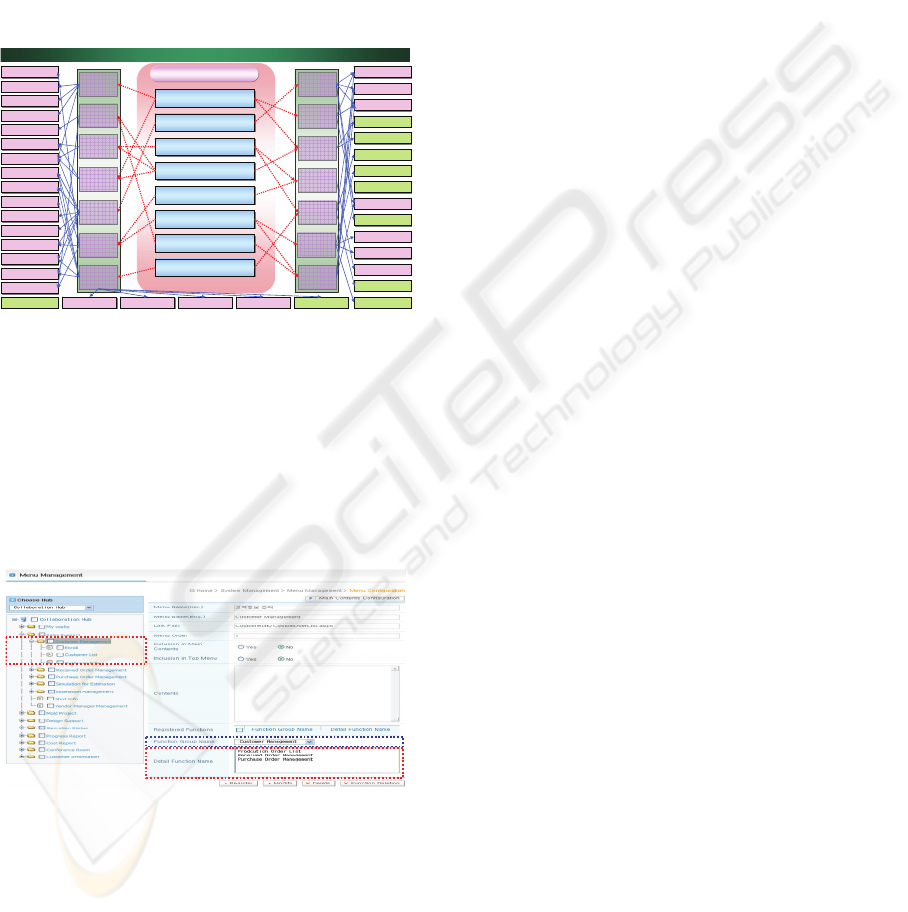
Design_Hub is the system to support collaborative
design of molds by providing useful tools including
CAD conference, visualizer for 3D CAD drawings,
collaborative project manager, etc. As illustrated in
Figure 7, users of the Design_Hub wanted to use
functions such as collaboration supports between
customer and company, sales support, efficient data
and schedule management, monitoring of production
processes in real time, etc. Based on such VoC, we
defined many services including customer support,
sales support, data management, etc., and developed
function modules as depicted in Figure 7.
Design Collaboration
System Management
System Management
User Information Mgnt.
User Information Mgnt.
Partnershi p Mgnt.
Partnershi p Mgnt.
Information Center
Information Center
Web Log Mgt.
Web Log Mgt.
Standard Process Mgnt.
Standard Process Mgnt.
Standard Class Mgnt.
Standard Class Mgnt.
Unit Cost Management
Unit Cost Management
Standard Parts Mgnt.
Standard Parts Mgnt.
Facilities M anagement
Facilities M anagement
Work-templates Mgnt.
Work-templates Mgnt.
Process-templates Mgnt.
Process-templates Mgnt.
Part-templates Mgnt.
Part-templates Mgnt.
Reporting & Simulation
Reporting & Simulation
Message Management
Message Management
e-Mail
e-Mail
Electronic Distribution
Electronic Distribution
Printing Matter Mgnt.
Printing Matter Mgnt.
Order Management
Order Management
Estimates Management
Estimates Management
Try-out Management
Try-out Management
Measurement Mgnt.
Measurement Mgnt.
Project Management
Project Management
Document/Drawing Mgnt.
Document/Drawing Mgnt.
Parts Management
Parts Management
CAD Data Exchange
CAD Data Exchange
Production Schedule Mgnt.
Production Schedule Mgnt.
CAD Conference
CAD Conference
Work Assignment
Work Assignment
Process Results Mgnt.
Process Results Mgnt.
Change History Mgnt.
Change History Mgnt.
Progress Status
Progress Status
Issue Management
Issue Management
Failure Management
Failure Management
My Job Management
My Job Management
Module Service Service ModuleCollaboration Hub
Collaboration Supports
b/w Customer and Company
Collaboration Supports
b/w Customer and Company
Sales Support
Sales Support
Design and Technical Info.
management
Design and Technical Info.
management
Data Transfer & Sharing
Data Transfer & Sharing
Monitoring of
Manufacturing Process
Monitoring of
Manufacturing Process
Management of
Manufacturing Execution
Management of
Manufacturing Execution
Production Result Management
Production Result Management
Product oriented Integration
of Collaboration Projects
Product oriented Integration
of Collaboration Projects
System
Management
Company
Information
Projects
Management
Schedule
Management
Data
Management
Distribution
Management
Change
Management
Reporting &
Simulation
My Work
Manufacturing
Execution
Sales
Support
Customer
Support
Engineering
Conference
Global
Collaboration
Process Change Mgnt.
Process Change Mgnt.
Schedule Management
Schedule Management
Figure 7: Composition of functions and services in the
Design_Hub.
According to the user’s purpose for using the
system, function modules can be reorganized in each
service by them. Furthermore, users can choose
proper or modify services. Figure 8 shows the screen
shot of the page that user can modify UI, services,
and functions. By developing flexibly restructurable
systems, users can use them with higher satisfaction.
Se r vi ce La ye r
Function Layer
Presentation Layer
Figure 8: Menu management in collaboration systems.
4 CONCLUSIONS
Led by the Korean government, the i-Manufacturing
project creates new value for the manufacturing
industry through collaboration among companies.
Through the project, Korean companies have
overcome the limitations of time and space to carry
out seamless production with overseas facilities and
clients, and manage the entire production process in
real-time. By using the system, they can reduce
delivery time and enhance product quality. In the
case of a conglomerate composed of nine small and
medium sized companies using Production_Hub,
average delivery time for molds has been reduced
from 44.7 days in 2004 to 24.6 days in 2006. Their
net profit has also increased 369.6% from 270
million won to 1.27 billion.
To widely enlarge the application areas of
collaboration systems rapidly and easily, we define a
common platform with pre-defined services
containing basic function modules. With this system
architecture and platform, we are developing two
brand-new systems and restructuring Production_
Hub for new conglomerates.
The easiest way to raise competitiveness and
realize manufacturing innovation is to develop and
to provide collaboration infrastructure especially for
small and medium sized companies. However, lots
of novel technologies regarding manufacturing
processes and systems also have to be developed and
combined with infrastructure to achieve innovation.
The i-Manufacturing project, we hope, will be the
answer of manufacturing innovation in Korea.
ACKNOWLEDGEMENTS
This paper is supported by the i-Manufacturing
projects funded by the Ministry of Commerce,
Industry and Energy(MOCIE) of Korea. The authors
would like to thank for their support.
REFERENCES
Lee, J., 2003. e-Manufacturing – fundamental, tools, and
transformation, Robotics and Computer Integrated
Manufacturing, 19: 501-507.
Ryu, K., Lee, S., and Choi, H., 2007a. Strategies based on
collaboration for manufacturing innovation in Korea.
In 37
th
International Conferences on Computers and
Industrial Engineering. Egypt. 954-960.
Ryu, K., Lee, S., Hong, W., Lee, D., and Choi, H., 2007b.
Business Innovation via Collaboration. In ICEIS2007.
Portugal. 198-201.
MODULARIZATION OF WEB-BASED COLLABORATION SYSTEMS FOR MANUFACTURING INNOVATION
177