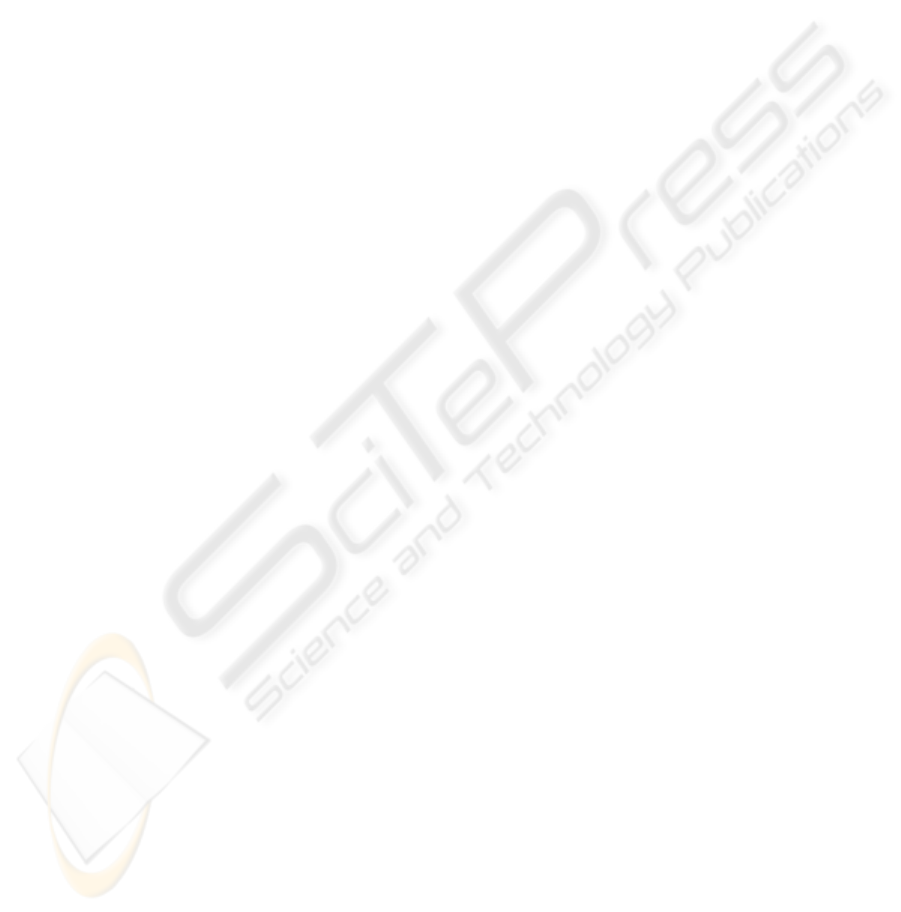
interrupted if the system would be down. The status
view and logs have to be maintained. The production
parameters have to be easily modified.
Defective product can be easily returned to the
production. The location information of the
defective product is very important so that it can be
transported as soon as possible to the unburden area.
There are several reasons for the defective products.
In the current manual system, the operator has to call
to a team responsible person before implying the
defective product. Some discussions have emerged
from the reasons for the failures on the process.
Breakdowns occur in the process. Thus, the
messages about the breakdowns have to be
registered to the system in real-time in order to share
the information in the whole process. A responsible
primary user argued that they need as accurate
information about the consuming rate of units as
possible. It is a significant trigger to the component
line and should be updated in real-time to the
system. The assembly machine can also register the
information about each unit running in the machine.
4 CONCLUSIONS
Manufacturing control systems are designed
according to the manufacturing logic of increasing
company productivity. Designing such a system
includes planning how the system will support the
tasks of end users. In this paper, a pluralistic
walkthrough method is used for evaluating a system
design from users’ perspective. The primary users,
e.g. the main operators in the system, were using a
paper prototype of the system according to
predefined scenarios of use. As a result their
comments were considered for the requirement
specification of the system.
Walkthrough methods provide an intensive way
to “walk through” the functionality of system
design, and iterate the design solution at the early
stage of the design process. Thus, the requirements
for system functionality can be verified before any
function is implemented. Moreover, using
walkthrough methods in the design phase may ease
the adoption stage as the users’ are already
introduced to the system.
The system designers may not be fully aware of the
everyday possibilities and practical restrictions, such
as breakdowns or product changes. The
communication ability between designers and users
help to avoid misunderstandings of the design
objectives.
Organisational change issues, such as job
redesign and changes of the individuals’ tasks, may
pose a threat to shop floor level workers. However,
in the walkthrough session the workers conduct their
tasks with the prototype of the new system.
Therefore, the workers are able to experience how
the new system will affect their work flows. The
issues that are raised during the session can be taken
into account also in the training plan for the new
system. The user acceptance and user satisfaction
are hard to measure, but users’ understanding of the
benefits of the system for their work can be clarified
in the walkthrough session.
The results of this paper affect the requirement
analysis and design process of the manufacturing
control system. In addition the walkthrough session
allowed communication between users and
designers, and introduced the users to the new
system in the early stages of design process.
REFERENCES
Bias, R., 1991. Interface-Walkthroughs: Efficient
Collaborative Testing. IEEE Software, Vol. 8, No. 5,
pp. 94-95.
Bias R., 1994. The Pluralistic Usability Walkthrough:
Coordinated Empathies, in Nielsen J. and Mack R. L
(Eds) Usability Inspection Methods. New York: Wiley
& Sons Inc.
Hermann, T., Kunau G., Loser K., Menold N., 2004.
‘Socio-Technical Walkthrough: Designing technology
along Work Processes’, Proceedings of the eighth
conference on Participatory design: Artful integration:
interweaving media, materials and practices - Volume
1, Participatory Design, Toronto, Ontario, Canada,
July 27-31, 2004, New York, NY, United States, ACM
Press, pp. 132-141.
Muller M. J., Matheson L., Page C., Gallup R., 1998.
Methods & tools: Participatory heuristic evaluation.
Interactions. Vol. 5, No. 5, pp. 13-18.
Nielsen J., 1994. Heuristic Evaluation, in Nielsen J. and
Mack R. L (Eds) Usability Inspection Methods. New
York: Wiley & Sons Inc.
Salmimaa, T., Vilpola, I., 2007. How to Design an
Efficient Electronic Kanban System – A Case
Study of Sociotechnical Design Process. The 11th
International Conference on Human Aspects of
Advanced Manufacturing Agility and Hybrid
Automation.
Yin, Robert K., 2002. Case Study Research: Design and
Methods.
WALKTHROUGH METHODS FOR IMPROVING THE SYSTEM FIT TO THE USERS’ TASKS WITHIN
MANUFACTURING OPERATIONS
383