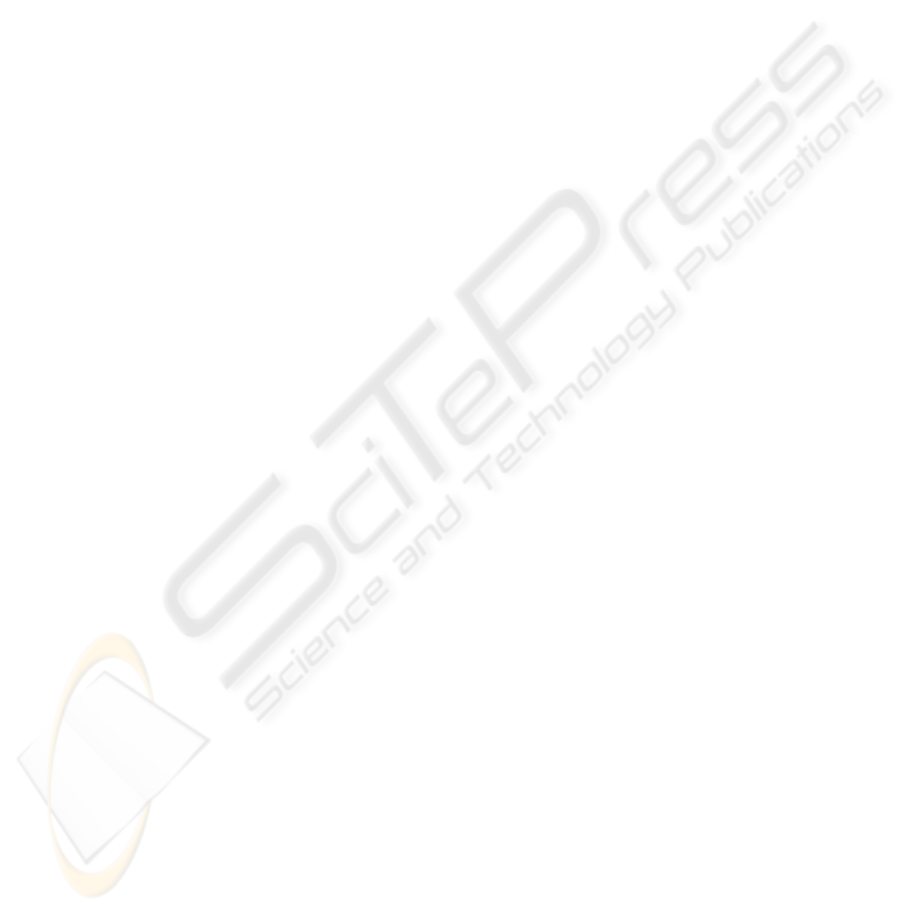
THE DESIGN AND FABRICATION OF
IMPLANTED INTRACRANIAL PRESSURE SENSOR
Tian Bian, Zhao Yulong and Jiang Zhuangde
State Key Laboratory for Manufacturing Systems, Xi’an Jiaotong University, Xi’an 710049, China
Keywords: Piezoresistive, Pressure sensor, Implantable intracranial pressure, Biocompatible.
Abstract: For the purpose of intracranial pressure measurement, implantable intracranial pressure monitoring sensor
applying to the long-term and real-time monitoring to the intracranial pressure of the brain patients, a
pressure sensor was designed based on the piezoresistive principle. The fabrication of pressure sensor
adopted the technology of bulk micromachining to form the structure, and used the ion implanted technique
to form resistances. The packaging was successfully fabricated by using biocompatible material, such as
titanium alloy and polyurethane. The output characteristic of the sensor is measured. It was demonstrated
that this pressure sensor has good performance, include linearity, accuracy and sensitivity for medical
applications.
1 INTRODUCTION
The intracranial pressure (ICP) is extremely valuable
in many cases in order to monitor and control the
clinical condition of a patient. Presently there are
essentially three types of intracranial-pressure
sensors: (a) the sensors requiring handling of the
cephalorachitic intraventricular liquid or cisternal
liquid, (b) the so called sub dural sensors to be
implanted in the subdural space between the dura
mater and the arachnoid, (c) the extra-dural sensors
to be implanted on the dura mater between this dura
mater and the skull.
The sensors of the first type (a) measure directly
the pressure of the cephalorachitic liquid which is
transmitted by a catheter to a transducer. The sensors
of the second type (b) measure the intracranial
pressure by using the arachnoid as an interface, the
arachnoid being a very fine and very flexible
membrane capable of integrally transmitting the
pressures. In both cases the pressure to be measured
is directly accessible, without there being
distortions, whereby the measurement provides
significant information without need for special
precautions and while making use of conventional
pressure sensors which are merely selected to have
the required sensitivity.
However implanting the sensors (a) or (b) entails
effraction of the dura mater necessitating a far more
complex surgical intervention than that required by
an extradural implant (c) and carries risks well
known to the practitioners; in particular, only the
extradural implant is suitable for danger-free, long-
term surveillance.
In this study, compared with conventional
monitoring, adopted the type of extradural implant, a
pressure sensor based on MEMS was designed for
ICP motoring. Considering minimized size and low
range of sensor, the corresponding finite element
analysis modules of the pressure sensor was set up.
The material and structure design of packaging were
also involved for compliant and stable implantation
purpose.
2 STRUCTURE DESIGN
AND FABRICATION
The ICP monitoring was evaluated at the standard of
2.00KPa, normally, the ICP under 2.00KPa, but the
lightly increased value of ICP is between 2.00KPa to
2.70KPa. Compared with other kind of pressure
sensors, piezoresistive pressure sensors have more
advantages which could satisfy the demand of ICP
monitoring, such as micro size, simplicity
fabrication process and high sensitivity. To fulfill
the requirement of pressure measurement for high
sensitivity and low range applications, this paper
presents a piezoresistive pressure sensor developed
on Si wafers.
296
Bian T., Yulong Z. and Zhuangde J. (2009).
THE DESIGN AND FABRICATION OF IMPLANTED INTRACRANIAL PRESSURE SENSOR.
In Proceedings of the International Conference on Biomedical Electronics and Devices, pages 296-299
DOI: 10.5220/0001777202960299
Copyright
c
SciTePress