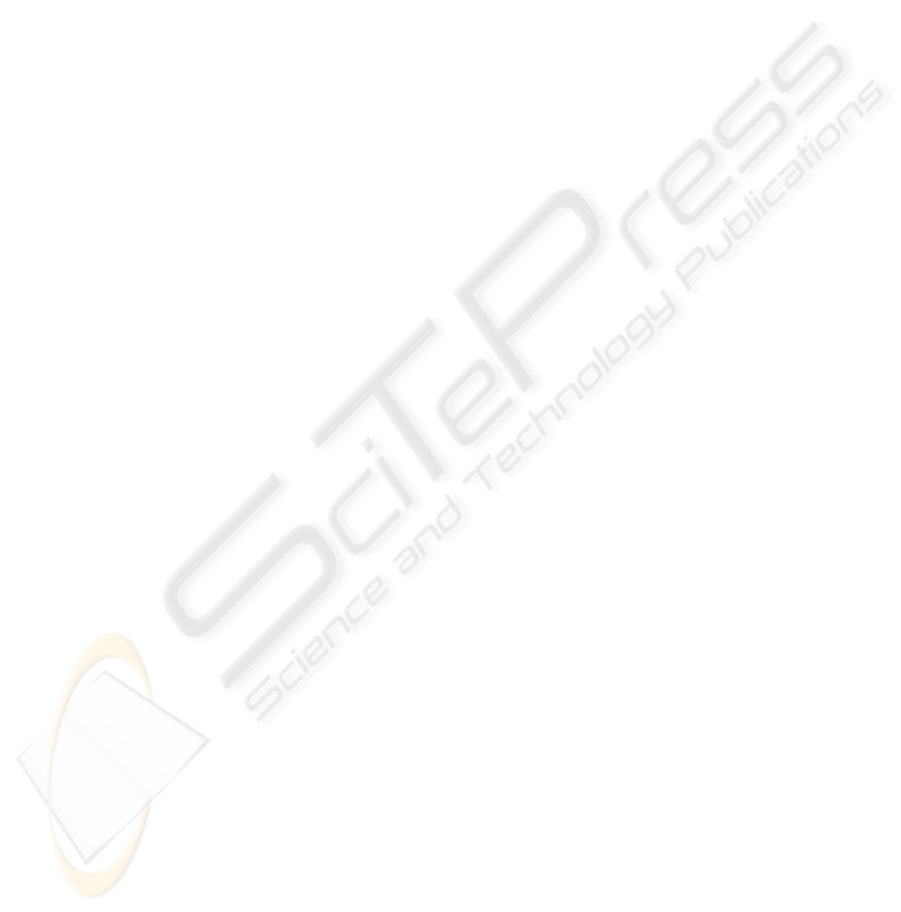
One very common error found in technical literature is the mix-up of the defini-
tions of seal and lock. While the function of the latter is to deter the opening of the
object to which it is applied through its mechanical strenght and robustness, the former
is a device that indicates whether the object has been opened or not. The only physical
strenght that a seal is required to have is one such that it does not break during normal
use.
There exists a wide variety of devices that offer both the seal and lock functionali-
ties, all or in part. For the purposes of this document these hybrid devices will be treated
as seals.
Seals are designed to be tamper-evident. Normally, to determine if a seal has been
tampered with, a visual inspection is required, as the tampering attempt will have altered
in an evident way the physical aspect of the seal. With the use of modern technologies,
though, a new family of seals has surfaced. These are seals that carry on board some
class of electronics, that extends possibilities of seal inspection beyond the normal on-
field visual inspection. These seals are normally referred to as eSeals or Smart Seals.
In literature today there are many different classifications of seals, based on the type
technologythey employ, on physical characteristics, or on the supposed level of security
they offer. In this article we offer the following classification:
Mechanical Seal: a device that carries out the basic function of a seal as described
at the beginning of section 2, based uniquely on its physical characteristics. These
seals can be made of different materials, ranging from plastic, to thin aluminum
foil, to steel in varying degrees of thickness. All these seals share the same sealing
principle, e.g. the fact that they cannot be opened and closed back again with-
out leaving evidence behind. This evidence is detected at inspection time, through
manual inspection. The identity of these seals is established through the use of a
unique identity number embossed on the body of the seal itself. Alteration of this
number should not be possible without leaving evidence behind. If a seal is made
of two detachable parts, the identity number should be embossed on both parts, to
avoid malicious mixing of parts from different seals.
Smart Seals: the definition of this family of seals is very generic, they include any seal
that has a form of intelligence built in that extends the functionality of mechanical
seals. They are usually able to give more information regarding their status, and
allow a number of additional ways of carrying out inspection. For example, a steel
seal could be molded with a technique that introduces random imperfections in
its internal structure that renders each seal unique, thus giving each seal a unique
”signature”[7]. This signature can then be verified through the use of ultrasonic
inspection. These seals are usually designed to alter their signature in a known way
when removed.This way they fulfill the definition of seal in that they carry evidence
of tampering attempts and a unique identity. Other smart seals include devices that
use different technologies to assess their status. These technologies include, but are
not limited to, pressure sensors, thermocouples, Speckle signatures [8], holograms,
radio frequency identification (RFID).
eSeals: this is a particular category of Smart Seal that deserves a special definition due
to their unique characteristics and potentialities. For the purposes of this article and
the definition of seal given here, eSeals are seals based on active, passive or mixed
9