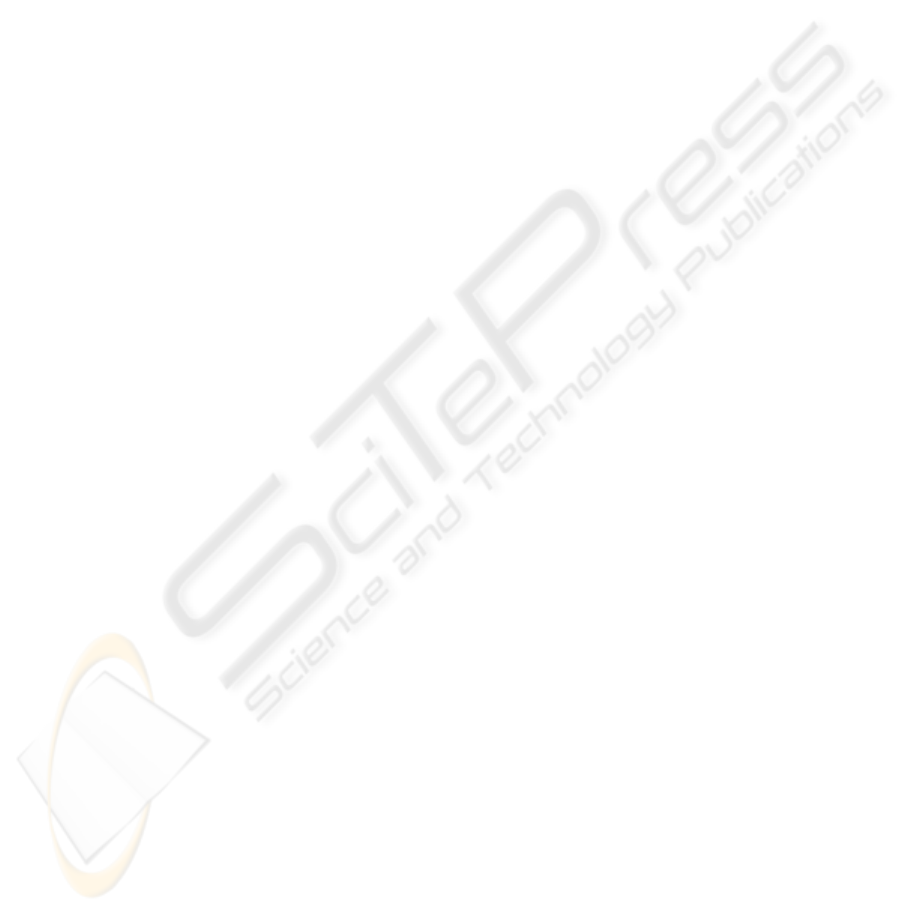
DEVICE FOR SYNCHRONIZED ROTATION
Shuh Jing Ying, Rufael Berhane and Rajiv Dubey
Department of Mechanical Engineering
University of South Florida
Tampa, Florida, U.S.A.
Keywords: Synchronization, Synchronized rotation.
Abstract: This device makes two shafts rotating in synchronized angular displacement. The sensors are potentiometers.
The device is designed for use in a driving simulator. The first shaft is connected to a steering wheel and
controlled by a driver so this shaft is the master, the second shaft is connected to the computer software that
displays the surrounding sceneries, therefore this shaft is the follower. The two shafts must be rotated in
synchronized mode and accurately. Major components in this device are operational amplifiers, NAND
gates, power MOFET and relays. Details in design and manufacturing are reported in this paper. This device
may be used for any place that requires two shafts rotating synchronically.
1 INTRODUCTION
Electronic Mobility Control Co.(EMC) developed an
Advanced Electronic Vehicle Interface Technology
(AVEIT) that converted the steering wheel, gas
pedal and brake pedal in a car into one joystick.
Based on the EMC system, we are building a driving
simulator for training disabled person to drive by
using a joystick for gas, brake and steering. The
forward movement of joystick is for gas pedal,
backward for brake, and right and left for steering.
However it is really difficulty for a person to drive a
real car without going through a simulator. A
simulator to be built is similar to an airplane
simulator for training pilot to drive an airplane. But
it is not so simple to build a driving simulator, many
man powers are required to work on the project from
design, computer software, and manufacturing.
Because of the limited man power and financial
resources, we bought a regular car simulator from
Simulator Systems International (SSI). It has three
screens to show the surrounding sceneries for the
driver to see. We hope to build a device that can
make EMC and SSI systems working
simultaneously. That is the whole purpose of this
project.
There are two possibilities for reaching the
synchronized rotation, mechanical and electrical
devices. After a length consideration the final
decision was on electrical approach.
Once electrical device is chosen we looked into
existing literature but to our surprise we could not
find any in our library or any nearby libraries.
Although we were pretty certain that synchronized
motors have been used in large airplanes but no
information is found. Anyway the existing device
may not fit what we need.
So we start to design a circuit for our purpose
and we build the device exactly as we want. The
details are given in this paper. After the device is
completed certainly we had quite extensive test to
check out every part. However we have not reached
to the point to train a disabled person actually to
drive.
2 DESIGN OF THE CIRCUIT
The circuit required is to operate a motor which has
enough power to rotate the steering mechanism of
the SSI system. The directions of rotation can be
clockwise and counterclockwise. The size of motor
is chosen to be similar to the servomotor used in the
EMC system. The input power of the motor is 93
watts with torque of 8.7 n-m. The motor is a geared
DC motor. Because there is no precise position
required in the operation analogue circuit is chosen
in the design. Potentiometers are used for the
position indicators and relays are used for the
control of the motor.
339
Ying S., Berhane R. and Dubey R. (2009).
DEVICE FOR SYNCHRONIZED ROTATION.
In Proceedings of the International Conference on Biomedical Electronics and Devices, pages 339-342
DOI: 10.5220/0001431903390342
Copyright
c
SciTePress