bari, Italy, 27-29 Sept. 2006.
de Luca, S., Cantarella, G.E., Cartenì, A., 2005. A
macroscopic model of a container terminal based on
diachronic networks. In Proc. Second Workshop on
the Schedule-Based Approach in Dynamic Transit
Modelling, Ischia, Naples, Italy, 29-30 May 2005.
Fischer, M., Kemper, P., 2000. Modeling and Analysis of
a Freight Terminal with Stochastic Petri Nets. In Proc.
of 9th IFAC Int. Symp. Control in Transp. Systems,
Braunschweig, Germany, vol. 2, pp. 195-200.
Kelton, W.D., Sadowski, R.P., Sadowski, D.A., 1998.
Simulation with Arena, McGraw Hill, New York.
Kozan, E., 2000. Optimising container transfers at
multimodal terminals. Mathematical and Computer
Modelling, Vol. 31, No. 10-12, pp. 235-243.
Legato, P., Mazza, R.M., Sept. 2001. Berth planning and
resources optimisation at a container terminal via
discrete event simulation. European Journal of
Operational Research, Vol. 133, No. 3, pp. 537-547.
Liu, C.I., Ioannou, P.A., 2002. Petri Net Modeling and
Analysis of Automated Container Terminal Using
Automated Guided Vehicle Systems. Transportation
Research Record, No. 1782, pp. 73-83.
Mastrolilli, M., Fornara, N., Gambardella, L.M., Rizzoli,
A.E., Zaffalon, M., 1998. Simulation for policy
evaluation, planning and decision support in an
intermodal container terminal. In Proc. Int. Workshop
Modeling and Simulation within a Maritime
Environment, Riga, Latvia, 6-8 Sept. 1998, pp. 33-38.
Steenken, D., Voss, S., Stahlbock, R., 2004. Container
terminal operation and operations research - a
classification and literature review. OR Spectrum, 26,
pp. 3-49.
Zeigler, B.P., Praehofer, H., Kim, T.G., 2000. Theory of
Modelling and Simulation, Academic Press. New
York, 2
nd
ed..
ICINCO 2008 - International Conference on Informatics in Control, Automation and Robotics
176