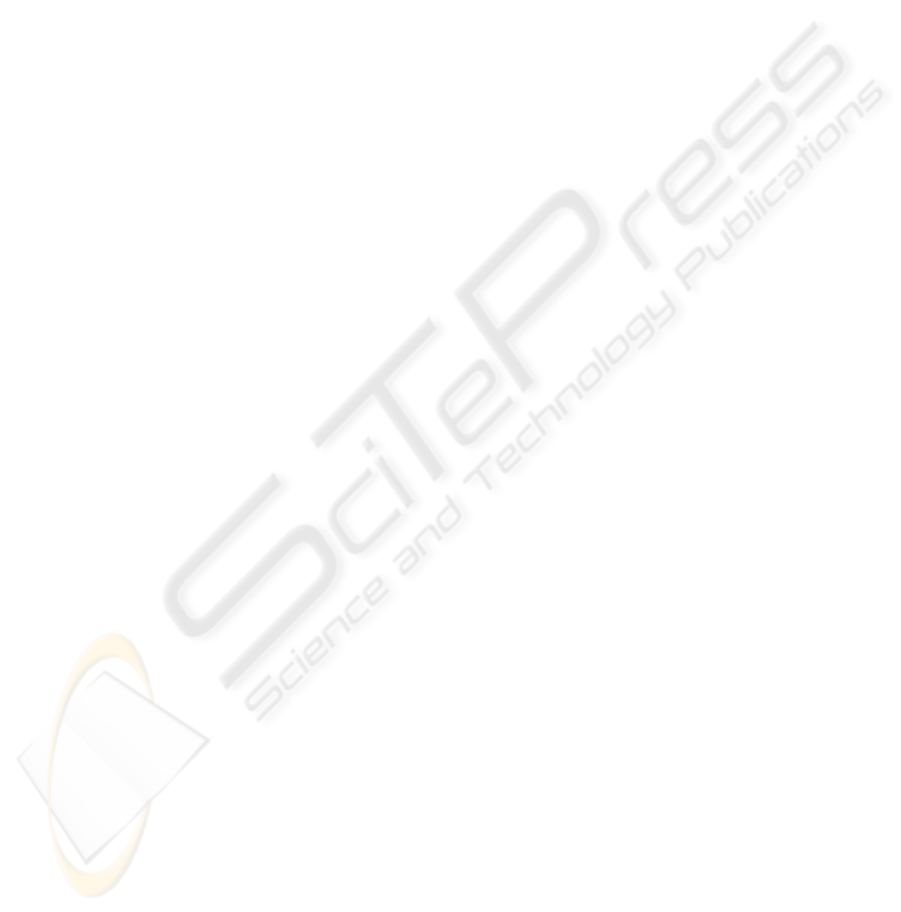
impact of the evaluation indicators identified on the
supplier selection.
A case study on an internationally well-known
auto lighting system OEM Company showed that the
proposed method really has the above advantages.
Through the results provided by the proposed
method, the present company can make some
adjustments for her suppliers in order to obtain more
attractive outcomes.
REFERENCES
Banker, R.D., Charnes, A., and Cooper, W.W., 1984.
Some models for estimating technical and scale
inefficiencies in data envelopment analysis.
Management Science, 30(9), pp.1078-1092.
Choi, T.Y., Hartley, J.L., 1996. An explortation of supplier
selection practices across the supply chain. Journal of
Operations Management, 1, pp.333-343.
Cooper, W. W., Huang, Z., Lelas, V., Li, S. X. and Olesen,
O. B., 1998. Chance Constraint Programming
Formulations for Stochastic Characterizations of
Efficiency and Dominance in DEA. Journal of
Productivity Analysis, 9, pp.53-79.
Cooper, W. W., Huang, Z. and Li, S. X., 1996. Satisfying
DEA Models under Chance Constraints. Annals of
Operations Research, 66, pp.279-295.
Csutora R. and Buckley, J. J., 2001. Fuzzy hierarchical
analysis: The Lambda-Max method. Fuzzy Sets and
Systems, 120, pp.181-195.
Dickson, G.W., 1996. An analysis of vender selection
systems and decisions. Journal of Purchasing, 2(1),
pp.5-17.
Goffin, K., Szwejczewski, M. and New, C., 1997.
Managing suppliers: when fewer can mean more.
International Journal of Physical Distribution and
Logistics Management, 27(7), pp.422-436.
Kao, C. and Liu, S.-T., 2000. Fuzzy efficiency measures in
data envelopment analysis. Fuzzy Sets and Systems,
113, pp. 427-437.
Kuo, R.J., Hong, S.M., Lin, Y., and Huang, Y.C., 2008.
Continuous genetic algorithm based fuzzy neural
network for learning fuzzy if-then rules,” Accepted by
Journal of Neuralcomputing.
Lehmann, D. R. and O’Shaughnessy, J., 1982. Decision
criteria used in buying different categories of products.
Journal of Purchasing and Materials Management,
pp.9-14.
Liu C.-M., Hsu H.-S., Wang S.-T. and Lee H.-K., 2005. A
performance evaluation model based on AHP and
DEA. Journal of the Chinese Institute of Industrial
Engineers, 22(3), pp. 243-251.
Mohanty, R. P. and Deshmukh, S. G., 1993. Using of
analytic hierarchic process for evaluating sources of
supply. International Journal of Physical Distribution
& Logistics Management, 23(3), pp.22-28.
Narasimhan, R., Talluri, S and Mendez, D., Summer 2001.
Supplier evaluation and rationalization via data
envelopment analysis: an empirical examination. The
Journal of Supply Chain Management.
Quayle, M., 2002. Puchasing in small firms. Eurpean
Journal of Purchaing and supply Management, 8,
pp.151-159.
Saaty, T.L., 1977. A scaling method for priorities in
hierarchical structures. Journal of Mathematical
Psychology, 15, pp. 234-281.
Schmitz, J., Platts, K.W., 2004. Supplier logistics
performance measurement: indication from a study in
the automotive industry. International Journal of
Production Economics, 89, pp.231–243.
Sengupta Jati K., 1992. A fuzzy systems approach in data
envelopment analysis. Computers Mathematic
Application, 24(8/9), pp.259-266.
Swift, C. O., 1995. Performance for single sourcing and
supplier selection criteria. Journal of Business
Research, 32(2), pp.105-111.
Smytka, D.L., Clemens, M.W., 1993. Total cost supplier
selection model: a case study. International Journal of
Purchasing and Materials Management, 29(1), pp.42-
49.
Thompson, K.N., winter 1990. Vendor profile analysis.
International Journal of Purchasing and Materials
Management, pp.11-18.
Wang, G., Huang, S.H., Dismuke, J.P., 2004. Product-
driven supply chain selection using integrated multi-
criteria decision-making methodology. International
Journal of Production Economics, 91, pp.1-15.
Weber, C. A., Current, J. R. and Benton, W. C., 1991.
Vendor selection criteria and method. European
Journal of Operational Research, 50(1), pp2-18.
Weber, C. A. and Current, J. R., 1993. A multiobjective
approach to vendor selection. European Journal of
Operational Research, 68(2), pp.173-176.
Wilson, E. J., 1994. The relative importance of supplier
selection criteria:a review and update. International
Journal of Purchasing and Materials Management,
30(3), pp.35-41.
ICEIS 2008 - International Conference on Enterprise Information Systems
246