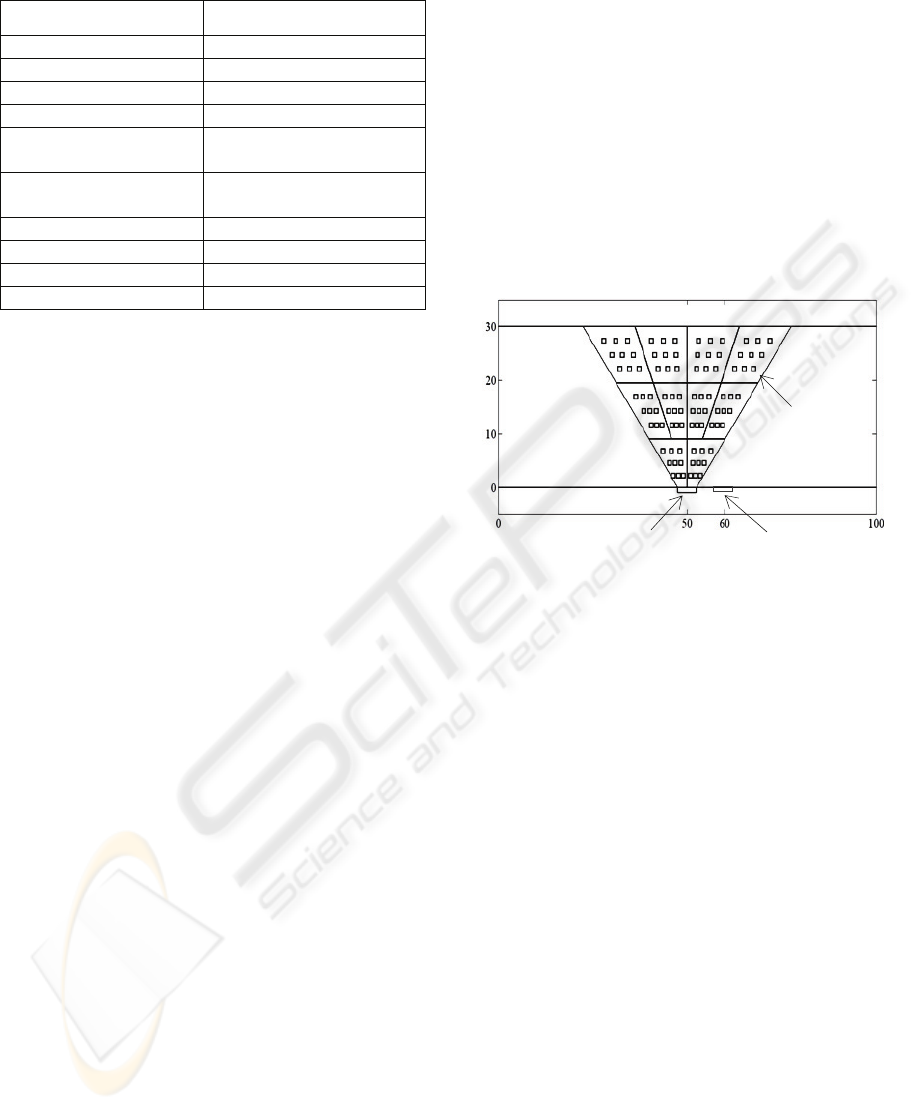
Table 2: Description of genetic algorithm parameters.
GA parameters settings Value or type
Initial population choice Random
Population size 100
Number of generations 100
Selection criterion Roulette wheel
Elitism (nr. of unchanged
individuals)
10
Crossover (nr. of selected
individuals)
50
Crossover rule Single point crossover
Crossover probability 1
Mutation probability 0.02
Termination criterion Maximum nr of generations
4 EXPERIMENTAL RESULTS
AND DISCUSSION
In order to test the proposed localization method, a
database of 90 simulated ultrasonic waveforms has
been obtained adopting the specimen and the
configuration analysis described in Section 2. In this
test case, 10 classes of defects with different
positions, inside the transducer radiation field, and 9
square voids (side 2 cm) for each class have been
considered, as shown in figure 3. Finally, the
collected signal set has been contaminated and
augmented by additive white Gaussian noise
considering four noisy waveforms for each signal of
the database. The extended data set of 90×4=360
waveforms, has been randomly divided into training
subset (90%) and test subset (10%) with the aim to
examine the robustness of the automatic
interpretation scheme. By according the above
described method, the 71 time and frequency
domain parameters for each waveform of the
database have been evaluated. Then the genetic
feature selection based on k-NN algorithm has been
used to select the optimal feature set for voids
position classification. The performances of k-NN
have been evaluated in terms of Mean Classification
Error (MCE), that is calculated as the mean of the
errors in the classification of the test set waveforms.
The better results have been obtained with the
number of neighbours k = 3 for the k-NN. In this
case, the MCE starts from a value of 38.89% in
correspondence of the whole set of 71 features, but
the GA-based feature reduction allows it to increase
up to the value of 97.22% with a selection of only 7
significant features listed below: Difference between
50% level and 25% level (spectrum CD); Difference
between 75% level and 25% level (spectrum CD);
Difference between 90% level and 25% level
(spectrum CD); Global rise frequency between 25%
level and peak of spectrum; Global rise frequency
between 50% level and peak of spectrum; Global
fall frequency between peak of spectrum and 50%
level; Global rise variance between 25% level and
peak of spectrum (CD = cumulative distribution).
The results show that the adopted method
provides a low error rate for the identification of
position of voids. Therefore, it would be a contribute
to develop an automatic method to localize defects
by means of ultrasonic analysis in concrete
structures. Future works will be devoted to a more
accurate identification of the position of voids.
Figure 3: 10 classes of defect in the radiation field.
REFERENCES
Berriman, J. R., Hutchins, D. A., Neild, A., Gan, T. H.,
Purnell, P., 2006. “The application of time-frequency
analysis to the air-coupled ultrasonic testing of
concrete”, IEEE Transactions on Ultrasonics,
Ferroelectrics and Frequency Control, Vol. 53, pp.
768 – 776.
Fan, X., Zuo, M.J., Wang, X., 2006. “Application of
stationary wavelet transforms to ultrasonic crack
detection”, Canadian Conference on Electrical and
Computer Engineering, pp. 1432 – 1436.
Acciani, G., Brunetti, G., Chiarantoni, E., Fornarelli, G.,
2006, “Automatic Evaluation of Flaws in Pipes by
means of Ultrasonic Waveforms and Neural
Networks”, International Joint Conference on Neural
Networks Sheraton Vancouver Wall Centre Hotel,
Vancouver, BC, Canada, pp. 892 - 898.
Rose, J. L., 1999, Ultrasonic Waves in Solid Media,
Cambridge University Press.
Muni, D.P., Pal, N.R., Das, J., 2006, “Genetic
programming for simultaneous feature selection and
classifier design”, IEEE Transactions on Systems,
Man and Cybernetics, Part B, Vol. 36, pp. 106 – 117.
Square void
Emitter
Receiver
ICEIS 2008 - International Conference on Enterprise Information Systems
234