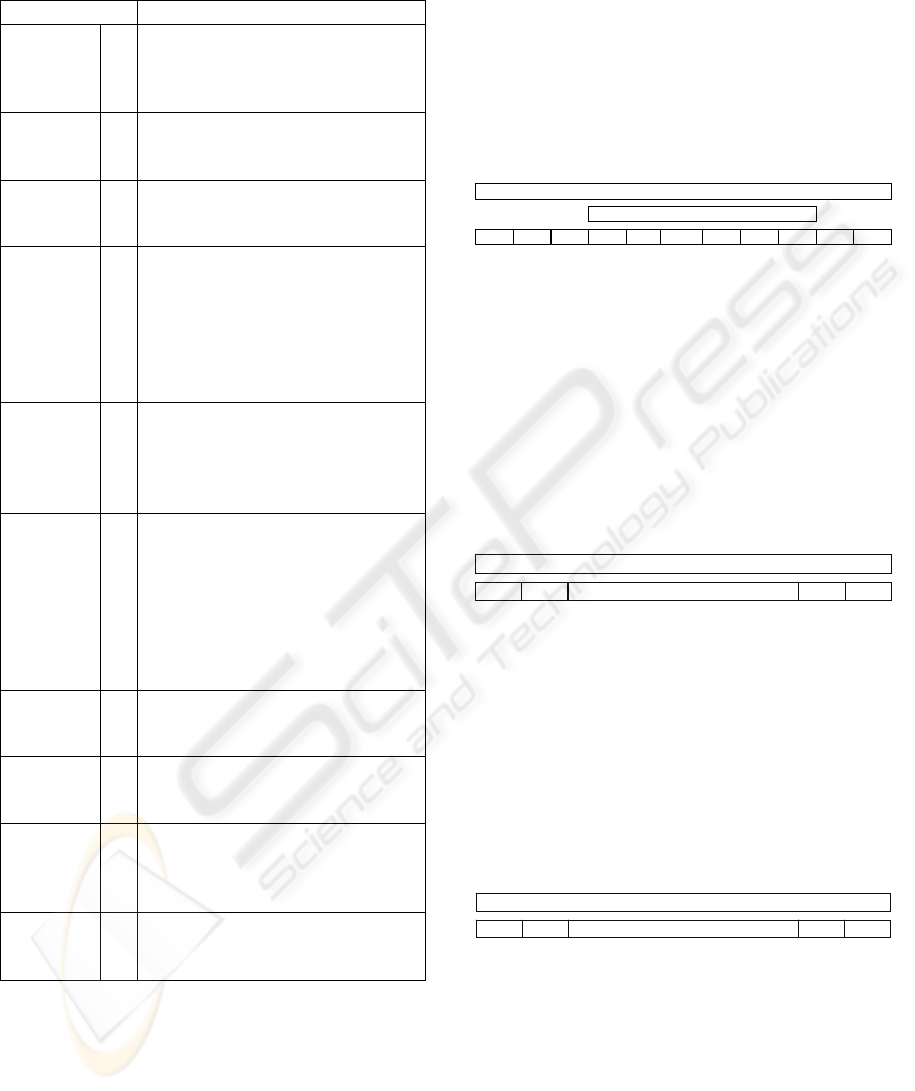
Table 1: Time segments which influence the transmission
delay value.
Time Segments Remark
Latency of
application
interface
T
ai
The data transfer between application
module and communication module
may influence the transmission delay
value remarkably.
Latency of
implemen-
tation
T
i
The implementation of the
communication module influences the
transmission delay value remarkably.
User data
length
L
ud
The user data length is related to the
data which is generated or consumed
by the automation application.
Data rate Bd
ud
This rate is the radio transmission rate
of the user data. Sometimes a symbol
rate is given. In this case a symbol may
consist of more than one bit. The
header of a packet containing the user
data may be transmitted with another
data rate.
Technology
constant
T
tc
The technology constant contains all
technology relevant protocol overheads
which are the same for each
transmission such as fixed idle times or
the time to transmit headers or tails.
Technology
variable
T
tv
The technology variable contains all
technology relevant protocol overheads
which may vary for different
transmissions such as the time to get a
clear channel or the back-off time.
Depending on the technology,
acknowledgments are required to
complete a transmission.
umber of
retries
N
r
If a transmission is disturbed, the
packet is usually retransmitted. This
may be possible at different layers.
Transmission
deadline
DL In some cases the transmission is
terminated when a deadline is
exceeded.
Time
allocation of
additional
connections
Tac If there is more than one connection
established, the time allocated to the
other connections within the same
system has to be taken into account.
Global time
slot
T
GTS
In systems with TDMA the maximum
transmission delay can be calculated
considering the global time slot.
The random nature of the transmission delay is
being caused by the latency of the application
interface and implementation, by the technology
variable, the number of retries and the time
allocation for additional connections. In contrast to
wired communication, the wireless transmission is
affected much more by environmental influences.
Therefore, the random behaviour of the technology
variable together with the number of retries and the
time allocation for additional connections may
influence the transmission delay remarkably
Taking into account the time segments listed in
Table 1, the dependency of the transmission delay
can be described in different ways. The first way is
the given formula (1) and is illustrated in Figure
3.
()
td ai i ai i ud ud tc tv r ac
T =f T (p),T (p),T (c),T (c),L ,Bd ,T ,T ,N ,T (1)
Tai(p) Tai(c)Ttc1 Lud/BdudTi(p) Ti(c)Ttv2 …Tac
* Nr
Ttd
Ttv1 Ttc2
Figure 3: Time segments of transmission delay depending
on re-transmissions, data rate and data length.
The second way to describe the transmission is
given in formula (2) and Figure 4. The
maximum transmission delay is fundamentally
influenced by the maximum allowed deadline which
covers the random behaviour of the media related
time segments.
tdmax ai i ai i
T = f(T (p), T (p), T (c), T (c), DL) (2)
Tai(p) Tai(c)Ti(p) Ti(c)DL
Ttdmax
Figure 4: Time segments of transmission delay depending
on a transmission deadline.
The third way to describe the transmission delay
is given in formula (3) and shown in Figure 5.
The maximum transmission delay is fundamental
depending on the number of retries and the global
time slot.
tdmax ai i ai i r GTS
T = f(T (p), T (p), T (c), T (c), N , T ) (3)
Tai(p) Tai(c)Ti(p) Ti(c) N
r
* T
GTS
Ttdmax
Figure 5: Time segments of transmission delay depending
on a global time slot.
As an example typical results of transmission
delay measurements are depicted in Figure 6. The
lower part of the figure shows the number of
packets, relative to the sample size, with certain
transmission delay values. The above described
random nature of the transmission delay can be
observed. The reasons for the different values are
HOW TO ASSESS RELIABILITY OF INDUSTRIAL WIRELESS SOLUTIONS
125